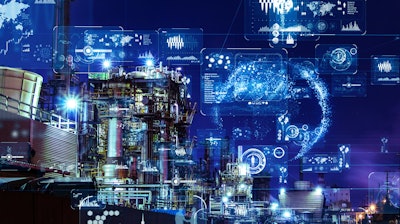
Industry 4.0, Society 5.0, and IoT may be the latest buzzwords in the industrial technology space, but the motivation behind them is beginning to show benefits.
At the core, these concepts are about using digital transformation to address core business cost drivers that are ubiquitous in the manufacturing space by providing for greater data transparency, accessibility and intelligence. To be sure, part of what these concepts promise has been in play for several years – specifically around data collection.
This proposed transformation must result in not just collecting data, but in contextualizing it. Some examples are predictive maintenance, ability to manufacture customized products on a JIT assembly line, and increased worker safety with fatigue detection systems.
Core to digital transformation is adoption of cloud services where it makes sense. For the longest time, limitations in connectivity (latency, throughput, and reliability) have prevented manufacturers from utilizing cloud services for any business-critical applications. While ERP and MES may remain on premise or co-located indefinitely, IT organizations must shift their service delivery approach to provide composable infrastructure to their stakeholders or risk being circumvented. In the worldwide economy of 2023 and beyond, embracing these new technologies is critical to remain competitive.
Currently, many of these technologies are prohibitively complex and expensive, though ROI is becoming clearer. As scale is achieved, small and medium-sized manufacturers will have the opportunity to integrate more technology onto their manufacturing floors – many which are developed with a SaaS or Cloud First approach. Instead of relegating cloud services to secondary business objectives, they should be considered a primary tool or engine that drives all business goals.
The more companies that embrace the cloud now, the better off they will be at predicting and preventing costly downtimes that cause other supply chain bottlenecks.
Performance Tracking and Operational Efficiency
Connected devices have been applied in manufacturing for decades in tasks such as remote asset monitoring. However, the lagging sensor technology that remote monitoring has historically relied upon has limited the abilities of these services, but with the mainstream adoption of wireless technologies, such as 5G in combination with the decreasing cost of sensors, these limitations are becoming less of a factor.
Network-connected wearables for workers make their jobs easier and safer. The data these connected devices produce is being sent to the cloud to run complex data analytics that helps not only track, but improve performance and operations. Digital sensors are faster and more precise than they’ve ever been, but improving data tracking is pointless without an effective tool to analyze the data in real-time.
Artificial Intelligence Helps Process Cloud Data
Artificial intelligence is what powers the real-time data processing that makes it possible to improve safety and productivity. The possibilities are endless — a forklift operator can be directed to the most efficient picking path, fuel filters can remotely measure oil quality, and commodity resources can be reallocated to reduce waste — all in real-time. Predictive maintenance analytics can also help prevent waiting until machinery breaks down and disrupts the supply chain.
The data available for processing is only growing, and failing to use high-powered tools to take advantage of all that data would be a waste. AI helps prevent that. However, the ability to process important data depends on a reliable IT structure.
Smart Applications Boost Optimization
Manufacturing has typically relied on Material Resource Planning (MRP) to facilitate production deadlines. This allows materials to be ordered at the stage of the process when they will be used - so the product is completed on time. This model only works when every order, delivery, and design phase is running precisely on schedule, which has proven particularly unrealistic given how unreliable supply chains have recently proven to be.
Advances in technology have produced smarter MRP options that allow for automated ordering of raw materials and better inventory management. The process has become more integrated with suppliers, so that in the event that any adjustments need to be made, there is open, two-way communication and real-time updates on lead times.
According to Deloitte Consulting, smart manufacturing not only improves asset efficiency by 20 percent, but improves product quality by 30 percent and reduces costs by 30 percent. Increasing digitization and smart application utilization will only get even more appealing as it helps bridge the skills gap in manufacturing and reduces human errors that leads to on-the-job injuries and lost time incidents that cost the manufacturing industry $7 billion every year.
Growth of cloud-based activities will inevitably provoke new best practices that will be challenging to keep up with, but even future shifts can be simplified with the help of companies that specialize in IT infrastructure. As new technologies revolutionize the market, manufacturing companies will have no choice but to prioritize cloud-enabled smart applications, AI, and IoT-connected services.
David Humes is the Director of Product Development at Involta.