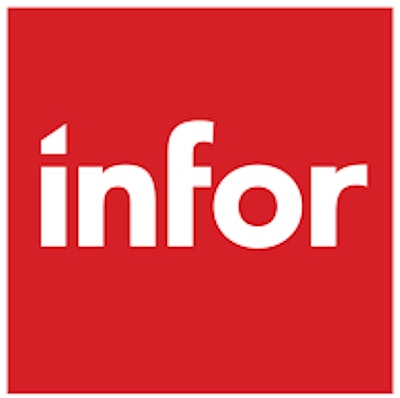
Nearly everyone who designs, builds, fixes, or drives an automobile has heard about the tragic situation involving defective airbag inflators installed in vehicles from several manufacturers. Even as the scope of the recall continues to expand, the airbag supplier and automotive manufacturers who use those airbags are scrambling to identify why they failed to work as intended.
There is a lot of consolidation happening in the automotive supplier community, resulting in multiple original equipment manufacturers (OEMs) using the same component, from the same supplier, across several vehicle models. This provides suppliers economies of scale and improves profit margins. However, it also magnifies the consequences when a defective component – like an airbag – finds its way into this larger vehicle mix.
While the answer as to why the airbags fail to work properly remains elusive, one thing is certain: these airbags failed due to a complex combination of factors, including the airbag design, vehicle design, and environment within which the vehicle was operating at the time of failure.
Investigations like these require thoroughness, efficiency, collaboration and - most importantly - access to accurate information.
Sensors Working Overtime
While access to accurate information from all sources is important, access to vehicle-generated data is absolutely critical for both automobile suppliers and OEMs. This data helps resolve product defects more quickly, improves the design of future products, and informs manufacturing process optimization.
Cars generate lots of data – about 1.3 gigabytes per hour, on average. This information is generated by dozens of sensors installed throughout the vehicle that capture and publish operating performance data of critical components, including airbags. Analysis of this sensor-collected data can help automotive suppliers and OEMs more quickly diagnose product defects. Unfortunately, the little vehicle data analysis that occurs today is performed only by OEMs.
Automotive Manufacturing Ecosystem Impact on Defect Resolution
Although data analytics technologies are readily available for any company to use, all vehicle sensor data is owned by the OEMs. This data isn't gathered or stored in a way that is easy to share with suppliers, meaning OEMs are the only ones with access to analyze the vehicle data. The auto suppliers' inability to access this data prevents them from using powerful analytics tools for defect detection and product improvement.
Auto suppliers are dependent upon OEMs to provide analysis summaries for every make and model where automakers have one of their parts installed. However, the OEMs are free to choose if – and when – they share this information with auto suppliers.
What if the airbag supplier had both the access and tools in place to analyze the data of every vehicle make and model where their product was installed across all of the auto manufacturers? The supplier would soon be able to see trends and patterns that could provide insight into why those airbags failed.
An even better situation would be if the airbag manufacturer had a truly predictive experience with real-time data access, and used analytics tools to proactively monitor their part performance alongside their manufacturing processes to anticipate problems before they occurred. Rather than parsing through all of the data after a part fails – assuming they even receive all the data – the supplier would be able to identify a potential malfunction before it happens, saving costs and lives.
The power of business intelligence doesn't just start and stop at predicting or managing incidents. The information garnered from watching the trends and patterns that may lead to a part recall or failure can also inform adjustments to things at the beginning of the supply chain – including design, materials, and processes. This is possible when auto suppliers have data access and integrate their business intelligence information and supply chain processes within the enterprise resource planning (ERP) system.
The systems and tools exist today to turn data from overwhelming to meaningful, predictive, and useful insights. Analytics tools have the power to help both automotive suppliers and OEMs efficiently improve product quality while saving costs and their company reputation. Now is the time to start ensuring all the OEMs and auto suppliers have access to the necessary data to perform the rich analysis needed for efficient defect resolution.