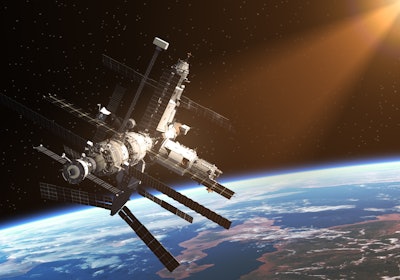
Manufacturing has witnessed transformative revolutions throughout history: from steam-powered mills to automated assembly lines to digital-age precision. Now, we stand at the threshold of perhaps the most audacious industrial leap yet: building factories not on Earth, but floating hundreds of miles above it in the vacuum of space.
This isn't science fiction anymore. Companies like California-based Varda Space Industries and UK-based Space Forge are actively developing orbital manufacturing platforms. Varda has raised $145 million in total funding and is valued at $500 million as of 2025, while Space Forge has secured $30 million to launch the first orbital semiconductor factory this year, marking a pivotal moment where space-based production transitions from experimental concept to commercial reality.
Manufacturing in space offers distinct physical advantages that are difficult or impossibly expensive to replicate on Earth. The orbital environment provides three game-changing conditions that could revolutionize how we produce the world's most valuable materials.
Microgravity: The Perfect Manufacturing Medium
The absence of gravity creates an ideal environment for precision engineering. On Earth, molten metals sink due to density differences, bubbles rise through glass during formation, and crystal growth occurs unevenly as heavier particles settle. In microgravity, these gravity-induced defects disappear entirely. Materials can form with unprecedented uniformity and structural perfection, leading to stronger alloys, flawless optical components, and crystals with dramatically reduced dislocation densities.
This isn't theoretical. Semiconductor sales are estimated to reach over $700 billion this year, and fabrication in space could reduce the number of gravity-induced defects from contaminants while increasing output. The precision possible in microgravity opens doors to manufacturing materials with properties that simply can’t be achieved under Earth's gravitational constraints.
Vacuum Conditions: The Ultimate Cleanroom
Space provides an inherent vacuum environment, eliminating atmospheric gases, dust, and contaminants that plague Earth-based manufacturing. This natural cleanroom eliminates the need for the complex, expensive facilities required for high-precision manufacturing on Earth, where maintaining particle-free environments can cost millions of dollars in infrastructure alone.
For industries requiring extreme purity, like semiconductors, pharmaceuticals, and optical components, this contamination-free environment represents a fundamental advantage. Manufacturing processes that demand sterile conditions can operate in space's natural vacuum without the constant battle against atmospheric interference.
Stable Thermal Conditions and Radiation Access
The stable thermal environment of space, combined with the lack of gravity-driven convection, allows for precise control of temperature-sensitive manufacturing processes. Additionally, the exposure to space radiation can be harnessed for specific high-energy applications, such as promoting particular types of crystal formation or enabling radiation-assisted chemical processes impossible to safely conduct on Earth.
These combined advantages create manufacturing conditions that aren't just better than Earth, they're fundamentally different, opening possibilities for entirely new classes of materials and products.
The first generation of space factories will focus on ultra-high-value materials where the unique properties achievable in orbit justify the costs of space-based production. These aren't everyday consumer goods, but rather specialized materials that could transform entire industries.
Super-Efficient Semiconductors: The Crown Jewel
Space Forge is pioneering the production of semiconductor supermaterials that could revolutionize computing efficiency. In the microgravity and vacuum of space, it's possible to create crystals from new chemical compounds with significantly higher purity, up to five orders of magnitude cleaner than Earth-produced equivalents, and dramatically lower dislocation density.
These space-manufactured semiconductors could enable devices to operate faster while consuming over 50 percent less power, potentially saving billions in energy costs across applications from consumer mobile devices to artificial intelligence systems. The company estimates that such high-grade semiconductor material could be worth just under $62 million per kilogram, easily justifying the costs of orbital production and return to Earth.
Flawless Optical Fibers: Supercharging Global Communications
ZBLAN fiber optics have been one of the earliest breakthrough applications. This fluoride-based glass material achieves superior transmission properties compared to traditional silica fibers when manufactured in microgravity, where the imperfections common in Earth-based production are eliminated.
The result should be dramatically increased internet speeds and reduced signal loss over long distances, potentially transforming global communications infrastructure.
Advanced Pharmaceuticals and Bioprinted Organs
Microgravity enables proteins and crystals used in drug development to form more effectively, potentially improving treatment efficacy for a range of medical conditions. Life science company Varda's W-1 capsule was the first commercial spacecraft to land on U.S. soil when it returned in February, demonstrating the viability of manufacturing and returning pharmaceutical samples from orbit.
Perhaps most revolutionary is the potential for bioprinting human tissue and organs in space. On Earth, these complex biological structures often collapse under their own weight during the printing process. Microgravity allows for precise positioning of cells and biological scaffolds without structural integrity issues, laying the groundwork for future organ transplants and regenerative medicine applications.
Specialized Materials and Future Infrastructure
Beyond these flagship applications, space manufacturing could produce stronger metal alloys for aerospace applications, precision optics for telescopes and scientific instruments, and novel energy-efficient materials for advanced displays and solar panels.
Looking further ahead, there's enormous potential for manufacturing satellites and their components directly in space, bypassing the size and weight constraints imposed by rocket launches while dramatically reducing associated costs.
How Will Space Factories Operate?
