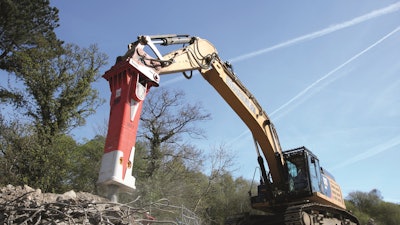
Worsley Plant was established in 1996 as a contract crushing company, processing stone at rock face or demolition sites on a pay-per-metric-ton basis. The company’s job was to crush stone and remove it, and the very nature of the work requires a heavy capital investment for very tight margin returns. Hence, any breakdowns and consequent downtime can be very expensive in terms of losses, and equipment costs and size meant that only jobs of over 3,000 tons were economically viable with such large machinery.
In 2003, the company identified a gap in the market for smaller jobs involving crushing buckets attached to excavators. Worsley Plant employed these successfully, and later then went on to sell these crushing buckets to end users following demonstration. By 2006, equipment had become more advanced and so the company established a relationship with Webtec, manufacturer of hydraulic controls and testing equipment, which began with the purchase of portable hydraulic testers. By 2007, the traditional large scale crushing business was sold, and the company’s sole focus became selling and hiring crushing buckets via a dealer network.
For Worsley Plant, an integral part of the installation is making sure the excavator is set-up correctly for the bucket to do its work. If the excavator isn’t set properly, then the bucket won’t function to specification, and the user may assume that the crushing bucket is at fault. All sales therefore include training and commissioning during which a Webtec flow tester is used to test the hydraulics.
Excavators have, in the last few years, become far more efficient and geared toward carrying attachments, whereas five years ago an excavator was only an on-site digging tool. Now that it is more of a tool carrier, it comes ready with hydraulic circuitry to control a wide range of rotating, vibrating or sorting attachments, and the pumps are more efficient. The demand for flow from the excavator to the attachment has increased, so now there is a need to test not only the inlet flow, but also the outlet flow as the ‘regeneration’ on some attachments with 400 lpm in, could result in 800 lpm out, for example. Hydraulic back pressure needs to be tested too, so not just how much flow is coming in, but that the hydraulic system is efficient and can achieve the working pressures that are required for the bucket to operate correctly. The larger 800 lpm Webtec tester enables Worsley Plant to do this easily.
The company seeks improvements all the time, and finds that the best way to ensure top performance is to carry out the installation and commissioning on behalf of the client. They must ensure the equipment is working correctly by adjusting the required hydraulic flow and pressures, then testing the back pressure prior to connecting the crushing bucket and demonstrating how to operate it. The approach shows Worsley Plant’s professional customer service. They turn up, they know what they’re doing, they have the right tools for the job and they do it.
For more information, visit www.webtec.com.