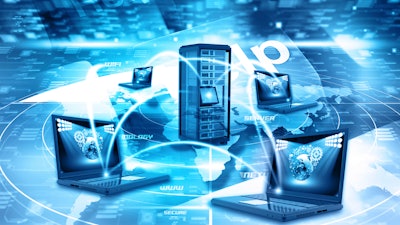
Big data analytics, the Internet of Things, 3D printing, drones, edge computing, wearables, convergence – the list goes on.
These are the drivers of digital transformation. Gartner notes these interdependent trends are “transforming the way people and businesses relate to technology.” Nowhere more so than in the oil and gas industries. Why?
- Because they allow companies to digitize, optimize, and automate processes that were not previously connected.
- The automation enabled via digital transformation opens new doors for workforce and maintenance efficiency.
- Predictive maintenance becomes a possibility with machine learning, as well as the automation of work orders.
- Integrating Wi-Fi and location-based technologies allow for remote monitoring of potential accidents, tracking and tracing personnel in dangerous situations, as well as contractors and equipment utilization.
There are three key technologies catalyzing digital transformation in oil and gas.
1. IoT at Work – Shut-Down Decisions
One particular area of benefit is availability, or the cost of downtime. IoT applications in oil and gas leverage sensors to remotely monitor equipment and make decisions about whether or not to shut it down - a very expensive decision.
Typically, oil and gas companies monitor a fleet of similar equipment from a central unit or control location. When an anomaly is detected, personnel assess diagnostics before a shutdown is ordered. Increasingly, these data monitoring centers are run by equipment providers as part of the support services they contract to oil and gas customers.
2. Going Mobile
According to recent research by Oil & Gas IQ, mobile device management adoption is pacing to reach 80 percent penetration. This is being driven by lower cost of entry for mobile devices and the rise of mobile friendly enterprise applications. The next step is to make enterprise data and functionality available on the mobile device to deliver benefits in two key areas in oil and gas.
The first is project visibility. Managing projects of various sizes and complexity is often the key to success. However, companies still struggle with fragmented business solutions that lack integration, making the projects more difficult to manage. The situation faced by the engineering procurement and construction contractor is even more challenging because recording work performed can often not be done until well after the fact.
Mobile devices offer improved project management and control by providing access to and reporting on critical information in real-time anywhere, anytime. Efficiency and quality is increased for on and offshore maintenance and service operations by enabling field workers to interact with the software as they perform work. Better decision making is enabled because there is less administration and greater data integrity.
The second is asset integrity control. Assets used in the oil and gas industry are mission-critical, and not just for their productive capacity, but because failures can result in environmental damage, loss of life and litigation. This makes asset integrity management (AIM) critical for the industry. This not only means that regularly scheduled maintenance must be performed, but the readiness and serviceability of the asset must be documented on a granular level. Mobility adds value by enabling work performed to be captured in the EAM system more accurately and completely.
3. Converging Technologies Brings Connectivity to the Edge
As operational technologies (OT) increasingly include mobile devices, software and sensors, OT and IT can converge in an environment containing smart machines, storage systems and facilities. While IoT data can be processed at the data center or at the edge of the network, the amount of content that will be generated at the edge will demand process queries be delivered to the point of data entry - rather than the data center. Edge processing could drive innovation in analytics, systems and operational management.
This is particularly key in oil and gas. Consider a typical offshore oil platform that generates between 1TB and 2TB of data daily. Most of this data is time-sensitive, but with the most common communications link - a satellite – it could take up to 12 days to move one day’s worth of data to a central repository.
Digital Requires Some ‘Unlearning’
An Altimeter report with customer experience guru Brian Solis offered some interesting results. Of the companies surveyed, 88 percent said they were undergoing digital transformation efforts, but only a quarter had an understanding of what it is. According to Forbes, the challenge creating this gap was not investment in technology, but rather the realignment of business models.
Traditional enterprise IT can be simply too cumbersome and inflexible to enable oil and gas to realign their business models. To react to these latest advances, organizations need the backing of a new generation of flexible, agile enterprise solutions. Traditional enterprise solutions can take months or years to implement, let alone adapt to an entirely new technology.
The new breed of modular enterprise solutions are designed to remove the time and pain of modifying existing business processes – maximizing the opportunities of new technology.
Digital transformation offers the potential to open up new operational efficiencies, productivity gains, and cost benefits for those companies that successfully make the transformation. But digital transformation of the scale that we are talking is dynamically integrated into the enterprise rather than just bolted on. This approach will provide greater agility and support for innovative products and services.