Space-based manufacturing is inherently automated due to the extreme costs and risks of maintaining human crews in orbit. This automation-first approach is driving innovations in robotics, manufacturing technology, and remote operations that will likely transform Earth-based manufacturing as well.
Robotic systems are absolutely critical for building, inspecting, maintaining, and assembling orbital facilities. These systems must operate with minimal human intervention, requiring advanced artificial intelligence and machine learning capabilities to handle unexpected situations and make real-time manufacturing decisions.
Companies are developing specialized space robotics, building on proven technologies like Canada's Canadarm series. The next generation includes contributions from firms such as Motiv Space Systems, Maxar Technologies, GITAI, Astrobotic, and Oceaneering Space Systems, each developing robotics solutions specifically designed for the unique challenges of space-based manufacturing and assembly.
Traditional Earth-based 3D printing faces unique challenges in microgravity and vacuum conditions. The University of Glasgow has developed a patented system that uses granular materials instead of traditional filaments, overcoming issues like breaking or jamming that plague conventional 3D printers in space.
This technology could enable the in-orbit production of large structures like solar reflectors for 24/7 clean energy generation and massive communication antennas that would be impossible to launch from Earth. NASA has allocated over $38 million to space manufacturing projects, with eight projects receiving up to $21 million this year, demonstrating the agency's commitment to advancing space-based manufacturing capabilities.
The European Space Agency has successfully demonstrated metal 3D printing on the International Space Station, proving that astronauts can manufacture essential tools, replacement parts, and structural components on demand, reducing reliance on expensive and time-consuming resupply missions from Earth.
The current generation of space factories are compact, automated satellites about the size of a refrigerator, controlled remotely from Earth. These Factories-in-Space (FiS) platforms operate above the Kármán Line (the boundary between Earth’s atmosphere and space, roughly 62 miles above sea level), executing autonomous or semi-connected in-space servicing, assembly, and manufacturing processes.
Safe and affordable re-entry capabilities are crucial for returning finished products to Earth. SpaceX has grabbed headlines with its rockets’ abilities to return to Earth safely. Space Forge has developed the Pridwen heat shield, a lightweight, origami-style design that protects payloads during atmospheric re-entry before a gentle ocean splashdown.
These recovery systems must protect delicate manufactured goods from the extreme temperatures and forces of re-entry while keeping costs low enough to maintain the economic viability of space-based production.
Space factories face unique cybersecurity challenges that extend far beyond traditional Earth-based manufacturing concerns. The Space Information Sharing and Analysis Center recorded more than 100 attempted cyberattacks on space systems each week in 2024, highlighting the growing threat landscape that orbital manufacturing platforms must navigate.
These facilities require robust defense-in-depth cybersecurity architectures that protect against everything from ransomware attacks and satellite kidnapping to jamming, spoofing, and data hijacking attempts.
The implementation of cybersecurity for orbital factories must follow risk-based, cybersecurity-informed engineering principles, with systems designed to continuously monitor, anticipate, and adapt to mitigate evolving malicious threats. Zero trust is already crucial for manufacturing, but it becomes especially critical when a cyberattack could cause the factory to go hurtling off into space or crash into Earth.
This includes securing communication links between ground control and orbital platforms, protecting autonomous manufacturing processes from interference, and ensuring that valuable intellectual property and production data remain secure during transmission back to Earth.
Is the Dream Viable?
The economics of space manufacturing have fundamentally shifted in recent years, transforming what was once prohibitively expensive into an increasingly viable proposition for high-value products.
Setting up factories in space requires significant initial investments and faces ongoing challenges related to technical reliability, the complexities of safe re-entry, and equipment hardening against extreme temperatures and radiation exposure. The harsh environment of space demands robust, redundant systems that can operate for extended periods without human intervention.
However, the economic equation has changed dramatically due to several converging factors that make orbital manufacturing increasingly attractive.
The advent of reusable rockets, pioneered primarily by SpaceX, has significantly reduced the cost of space access, making orbital manufacturing economically viable for the first time. Launch costs that once measured in tens of thousands of dollars per kilogram are now approaching hundreds of dollars per kilogram for some applications.
The immense value of space-produced materials easily justifies these costs. Just look at those semiconductor 'seeds' from Spacer Forge valued at up to £45 million per kilogram, meaning even a small successful production run can generate returns that dwarf launch and operational expenses.
Space-based production promises to reduce environmental damage on Earth by shifting heavy industrial processes off-world, leading to significantly less terrestrial waste and pollution. The healthcare implications are equally compelling: purer drugs, more effective treatments, and the potential for bio-printed organs could transform medical care globally.
Despite rapid progress, significant hurdles remain before space-based manufacturing becomes routine. The increasing problem of space debris and collision risks poses ongoing safety challenges for orbital facilities. Legal and regulatory uncertainties regarding ownership, liability, and resource rights in space require resolution as the industry scales.
The technology demands for highly autonomous systems capable of operating without continuous human intervention continue to push the boundaries of robotics and artificial intelligence. Each space factory must essentially function as an independent, self-maintaining facility for months or years at a time.
However, the foundation for orbital manufacturing is being laid rapidly. While currently only ultra-high-value items justify the costs and complexities of orbital production, this equation is changing as technology improves and space infrastructure matures. Continued innovation, sustained funding for in-space demonstrations, and robust public-private partnerships will prove crucial for transitioning from experimental missions to routine commercial operations.