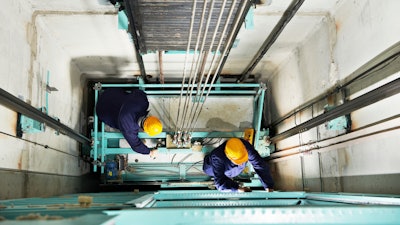
Whether it’s worn sheaves or simply an old operating system, many different factors can contribute to elevator malfunctions and breakdowns.
Taking proactive, preventative steps, however, is much easier than fixing an already broken elevator, and regular inspection is the first step to ensuring smooth and reliable operation.
In fact, thorough inspections combined with routine maintenance can significantly increase productivity by eliminating downtime, and can also decrease energy consumption by up to 15%.
No one wants long wait times or breakdowns. Not only are these obvious signs an elevator system has seen too much wear, but they can also run up costs. Below are five common elevator issues, with tips on how to fix them.
Problem: Power Failure
Since elevators require a large supply of power from commercial building utility systems, voltage updates can affect motor operations, and updates to systems can even cause damage to the elevator.
Solution: Power Quality Survey
Power quality surveys can uncover common faults like under/over voltage. Infrared thermography, for instance, measures extreme temperature fluctuations, helping to identify potential issues before they cause an expensive system failure; fuses running hot are much more easily seen using infrared technology.
Problem: Worn Sheaves
Worn sheaves place excess wear on ropes, in turn further increasing the level of wear on the sheaves. Ideally, proper inspection will prevent this from occurring, but once it does begin, damage is inevitable.
Solution: Regrooving
Either replacing or regrooving sheaves can help prevent premature hoist rope failure, so it’s important to check groove profiles in order to ensure a proper fit between sheaves and ropes. Magnetic standard tools and a straight edge can help you visually check wear on grooves.
Problem: Contamination
With wear comes the release of small metal particles into the oil, which interferes with elevator system functioning. Improper lubrication or worn-out seals can also interfere with proper functioning.
Solution: Oil and Lubrication Analysis
To ensure your elevator isn’t affected by these contaminations, a proper analysis should be completed, in which you check for certain properties in the oil that can indicate contamination or motor wear. For instance, a high level of bronze in gear case oil can mean premature wear has occurred on the gear’s crown. Or, a high level of aluminum in a hydraulic tank can mean wear has occurred on the pump housing.
Problem: Bearing Malfunction or Loud Bearings
More than 50% of all motor failures can be traced back to bearing malfunction, and vibrations within the motor can result in noisy bearings. Although variable frequency drives can help decrease the motor’s energy use, they can also introduce common mode current — a byproduct that increases vibrations to hazardous levels.
Solution: Inductive Absorbers
An inductive absorber, CoolBLUE can absorb these currents and provide protection from potential breakdowns. This absorber also ensures all grounds are connected and secure, minimizing issues from electrical noise on the ground that can trip out systems.
Problem: Misaligned Motor Drive
Shaft alignment is critical when another piece of equipment is coupled to an electric motor, as improper alignment can cause wear on motor bearings.
Solution: Laser Measuring
Shaft alignment can be detected through the use of laser measuring equipment, or simply employing a straight edge and string. The need for alignment can be eliminated altogether, however, by purchasing a geared machine with a flange-mounted motor, which doesn’t require aligning if the machine is disassembled.
Renown Electric offers preventative maintenance and on-site elevator repair services for companies and organizations across all types of industries.
For more information on preventative maintenance and tips on how to avoid elevator malfunction altogether, check out the eBook, “Preventative vs. Predictive Maintenance.”