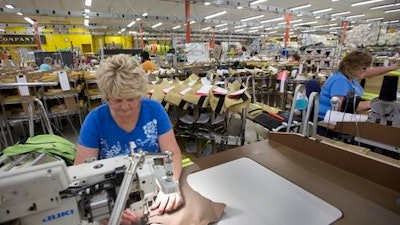
CONCORD, N.H. (AP) — In a small town just south of New Hampshire's capital, General Electric runs two plants filled with workers building jet engines for the world's leading airlines.
With 800 workers, GE Aviation is the largest employer in town. But in the next five to 10 years, about a third of those workers are expected to retire. The company is scrambling to not only fill those jobs, but to find workers with the needed skills to take on jobs that are becoming ever more technologically advanced.
It's a problem expected to play out across the region and the country over the next decade, driven in part by the growth of the economy and a rash of retirements among baby boomers.
"What we have found out is that as we raise the bar, we're finding it a little bit difficult to get a pretty good population or a subset of folks that we can pick from to fill those needs," said Peter Haley, a business operations leader at GE Aviation's Hooksett facility.
Nearly 60 percent of New Hampshire's manufacturing workers are over the age of 45, compared to 49 percent nationally, state and federal data shows. And from 2004 to 2014, the number of manufacturing workers in the state between the age of 35 and 44 dropped by nearly half. State projections show about 80 percent of open production jobs in the next decade will be to replace outgoing workers.
On top of that, New Hampshire's 2.8 percent unemployment rate, one of the lowest in the nation, means the labor pool is already shallow.
"We're having to rebuild the entire pipeline of workers," said Katrina Evans, assistant director of the state's Economic and Labor Market Information Bureau. "It's not even so much a skills mismatch as it is a warm body mismatch."
Nationally, a 2015 report from The Manufacturing Institute and Deloitte found that the skills gap "is real, and it is substantial," noting that over the next decade, 3.5 million manufacturing jobs will have to be filled and that the skills gap means that 2 million of those jobs will go unfilled.
Of the CEOs surveyed for the report, 82 percent said that the skills gap would impact their abilities to meet customer demands and 78 percent said it would impact their abilities to implement new technologies and increase productivity.
"The basic consensus at this point is that the shortage of skilled labor is so severe that it's actually affecting the ability of companies to grow," said Val Zanchuk, a manufacturing executive and chairman of a new statewide effort to bridge the skills gap. "This is nationwide, and it's certainly reflected in New Hampshire as well."
But some experts think the nationwide skills gap is overblown.
Elise Gould, senior economist at the liberal-leaning Economic Policy Institute, said federal jobs data shows there are two unemployed manufacturing workers for every available job. She said employers looking for workers could be doing more to train available workers or attract more talent by offering higher wages.
"Actually, there's a lot of unemployed workers in that field that you're trying to hire in," she said, noting that she did not have specific data on New Hampshire's manufacturing sector.
New Hampshire and several other states in the region aren't waiting for the debate to play itself out.
Gov. Maggie Hassan announced this month the creation of the "manufacturing sector partnership," an initiative to bring different manufacturing companies to the table with educators to find out exactly what skills are needed.
In addition, community colleges in New Hampshire and Vermont have also bolstered classes to train students to become computer numerical control machinists — those who run equipment that creates machine parts —or learn skills like tubing that is a critical to building engines. Businesses, too, are starting their own internship and part-time job programs in a bid to convince young workers that manufacturing isn't the dirty, difficult work of their parents or grandparents. Some are even offering hiring incentives to attract prospective workers and considering busing prospective candidates into New Hampshire from out-of-state, like Hitchiner Manufacturing Co., Inc., which already has a short list of towns it would target for employees.
"In the past, manufacturers were passive about it," Zanchuk said. "The hope here is that we can focus the education and training process at different levels throughout the state to prepare the workforce for the particular needs of each industry."