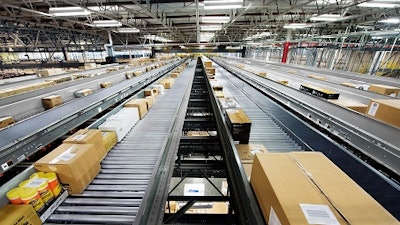
Accumulation conveyors can be critical equipment in a material handling system, providing buffer zones to hold product until downstream operations have available capacity. Advanced solutions yield high-throughput, high-density accumulation of the most challenging mix of product sizes, shapes and weights while preserving product integrity. Similar to cars slowing down for traffic lights, accumulation conveyors allow items to queue before moving forward. Operating a material handling system without any accumulation functionality, such as belt conveyors running at a constant speed, is analogous to driving a car in traffic without any brakes. It eventually slows down, but at the expense of another car’s bumper.
Medium-pressure, zero-pressure and zero contact are three types of accumulation conveyor that regulate product flow through automated systems, allowing operations to run more smoothly and accommodate fluctuations in product movement.
Medium-Pressure Accumulation Conveyor
Medium-pressure accumulation conveyors typically utilize a flat drive belt to apply adjustable pressure to conveyor rollers without logical control of the accumulation function. Even as product starts to accumulate, the drive continues to run and apply slight pressure to the rollers, resulting in back pressure on accumulated products. Using this technology requires balancing sufficient drive pressure to move the heaviest product, while not exerting excessive pressure that risks interrupting smooth product flow. This technology is also referred to as low- or minimum-pressure accumulation.
Medium-pressure accumulation conveyors are typically most effective when handling the same or similar-size products capable of withstanding slight back pressure without sustaining damage. In applications with different-size products, the back pressure may cause wider products to pivot around smaller items during accumulation, resulting in side-by-sides and downstream operational problems. Back pressure can also cause product damage due to insufficient protection from fragile packaging.
Therefore, an appropriate application of medium-pressure accumulation conveyors may be in an environment that rarely requires accumulation, such as occasional, minor delays in downstream operations.
Zero-Pressure Accumulation Conveyor
Zero-pressure accumulation conveyors consist of rollers divided into zones that drop in sequence as products accumulate. The system uses a flat, narrow belt or padded chain as the drive mechanism, raised or lowered by pneumatic actuators to apply drive pressure to rollers and move product. Before a product runs into an accumulated item downstream, the pneumatic actuators release air to lower the drive mechanism and remove pressure on rollers to allow the item to coast to a stop.
The ideal zero-pressure accumulation conveyor lets off the drive pressure to the rollers early enough to prevent any side-by-sides, jams or product damage, but late enough to remove all air gaps from a line of accumulated items. In a zero-pressure accumulation conveyor system, items coast to a stop and contact the next downstream item. After accumulation, there should be no driving pressure on accumulated items, hence the term “zero-pressure” accumulation.
Zero-pressure accumulation conveyors often operate in distribution and fulfillment facilities where the product mix consists of a wide range of sizes and weights. This variable product mix means that any back pressure during accumulation could cause sideby–sides, which may lead to downstream operational problems. Within these operations, zero-pressure accumulation conveyors are often positioned before and after sortation systems, feeding merges and also leading to shipping docks.
Zero Contact Accumulation Conveyor
Zero contact accumulation provides the best carton control and lowest risk of product damage by instantly stopping accumulation zones to prevent items from coasting to a stop and contacting each other. This type of accumulation typically utilizes one or two motor driven rollers (MDR) connected via o-bands to other non-powered rollers to control each accumulation zone.
MDR conveyors use “run-on-demand” technology that provides significant energy savings, only operating when necessary to move product to the next zone. Other benefits include low operating noise and no back pressure on the accumulated product. However, this approach does offer a lower throughput rate compared to medium-pressure and zero-pressure accumulation.
Zero contact accumulation is most similar to how people typically drive. Imagine a road divided into segregated zones slightly larger than the average car length. Cars only move forward when the zone in front of them is open and come to a stop before they reach the end of their zone, ensuring no contact between cars.
Recent changes in dimensional weight pricing have caused operations to increase their use of polybags in an effort to keep shipping costs low. Accumulating with polybags presents unique challenges best handled with zero contact accumulation, making MDR the conveyor technology of choice for applications with flexible packaging.
Conclusion
With several conveyor technologies capable of accumulating product in material handling systems, selecting the right approach requires careful consideration of key tradeoffs. Understanding the product mix and throughput rate requirements helps select the technology best suited to meet operational goals.
Tim Kraus is manager of product management, and Jonathan Lim is a product manager – both for Intelligrated. For more information, visit www.intelligrated.com.