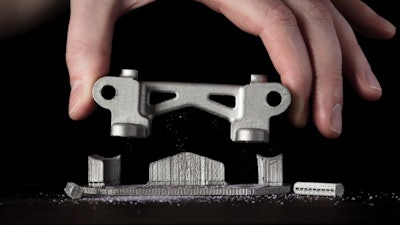
Over the past decade 3D printing has captured the imagination of the general public, engineers and environmental visionaries. It has been hailed as both a revolution in manufacturing and an opportunity for dramatic environmental improvement.
3D printing has two key attributes that lead enthusiasts to call it a βgreenβ technology. First, many 3D printing systems generate very little waste, unlike conventional manufacturing techniques such as injection molding, casting, stamping and cutting. Second, 3D printers in homes, stores and community centers can use digital designs to make products onsite, reducing the need to transport products to end users.
However, there is limited quantitative analysis of the environmental performance of 3D printing. Much of it focuses only on energy used during production, rather than including impacts from raw materials production, use of the product itself, or waste management. To fill this gap, we organized a special issue of Yale Universityβs Journal of Industrial Ecology.
We found that excitement around the possibilities for dramatic environmental improvements needs to be moderated with an understanding of the technology, how it would be implemented, and its current state of development.
Mainly for Industry
Most consumers who have seen 3D printers know them as small, boxy machines similar to ink-jet printers. Those systems can make simple products such as doorstops, bottle openers and shopping bag handles, typically from a single material.
In fact 3D printing is a family of technologies used mainly in industry, where it is called additive manufacturing. These systems produce objects, based on digital information, by adding successive layers of materials. These items are then further processed and assembled into products such as jet engine components, hearing aids, medical implants and numerous different types of complex parts for industrial equipment. Additive manufacturing thus is a complement to conventional manufacturing processes, not a substitute for them.
Industry has used additive manufacturing for several decades to create prototypes for use in product design and production planning. Now the technologies are becoming more sophisticated, and are being used to make end-use parts and products.
Additive manufacturing is especially useful for making custom parts and small batches of complex objects at less cost than conventional manufacturing, which often requires time-consuming and expensive preparation of production equipment.
Junk on Demand?
Our review of emerging research indicates that additive manufacturing is not automatically good for the environment. Parts produced this way often require additional processing to give them the correct dimensions or appearance. This can consume resources or generate further environmental impacts.
Much of the research that we reviewed suggests that seemingly mundane considerations, such as how additive manufacturing equipment is configured, the operational setup, and choices about processing details β for example, the thickness of layers being added β have a big impact on overall environmental performance. Scientists also are starting to investigate exposure to emissions of tiny plastic particles and safety hazards during use of additive manufacturing machinery.
Importantly, additive manufacturing is not an inherently wasteless process. For example, some technologies require use of temporary support structures during production to prevent objects from warping or collapsing while they are being formed. These supports cannot always be reprocessed back into raw materials. It also is important to consider whether the plastics, metals or mixed materials used in parts made with additive manufacturing can be recycled.
Another concern is that on-demand production and endless customization could lead to dramatic increases in throw-away consumer products, or βcrapjects,β as some commentators refer to them. Producing shoes, costume jewelry or household goods in varied colors or designs on demand could take βfast fashionβ to a whole new level.
Realizing Environmental Benefits
At the same time, decentralized, customized production is an intriguing environmental opportunity. It arises from a vision of producing objects in local factories, or even at home, and making just the specific product that is desired, rather than making an entire batch in a distant location, then shipping and warehousing the items in bulk quantities.
Currently, however, most products that could be made this way must be simple enough to produce on entry-level 3D printers, usually from a single material. More importantly, processing raw materials for additive manufacturing can consume more energy than manufacturing with conventional manufacturing technology and shipping the final product to end users.
Making spare parts through additive manufacturing has real potential for prolonging the lifespan of products, although it also could keep older, less energy efficient equipment in use longer. To make this a common option, some parts will need to be specifically designed to be produced through additive manufacturing.
Here, though, intellectual property issues could pose major challenges. Users of 3D printers may not have the legal right to produce parts and products from designs created by the original producers. And those producers may not find it in their economic interest to allow use of the design. Users of 3D printers may want to make spare parts for, say, an older car, but the car manufacturer may not want to share designs for those parts.
Additive manufacturing has powerful capabilities to produce objects with very complicated shapes and internal spaces β for example, specialized parts for aircraft that can reduce weight, thereby lowering fuel consumption and greenhouse gas emissions. Many researchers think the capability to make such complicated parts, and resulting gains in energy efficiency, may offer the greatest environmental benefits from additive manufacturing.
Opportunities Ahead
Additive manufacturing is very effective for producing a small number of specialized parts or products. Its potential environmental advantages currently lie in making spare parts on demand, and especially in creating specialized parts that reduce energy consumption of products during use. Other gains may be realized as technologies continue to advance.
Despite claims made about the environmental benefits of this technology, it is important to realize that these systems have not been designed with environmental efficiency in mind. While some 3D printing applications may not be environmentally desirable, there are many opportunities for improvement that have not yet been pursued. The first step is more research on the environmental impacts of producing materials used in 3D printing, how 3D products are used, and the wastes they generate.
This article was originally published on The Conversation. Read the original article here: https://theconversation.com/its-too-soon-to-call-3d-printing-a-green-technology-89212.