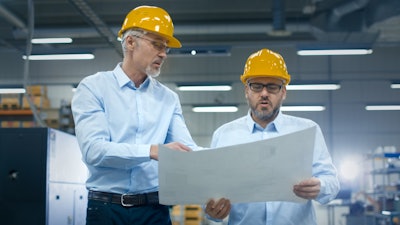
Walk into a modern factory in 2025 and you’ll see computer-vision cameras inspecting parts, collaborative robots ferrying materials down the line, and cloud dashboards predicting maintenance hours before a fault. So, what function do humans have in these manufacturing processes?
Well, plenty. Despite how sci-fi manufacturing can feel these days, there are still limitations and problems that AI and automation just aren’t equipped to deal with. When problems arise, it’s human that will need to be able to work out how to deal with them. And while technical skills can be important in these scenarios, it’s soft skills that will allow them to identify issues, find solutions, and collaborate effectively.
Why AI and Automation Make Soft Skills Essential
It’s no secret that industrial automation has been rolled out at breakneck speed, and will likely continue to do so. The International Federation of Robotics counted 4.28 million industrial robots active worldwide in 2024, up 10 percent year-on-year. Annual installations have topped half a million units for three years running, and World Economic Forum data show that 58 percent of manufacturers plan to scale robotics by 2030.
Routine tasks are increasingly handled by cobots or AI-driven inspection systems that never tire or deviate, which should free employees to focus on higher-value analysis and improvement.
The Human Advantage in an Automated World
Even the most advanced neural network lacks intuition, ethics, or empathy. When a predictive-maintenance system suggests shutting a line, someone must weigh up the safety concerns, customer deadlines, and opportunity cost. If a chemical hazard occurs, AI might be able to flag it has happened, but it won’t necessarily know what to do about it. It’s soft skills that turn data into decisions.
It’s also worth noting that well-developed soft skills often include an ability to learn, adapt, and evolve. With automation and AI continuously making roles obsolete or drastically changing the nature of existing roles, the ability to adapt will also be a great advantage for both employees and employers.
Manufacturing’s macro challenges underscore the need for soft skills. Electrification, supply-chain volatility, and decarbonisation all demand cross-functional collaboration as much as coding.
Perhaps most critically for business leaders, Deloitte projects a shortfall of 1.9 million U.S. manufacturing workers by 2033 if talent development stalls, with the fastest-growing roles blending technical, digital, and soft-skill requirements, meaning we need to start cultivating soft skills in the manufacturing workforce now.
Essential Soft Skills for Manufacturing
- Communication. Production lines fail when hand-offs falter. Communication, whether it's spoken, written, or visual, keeps multi-shift teams aligned on tolerances, changeovers, and, now, AI outputs. The need is backed by data, as 31 percent of manufacturing businesses name ‘communication’ as the number-one soft skill for new hires. Active listening, clear explanations of sensor data, and culturally aware body language shape everything from daily Gemba walks to board-level cap-ex pitches.
- Problem-Solving and Critical Thinking. When a vision system starts flagging false defects, it’s up to human workers to hypothesize, test, and identify the root cause. Critical thinking also tempers AI outputs, probing for biases or improbable correlations before decisions are made. As a result, Deloitte’s 2025 outlook stresses that analytical thinking and problem-solving top employers’ wish lists as they scale smart-factory investments. In practice, this means teaching technicians basic statistics, fault-tree analysis, and, above all, the courage to challenge a machine-learning model if its suggestion contradicts experience, and being able to back that challenge with data.
- Adaptability and Flexibility. The production environment never sits still: there’s always new composite materials, new ERP modules, new safety rules, and more to stay on top of. still. Automation and AI aren’t at the point where they can actively adapt to changes without instruction (yet). So new regulations or processes are introduced, it’s human workers who will work out how to adapt and change the current systems to align with the needs of the business.
- Teamwork and Collaboration. Teamwork and collaboration are fast becoming production metrics in their own right. Factories pairing new tech with cross-functional collaboration unlock the biggest productivity gains. In fact, embedding collaborative workflows into root-cause analysis, supplier management, and maintenance can raise output by 20 to 30%. Smart-factory teams that share data and decisions across functions are not only more productive but also markedly better at attracting talent, an edge manufacturers need as the skills gap widens.
- Leadership and Decision-Making. AI planning tools can propose scenarios, but humans still choose. Effective front-line leaders can translate algorithmic recommendations into safe, ethical actions and then communicate them with clarity. These leaders mentor apprentices, arbitrate in diverse teams, and champion continuous improvement, all of which are essential skills that AI and automation are unlikely to be appropriate substitutes for any time soon.
Other Crucial Traits
Accuracy matters when a 0.02 mm error scraps a turbine blade, so attention to detail remains vital. Emotional intelligence eases conflicts between veteran technicians and digital natives. Creativity sparks process innovations that AI could never suggest. And reliability, showing up, following through, keeps takt times intact and customers happy.
Soft-skill cultivation begins at the start. Behavioral interviews, role-play simulations, and psychometric tools surface candidates’ communication and adaptability before they put on safety glasses. Ideally, you (along with 82 percent of manufacturing hiring managers) want to find ways for your candidates to demonstrate (not just talk about) soft skills during recruitment.
Training shouldn’t end at onboarding. Not only is it a means for cultivating soft skills, it;s essential for talent retention, with 88 percent of professionals citing it as the top retention lever. You can even gamify soft-skill learning: operators can earn points for mentoring peers or leading a quick workshop, then spend those points on advanced course credits, turning culture change into a game everyone can play.
Pairing a senior engineer with a new starter can accelerate knowledge transfer while honing the mentor’s empathy and feedback muscles. Cross-generational mentoring is especially helpful as it can create a two-way loop of development: the veterans can share their insights and expertise on how to navigate problems, while younger, more tech-savvy hires can help their older counterparts gain digital fluency, and both sides practice listening and coaching.
Soft skills atrophy in cultures that don’t encourage them. Psychological safety can be incredibly important for encouraging soft skills, as workers need to have the freedom to flag near-misses without fear, discuss 360-degree feedback loops, and cross-cell kaizen events that reward joint wins.
AI and robotics are rewiring factories, but they haven’t rewired the essence of work: humans collaborating to solve novel problems. Robots may top four million worldwide, yet leaders still warn of nearly two million manufacturing roles going unfilled without the right blend of technical know-how and soft-skill excellence. The evidence is clear: communication, critical thinking, adaptability, and leadership aren’t ‘nice-to-haves’. They’re production assets are as real as any robot arm.