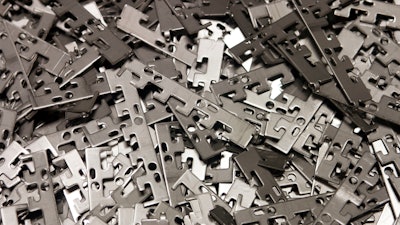
Metal stamping is a complex production process comprised of many different forming techniques, such as blanking, bending, and piercing.
Whether selecting high-quality materials or employing important secondary processes, manufacturers can make use of various techniques to ensure they achieve reliable, quality stamped metal parts and geometries. To cut down on production costs, some companies skip these steps.
But by selecting cheaper materials or forgoing important finishing services, manufacturers often end up sacrificing product quality for cost efficiency. Below are five important manufacturing tips to keep in mind that will help keep costs down without compromising quality.
Tip 1: Identify Potential “Mismatch” Cuts
When designing new progressive die tooling, manufacturers should always speak with the customer about where the part will be carried in the strip as it’s carried through the die.
A slight cut-in or bump-out detail (usually about 0.005 inch deep) will help avoid a “mismatch” cut when the part is cut away from the strip. In many cases, mismatch cuts can result in defective parts.
Tip 2: Provide Extra Material for Designs with Bends
If a part’s geometry requires a bend close to an edge, areas along the edge should be reinforced with extra material. This added material should be at least as much as the radius of the bend.
If this can’t be done, relief notches can also be added, which should be at least twice as wide as the material thickness and as long as the bend radius plus the thickness. Without extra material or notches, bends can come too close to the edge and tear the part.
Tip 3: Consider Coining Instead of Deburring or Edge Grinding
Coining involves striking the edges of a stamped metal part in order to flatten and break off any burrs. The resulting edge is stronger and has a much smoother finish, saving manufacturers money on costly secondary processes such as vibratory deburring and edge grinding that would achieve the same result.
Tip 4: For High-Strength Materials, Design Bends Against the Grain
Because high-plasticity materials are easy to form, bends usually aren’t a concern, but higher-strength materials such as stainless steel and tempered metals can crack when bent along the grain, weakening the overall integrity of the part.
To avoid failure when working with these high-strength materials, it’s important to design bends against the grain of the material.
Tip 5: Understand How Fracture Angles Impact Measurements
The downward stress applied when shearing the edge of a material can cause fractures called “stamping burrs.” These burrs — which occur when the metal splits after meeting its maximum strength at a cut location — create an angle that can alter the part’s dimensions.
In order to accurately design for tight tolerances, manufacturers must consider the height of the burr and the angle and depth of the fracture.
When in Doubt, Consult the Experts
The stakes are high when you’re mass producing complex parts. A custom metal stamping expert will be able to offer a full staff of experienced design engineers to ensure your project runs smoothly and efficiently.
Ron Delfini is the president of ESI. To learn more actionable tips about mastering metal stamping design, download ESI’s free stamping design guide.