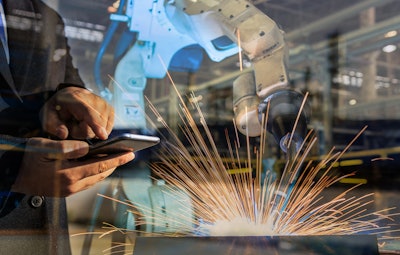
The future of manufacturing is here. Digital Twins have already transformed how manufacturers build, maintain, and optimize their assets, reducing downtime by 20-30 percent and improving efficiency by 10-15 percent. With the integration of Generative AI (GenAI), this technology is poised to unlock unprecedented levels of foresight, flexibility and operational excellence.
By integrating GenAI with digital twins, manufacturers can achieve faster design cycles, a predictive maintenance accuracy of up to 90 percent, and energy savings of 15-20 percent. However, implementing this transformative duo requires careful attention to ethical practices, workforce impacts and decision-making transparency.
Why Data Alone Won’t Deliver Factory Intelligence
Industrial operations today face challenges ranging from managing geographically dispersed assets to minimizing downtime costs. However, fragmented systems and legacy equipment often hinder a unified view, making it difficult to explore "what-if" scenarios or identify early-stage risks.
While data-driven predictions can provide valuable insights, they often fail to capture the nuances of asset behavior or meet dynamic performance goals. By combining physics-based models with AI, manufacturers can achieve deeper insights.
A digital twin strategy is one that combines physics-based models with advanced AI to provide such insight. Using a hybrid approach—blending detailed simulations with machine and deep learning—can help speed up development and improve how assets perform, leading to more efficient and resilient operations.
Together, digital twins and GenAI are forming a powerful pairing: AI can accelerate the rollout of digital twins, while digital twins can refine and verify AI output. Innovators in the manufacturing space are leveraging new capabilities to simulate product behavior and even predict outcomes.
There are several benefits and use cases that manufacturers are starting to develop from combining the technologies:
Track assets in real-time to improve factory output. Firstly, tracking live assets via a hybrid modeling approach helps to boost productivity and performance across industrial operations. By combining data-driven optimization with continuous monitoring, organizations can spot issues early and improve decision-making. A centralized asset-monitoring intelligence center also connects the infrastructure, apps, and people to power faster, smarter decisions on the ground.
Train faster and fix sooner with immersive technology. Augmented and virtual reality (AR/VR) technologies, powered by live data and integrated into AI digital twins, enable workers to carry out maintenance remotely when experts are stationed further afield. These field assistants can guide on-site teams in real time, helping to resolve urgent issues faster and minimize downtime. Immersive tools can also be used for training, including maintenance procedures and health, safety, and environmental protocols, without significant day-to-day disruption.
Monitor factory health to predict failures before they happen. Your AI, digital twin duo can monitor the condition of critical subsystems and estimate their remaining lifecycle. By integrating existing field instrumentation, these simulations generate complete datasets that support better predictions and more accurate tracking of asset health. This makes it easier to replace parts before they fail, sustaining output and helping you manage any spare inventory more efficiently.
Power smarter decisions with connected sensor infrastructure. At the core of all these capabilities is a robust cyber-physical system—a powerful framework of sensors, software, and services. These systems operate across four layers: connect, collect, consume, and cognition. Together, they help bridge the gap between physical assets and digital environments, starting with raw data and ending with actionable insights.
Overcoming Barriers to GenAI and Digital Twin Integration
While the powerful combination of GenAI and digital twins promises transformative potential, several hurdles must be addressed to ensure wider adoption and sustainable value creation.
Human-Centric GenAI. While digital twins powered by GenAI can upskill employees through immersive training and intelligent insights, some workers remain apprehensive about job displacement and the diminishing role of human intuition in problem-solving. To build trust, manufacturers must position GenAI as a collaborative tool that enhances worker capabilities rather than replacing them, ensuring people remain integral to operational decision-making.
Trust and Oversight. As GenAI takes on more responsibility in generating operational recommendations, fostering trust in its decisions becomes crucial. Engineers and operators may hesitate to act on GenAI insights without clear accountability or traceability. Implementing explainable AI (XAI) frameworks tailored for GenAI can ensure transparency in decision-making, enabling operators to understand and validate AI-driven outputs confidently.
Data Quality and Infrastructure. GenAI and digital twin systems rely on high-quality, real-time data for accurate simulations and predictions. However, fragmented systems, legacy equipment, and inconsistent data collection remain common barriers. Deploying scalable cloud platforms, IoT-enabled retrofits, and robust connectivity frameworks can address these gaps, ensuring the data infrastructure required for GenAI and digital twins is reliable and future-ready.
Ethical Challenges. The ethical use of GenAI in manufacturing raises critical questions around bias in generated insights, misuse of worker data, and compliance with evolving regulations. Manufacturers must proactively establish governance frameworks to guide GenAI usage, ensuring alignment with global standards like the EU’s AI Act. By prioritizing ethical practices, they can mitigate risks, build trust, and foster responsible innovation.
The Factory of the Future, Today
Ultimately, manufacturers looking to get the most out of their AI, digital twin combo should look to a specialist partner to help them navigate the complex integration. With experience across industrial automation, connected systems, and AI-driven software, these partners can guide factories through the entire transformation journey, from building the right infrastructure to developing transparent, trustworthy AI models.
After all, the next era of productivity will belong to manufacturers who can simulate outcomes before they unfold, identify issues before they disrupt, and empower their people to work alongside AI, not around it. With the right infrastructure and expertise, manufacturing leaders can move from reactive to predictive, from efficient to exceptional.