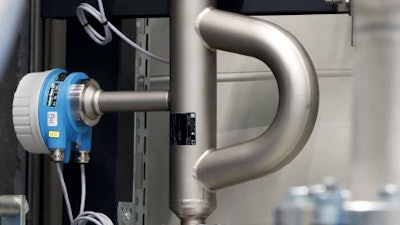
Whether dealing with food and beverage manufacturing, cosmetics and haircare or the oil leg of a separator, accurate liquid flow management and measurement can become extremely challenging when dealing with entrained gas.
Entrained gas is the result of gas and liquids coexisting, which occurs in many applications: film emulsions, glucose, cosmetics, beer, liquid fertilizers and agricultural chemicals, dairy processes, phenols, polyethylene, and food production, to name a few.
This trapped gas can be very disruptive, compromising accurate flow measurement and creating unpredictable (and less efficient) manufacturing environments.
Flow Measurement for Entrained Gas
Depending on the specific liquid process, entrained gas can take several different forms. Among the most common and difficult to manage are the bubble effect and resonator effect.
As its name implies, the bubble effect occurs when a gas bubble trapped in the measuring tube of a flowmeter does not flow with the relative motion of its surroundings.
Essentially, the liquid cannot properly hold the bubble. The density difference between the gas and surrounding liquid causes these bubbles to create a secondary flow with a different inertial effect than the one utilized by the flowmeter to sense mass flow rate; this, in turn, results in underestimated readings of the real density and mass flow rate of the liquid.
The resonator effect is also caused by bubbles, but, unlike the free-flowing gas in the bubble effect, these bubbles are suspended. The result of increased compressibility, this effect is far more difficult to eliminate, resulting in inaccurate density and mass flow measurements. This effect almost always leads to positive measurement errors.
Preventing Entrained Gas
Preventing bubbles from the outset is the best way to avoid these errors. With careful flow management process design, it’s possible to reduce or eliminate the entrainment of free gas bubbles in the overall liquid flow. Some common solutions include:
- Installing air eliminators
- Installing settling tanks for the removal of large bubbles
- Maintaining an intentionally high back pressure to a meter to avoid or suppress outgassing
- Engineering a small enough pressure loss upstream of a meter to avoid or suppress outgassing
Even so, some entrained gas often remains. Multi-Frequency Technology (MFT) effectively compensates for measurement inaccuracies and errors caused by the resonator effect by responding to the varying densities of an active flow, including entrained gas. Frequently used in heavy-duty and dairy applications, this technology has been researched and developed based on the Coriolis sensor.
The Coriolis sensor holds a unique set of vibrational properties, and, by incorporating MFT, its measurement accuracy can be significantly improved — from up to 2% error rates to 0.3% accuracy.
Learn more about MFT and flowmeter management from Endress+Hauser, particularly the Proline 300/500 family of tools. These systems help plant managers gain insight into flow processes while ensuring optimal safety and quality throughout all plant operations.