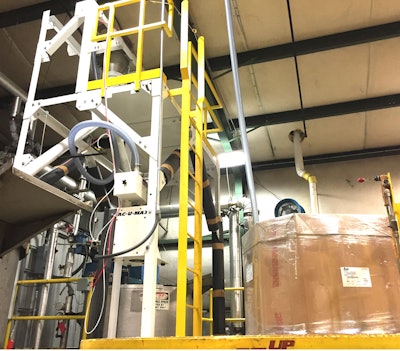
A common dilemma in the industrial world is the manual transport of bulk materials, often to raised platforms where workers dump ingredients into hoppers. This arrangement can produce ergonomic challenges and fall hazards. These ergonomic hazards can lead to work-related musculoskeletal disorders (WMSDs) that include a variety of conditions affecting muscles, bones and joints.
Although the number of WMSDs has steadily decreased since 1994, according to the Bureau of Labor Statistics they still account for 32 percent of all injury and illness cases. Additionally, manual material handling is among the top three tasks incurring the highest number of WMSD cases.
Implementing engineering controls, where physical change is made to the workplace in eliminating or reduces exposure to hazards at the source, is the preferred method to control hazards, according to OSHA’s hierarchy of hazard controls pyramid.
“We are always looking to improve worker safety by implementing a variety of controls, and each year we generally have one large project that we can engineer the risk out of,” says Ryan Cooley, Regional Environmental Health & Safety Manager for International Converter, a leading manufacturer of industrial laminates and sealant coatings.
One of last year’s largest safety projects was automating the process of transferring wax beads into melting tanks at the Iuka, Mississippi plant that produces products for the construction and graphics industries. Previously, 40-lb. bags containing wax beads were stacked on a pallet and lifted onto a mezzanine level above two melt tanks. Then two workers would cut the ends open with utility knives and dump the bags into heated tanks.
“It was a poorly designed process, ergonomically, to have people manually moving those 40-lb bags whenever we needed to fill a tank,” says Cooley. “So it became a priority to find another way.”
Organizationally, it was determined that a pneumatic conveying system would be the best solution. Pneumatic conveying systems use vacuum to move materials from point to point. When the time came to choose a pneumatic conveyor manufacturer, Cooley contacted the Memphis, TN office of Jim Robbins and Associates (JRA). JRA’s Vice President, Walker Robbins, suggested VAC-U-MAX due to the manufacturers’ extensive experience with wax pellets and glue chips.
Although the process of conveying the wax chips is fairly straightforward, “there are a lot of people that wouldn’t know how to handle this type material,” says Robbins. “VAC-U-MAX has had equipment with other wax applications like Candle-Lite and JB Fuller, so knowing what type of wax it was and knowing how it would behave was a bonus.”
Typically, the melting point of wax poses some challenges. Wax that melts at very low temperatures becomes sticky and adhesive, requiring provisions to ensure the wax melts in the tank and not in the equipment conveying it.
Although all pneumatic conveying systems require some human interaction, the first system iteration came as close to a fully automated as possible. It featured an automated super sack unloading equipment and dual material receivers to facilitate the delivery of both gloss and matte wax beads to their respective tanks.
The cost, however, was outside of what Cooley had to work with, “so we started looking at this a few different ways,” says Robbins. “That is the thing about pneumatic conveying equipment, just like there are 100 ways to skin a cat, there are numerous ways to engineer systems.”
Although the automated bulk bag unloader would have further reduced worker interaction in the process, it did not add a whole lot to the package otherwise. On average, the company operates three shifts five days per week, and transfers 1,500 lbs. of wax beads per shift. If International Converter wanted to increase throughput, or had higher volumes of material to move, then the bulk unloader would have been a more viable option.
Since the amount of pellets moving through the system was a lower capacity, rather than using a bulk bag unloader, the manufacturer proposed that workers use a wand to suck material out of the super sac rather than suspending it. Although it is more labor intensive than using a bulk unloader, using a wand to remove material from bulk vessels eliminates the exertion, repetitive motion, and awkward positions that occurred with the manual handling of 40 lb. bags, and has the same outcome as using a bulk bag unloader.
A gravity diverter valve was also implemented, which acts similar to a splitter valve facilitating the use of one receiver instead of two. A blade inside switches from one direction to another, allowing material to be diverted to the appropriate tank. Still on a mezzanine level, the pellets are transferred, via wand, from a Gaylord up 20’ to the receiver.
Where it used to take two workers per shift, “now one person can do it, allowing us to utilize these employees for other tasks,” says Cooley.
To protect the conveying equipment from the heat rising from the melting tanks, a Sparge Ring provides some isolation from the process. Sparge rings are transition pieces with small fittings that create positive pressure and are used most often with heat sensitive equipment or vapor control.
Previously, when workers were handling the bags manually, some of the beads inevitably ended up on the floor, making them unusable. With the new system says Cooley, “everything is enclosed so we don’t spill the wax beads.”
Since the system is so new, Cooley hasn’t had time to accurately calculate the savings, but says, “the system has eliminated a lot of risk for us and that was the primary goal. Because this is now a one-person job, the machine is no longer shut down to load wax. The avoidance in downtime and mitigation of the risk of injury will easily pay for the system in a short period of time.”
For more information about he company's offerings, visit www.vac-u-max.com.