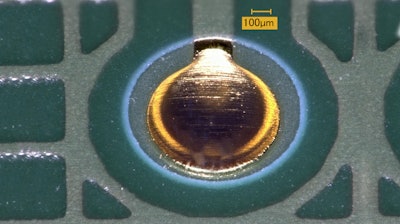
In the course of ever-progressing miniaturization, increasingly small and sensitive components need to be joined together.
Expanding functionality of the components goes hand in hand with increased material mixing and higher quality requirements, making it necessary to provide joining methods that ensure reliable fixing of miniature components.
Bigger Challenges with Smaller Components
Bonding is an ideal solution as it can be used with a variety of different materials and can be applied easily in confined spaces, though bonding of small components does require extreme accuracy. Additionally, manufacturers seek to reduce costs during their production processes by speeding them up.
The challenges faced by microdispensing technology are clearly defined: ever smaller amounts of adhesive need to be dispensed at ever-increasing speed while maintaining a high level of precision.
As technology has advanced in many industries, manufacturers can learn something from the printing industry: dot matrix printers transferring ink to paper by impact were extremely slow and created broad lines. The development of inkjet systems, placing tiny ink droplets without contact on the paper, has significantly increased both speed and resolution.
Jetting Beats Needle Application
The same principles can be used for the dispensing of adhesives by โjettingโ free-flying adhesive droplets from a small distance. The time-consuming placement of a dispensing needle onto the substrate for application of the medium, as is done with traditional dispensing, is no longer necessary. Jetting is therefore much faster and is reflected by higher cycle times.
Jet dispensing can provide accuracy, reproducibility, speed โ with a drop size of just a few hundred micrometers.DELO
Due to the functional principle of jetting, position tolerances of components in z-direction are irrelevant since the free-flying adhesive droplet will reach the substrate surface anyway. Consequently, the risk of collision between needle and component posed during needle dispensing does not exist in jetting mode. As a result, there is no need to perform camera measurements before and after the application process, saving time. The closing mechanism of jet valves prevents unwanted dripping, as can happen with needle valves, thus avoiding dragging of the adhesive.
Needle dispensing still has its benefits. Many companies will opt for needle dispensing when just a few milligrams of adhesive needs to be dispensed with maximum precision. Conversely, jetting is the preferred way of dispensing when the focus is to speed up production.
Technology Choices in Actuators
In the case of jetting, there is a choice between two driving systems for your dispensing unit. The requirements for the actuator generating the pulse pressure for ejecting medium- to high-viscous adhesives are much higher compared to applications with low-viscous ink.
During the closing process, the valve piston moves with high momentum towards the outlet. The dynamic pressure at the piston head allows overcoming the surface energy and the high cohesive forces within the liquid, causing a free-flying droplet to detach from the valve opening. High actuator forces and speeds are important factors in ensuring that the process works.
However, in order to make full use of the speed advantages provided by contact-free dispensing, the valve must be operational most of the time. This is where common systems often fail.
They use either pneumatic actuators with sliding sealing elements that involve friction, or piezoelectric ceramic actuators based on a lever mechanism that are also subject to friction. Friction, combined with high speeds and fragile ceramics, blended with high driving forces lead to severe wear and reduced service life. This partly negates the speed advantage of the jetting method and causes substantial increases in costs.
New Microdispensing Valve Technology
New microdispensing valves rely on pneumatic actuator systems that do not use any sliding or frictional elements. They are extremely robust and have an exceptionally long service life of up to one billion dispensing cycles thanks to the reduced wear on the elements.
Developed for fast serial production processes and long service life: pneumatic microdispensing valves like DELO-DOT PN3.DELO
The new valve also features increased jet performance and allows for many adhesives to be dispensed in significantly smaller quantities. On average, the minimum dispensing volume is reduced by a factor of three. Certain products can be jetted permanently in quantities as small as 2 nl.
Additionally, the maximum dispensing volume per drop is almost 5000 nl, making the valve extremely adaptive in the production process. This is made possible thanks to an optimized fluid system geometry and two different piston types, one for very small dispensing amounts and one for small to medium drop sizes.
Well-designed valves feature a modular design. Because of this design, the actuator is completely separated from the resistant fluid system which, in turn, can be dismantled into individual parts. This allows for easy cleaning of all components that come in contact with adhesives and all relevant areas are easily accessible without any special tool.
To keep system downtimes to a minimum when changing the adhesive, it should be possible to replace the fluid system as a whole. Single components, like the stainless steel chemical-resistant fluid system body, different diameter nozzles with different geometries, as well as the nozzle heater, are available separately and can be quickly and easily exchanged by the user on site.
A modular design with actuator and fluid system separated and fluid parts easy to remove make things easier for manufacturers.DELO
The redesigned nozzle heater guarantees permanently stable temperature and viscosity conditions for the dispensing medium. The built-in thermal insulation of the heater, which has no open electric contacts and is screwed onto the valve, ensures that only the medium-transporting part at the valve outlet is heated, thus reducing the time during which sensitive dispensing media are exposed to a defined thermal load.
Plug & Play Installation
In high-throughput systems, dispensing systems need to be designed as small as possible. The compact outer dimensions of the jetter (min. 20.5 mm ร 153 mm ร 62 mm), in combination with a media supply that can be positioned at a 90-degree angle, enable flexible adaptation to small installation spaces and easy integration into production systems. Mounted on a movable axis, its low weight of less than 350 g is ideal for high travel speeds and ensures an operating frequency of up to 330 drops per second.
When installed, the microdispensing valve is easier to handle. Many parameters can be read from a PCL. A rotary wheel is used to set the stroke of the piston by selecting one of five different locking positions without any additional tool. The respective position is indicated by an LED, making it easier to check the stroke setting after integration into a production system.
Robust, Reliable System
The jet valve features a highly resistant fluid system, separated from a pneumatic actuator. This combination results in an extremely robust and reliable system, guaranteeing a long service life and minimized operating costs. With this new technology, increased production speed requirements can be met while maintaining the precision necessary to ensure a proper adhesion process essential to providing a high-quality product.