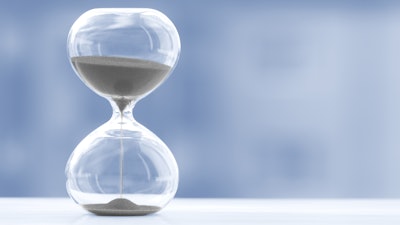
Those who work in manufacturing know that their company’s job is to ensure every job is done as efficiently and quickly as possible. However, is there a way to measure something like that? You will be happy to know that time studies on plant floors are designed to provide you with a more adequate and comprehensive overview of the allocation of your organization’s resources.
What Are Time Studies?
We can define a time study as an analysis of the company’s production process designed to enhance efficiency and productivity by identifying areas of production where time is often wasted. In other words, time study is the art of carefully observing and recording the time needed to perform each detailed element, or part of an industrial or manufacturing activity. The best thing about a time study is that it can lower waste while streamlining the production process.
Keep in mind that time studies are the most suited for activities and processes that entail a set of repetitive and predictable actions. This makes them ideal for factory settings, as it is possible to break the production process down into a series of operator movements and sequential tasks. You can use time studies to achieve various objectives and goals:
- Compare alternative methods by their basic times,
- Product cost estimates.
- For production control.
- Improve the use of machines, materials and workforce.
- Develop a better and more productive physical working environment.
- Formulate useful wage incentive schemes based on target times.
When conducted properly with adequate planning and careful analysis, time studies can deliver a granular and detailed view of how efficiently and quickly work is done on your plant floor. It is worth noting that the standard time is an invaluable metric for plant managers looking to enhance production efficiency.
You can also use a time study to establish KPIs for a manufacturing process, and assist in the collection of data in order to predict yearly revenue and output. Additionally, time studies can be used to identify hidden flaws, issues, and weaknesses in other aspects of your plant floor, such as sub-optimal layouts and placement of workstations and machines.
Tips for Success
1. Know why you are conducting a time study. Why do you want to perform a time study? Before starting, it is vital to articulate in writing the reasons and motivation for performing a time study. This will help you set goals and communicate with employees. Remember - most time studies are done merely to learn how long certain activities take, but there can be many other reasons. Perhaps, you feel overall performance is lacking and want to speed it up in new ways.
2. Use good sampling procedures. You have to follow the best practices for collecting work samples if you want representative and accurate data. Firstly, you should be aware of the sample size you will use. You can determine sample size by a formula based on the power of your sample or its ability to faithfully represent the population with a reasonable and predictable margin of error.
As you will have to allow for a specific margin of error, such as two percent, on both ends of the data, it is best to collect a sufficiently large sample size so this won’t matter too much.
3. Decide on a suitable fixed starting and ending point. Make sure that your time study is conducted during a time period that accurately represents your organization’s typical work environment. For instance, do not perform your time study while half your employees are away on vacation. You should choose a regular and representative period when everything is operating or working as usual, and your workers are performing at their standard capacity.
It is ideal to start by breaking the entire process into separate activities or steps you determine. Keep in mind that you can be as in-depth or surface-level as you want. The next step in the process is to determine the exact fixed start and endpoints of each step. When determining this, choose a period that’s representative of the overall workflow in your facility, within predictable limits. These fixed bookend points are important as they give your data reliability and clarity later on.
With technology advancement, many digital platforms and tools allow you to automatically record granular and comprehensive time studies. For example, you can easily see each operator’s time spend for each step and compare that against the benchmark or target.
It is also worth mentioning that cloud computing and IoT connections have allowed for the simple creation, maintenance, and storage of data on an unmatched scale. Computer vision, wearable sensors, and no-code apps can collect real-time data from your workers. As the data collection is now automated, it helps eliminate human bias from your sample. This connectivity is valuable as it lets engineers (or algorithms) perform real-time and ongoing studies of processes.
Time studies can be extremely powerful and valuable tools when used properly and can help you develop a solid and stable foundation for your lean organization. The first and most important step toward improving efficiency and productivity is to acquire specific data points on your performance metrics. With equipment and machines, it’s simple to predict performance. However, the humans that operate them are considerably less predictable. Time studies help fill this crucial void.
If you apply these techniques and steps correctly, you will likely end up with positive results from your time studies, especially in the long run.
Bryan Christiansen is the founder and CEO of Limble CMMS, which helps managers organize, automate and streamline their maintenance operations.