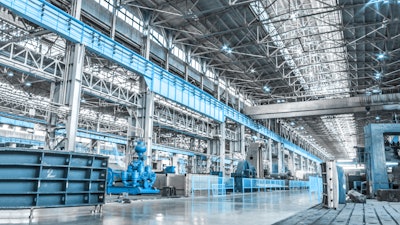
Ownership is a tricky subject. When assessing current or potential employees and managers we target individuals who express a desire to take ownership of a situation or role. A greater sense of accountability, responsibility and buy-in usually leads to more efficient workflow and higher quality outcomes.
The other side of this coin is the potential to become territorial. Instead of welcoming input or ideas, this sense of ownership leads to a grumpy, battle-weary engineer essentially chasing people off his “lawn” with not-so-veiled threats.
Traditionally, IT and operations have played in their own yards, only to converse when the ball accidentally rolled into the others or mom and dad forced them to play nicely. It’s this dynamic that could present the biggest obstacle to expanding operational connectivity throughout the industrial sector.
Dave Vasko is the Director of Advanced Technology at Rockwell Automation, which is one of the founding members of the Smart Manufacturing Leadership Coalition. He sits on the board as the company’s representative. The SMLC is a collection of leading suppliers and manufacturers that Vasko describes as “looking for solutions” when it comes to new, connected technologies and processes for manufacturing.
“With SMLC, we highlight the value in connectivity,” offers Vasko. “Bringing the top floor to the shop floor and the supply chain to the demand chain. The concept is for all our members to share information in developing solutions.” Right now membership consists of about 50 suppliers, organizations and institutions pushing developments in enhanced industrial connectivity.
It’s About Data, Not Feeling Lucky
Vasko cites data analytics as possibly the most important tool for advancing the connectivity cause. It could also be the rally cry that finally unities IT and OT. Although the availability and implementation of software, sensors and other data sources has been a part of manufacturing for decades, the next crucial step will focus on the way the information garnered by these tools is analyzed and who is given access to it.
Property lines need to be erased for this data to truly have an impact. This means the data is owned by the entire enterprise, not segregated amongst different departments. “Contextualization is a critical part of data. Data without context is useless,” offers Vasko.
He continues, “You need to correlate what is being measured, which equipment is being effected and what product is being manufactured at the time of the data capture. We sometimes miss important information because there is so much data to sort through. Manufacturers don’t always realize that some solutions are already there and some problems have already been solved. They don’t have to start from scratch.”
Enter the convergence of IT and Operations Technology. Instead of drawing lines regarding which data belongs to which department, IT and OT can work together in getting a better understanding what all the data means for the entire enterprise. Connections can then be made in terms of how this information effects everything from product development and sourcing through production and into the supply chain.
Once both groups have an understanding of all this data, identifying responsibilities becomes easier. “We recommend training IT on how to connect to OT and vice versa. When both groups understand the whole situation, problems are more easily resolved. Data analytics lends well to getting these groups together because once you show how understanding and sharing data can help reduce inventory, improve lead times, etc. - it’s a much easier sell,” states Vasko.
Still, paradigms that challenge such collaboration persist and can delay critical actions from being taken. Be warned that the negative ramifications of waiting to bring these two factions together can produce a lapse in deeper data analysis. This will slow the development of solutions for reducing downtime or enhancing preventative maintenance approaches that could streamline profit centers.
I concluded my conversation with Vasko with a question I’ve used numerous times with various individuals in the industrial sector – If you could give U.S. manufacturing on thing, what would it be? His response wasn’t surprising; “Better connectivity of assets. Machines that have connectivity need infrastructure to support it.”
Support that must come from both Operations and IT.