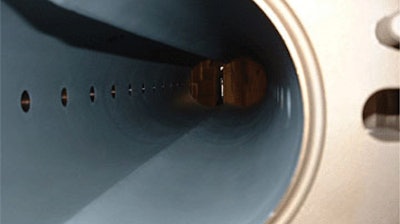
By Corey Wesnitzer, General Magnaplate Corp.
Rather than being a part of the discussion in the early stages of design, designers try to solve problems with coatings at the point of manufacturing – or even after manufacturing.
While each type of surface treatment (anodizing, electroplating, thermal spray etc.) provides its own unique set of properties and benefits, each of these processes also has limitations that should be addressed early on in the design process to ensure optimal performance.
Typically, engineers are looking to extend the life of equipment by protecting parts from wear, abrasion. Protective coatings not only guard these parts against these issues, they can also provide lubrication and increase structural integrity. Using the correct surface treatment on equipment can increase a part’s lifespan, eliminate the need for production downtime, and reduce overhead too.
Key factors affecting surface treatment that need to be discussed at the outset of the design process are:
- Process limitations
- Choice of base metal
- Part configuration and design
- Surface finish
Engineers risk lengthening product cycle times by not making surface treatment discussions a primary consideration early in the design process because they risk specifying a treatment that cannot be completed due to the design properties of the part in question.
Process Limitations
‘Line–of–sight’ is one of the most frequent process limitations that engineers encounter and is most commonly experienced with electroplating, anodizing, spray coatings and physical vapor deposition (PVD) methods. Essentially the rule with these processes is ‘what you see is what you can coat’ so engineers needs to consider a more suitable immersion process for parts with ‘hidden’ surfaces that require treatment.
With ‘line-of-sight’ applications the engineer is usually limited to 1 – 1 1/2 times the diameter for the depth of the coating to uniformly penetrate down the hole because of the limited ‘throw’ of a line-of-sight process. This means that parts with deeper holes will not have a uniform coating thickness, which may be a significant issue for parts with tight tolerances.
Air pockets or ‘pocketing’ is an issue more commonly found with immersion processes such as anodizing and plating. If a critical surface needs to be coated, the engineer needs to ensure that there is access to that surface so that pockets can be removed by the coating vendor. Pocketing also reduces the efficiency of the coating process because the part often has to be orientated (in the case of immersion processes) at different angles and then maneuvered to remove the air. Intricately designed parts are more susceptible to this issue and engineers also need to consider designing in relief holes to allow the air to escape.
Base Metal Choices
Communicating early with your coating vendor on the choice of base metal for the part can also eliminate issues later in the design process, especially if the part has tight tolerances, because subsequent processing temperatures can have a damaging affect.
Deformation can occur if application surface loads are high and process or post – process temperatures, during the coating process, exceed the substrate’s heat treatment recommended operating temperatures. In addition to deformation, some metals suffer from structural stability issues where the part will move or actually change size.
When high strength alloys or materials such as titanium or tool steels are considered, part designers need to be aware of hydrogen embrittlement, which can cause the part to crack and fail under loads. During the cleaning process, which often involves acidic materials, certain alloys will impart hydrogen to the surface of the metal, which causes the embrittlement. If the coating vendor is aware of this, he can perform processes to the part after coating or use alternative cleaning processes to expel the hydrogen from the surface and avoid the issue.
Sometimes engineers design a part that incorporates more than one material. In this case, the part may not be conducive to plating surface treatments because the cleaning process before coating are different for each type of metal. One cleaning process may activate the surface of a specific metal for coating, while passivating the surface of the second material. If both surfaces cannot be coated at the same time, special masking is required and the labor–intensive nature of this work drives the cost up.
Adhesion issues on the boundary areas between the two metals also occur, and when you expose them to electrolytes there may be a galvanic reaction between the two materials creating corrosion of one of the base materials.
Additionally, if the base metal of the part is extremely hard it can cause surface tensions that prevent a strong adhesion between the base material and coating. A bad bond between the part and coating will lead to chipping of the coating.
Part Configuration
In many plating processes, a sharp corner is the designer’s greatest enemy. Sharp corners are subject to chipping; therefore it is always advisable to radius the parts, depending upon the coating thickness required. A greater radius provides more support for the coating and minimizes chipping, but if a sharp corner is absolutely necessary then the coating thickness should be kept to a minimum.
Some processes which require electrical current to generate the coating produce an unwanted effect on sharp edges and corners of parts, which translates to greater coating thickness in those areas and less in other areas. If the part has tight tolerances, subsequent machining operations will be required, which increase both costs and time.
Designing parts with sufficient corner and edge breaks helps avoids this issue. If a part has thin areas of metal then these spots can be prone to burning. When high voltages are required during some coating processes, thin sections of metal generate high amperages, which can cause those areas to burn. Your metal finishing expert will have to adjust his processes to minimize this potential.
Size also matters when coatings are a consideration. Immersion coating processes are limited by the tank size, so designers need to communicate with the vendor to see what size parts they can physically accommodate. In the case of very heavy parts, material handling capabilities also need to be discussed.
Coating Considerations
Because parts need to be racked in order to be coated, it is important to discuss racking early in the design process with your coating vendor. Racking means that areas of the part may be left uncoated where they come in contact with the rack, or the part may end up marked by the racking process. If the part is large then it cannot be suspended by a small hole, so significant rack points need to be considered. In certain processes, particularly anodizing and electroplating, the racks act as a current carrying device so correct positioning of the racks is critical, as is the number of rack points required to achieve a uniform coating.
Some applications require areas of the part to be free from coating. This leads back to the labor-intensive issue of masking – engineers should not underestimate how much this process adds to the processing cost. If cost is an issue, then it is best to design a part that can be coated all over.
Tight Part Tolerances
Each coating process (i.e. anodizing, plating, thermal spray etc.) has specific thickness and tolerances to which the coating can be applied. Depending on the process selected, parts may or may not require machining after the coating is applied. Engineers should pre-size parts to accommodate coating thickness and tolerances wherever possible.
Coating thickness should be a primary consideration for engineers, especially where tight tolerances are required. Certain processes, such as plating, are described in terms of surface growth. For example, 0.001mm of a coating will be equal to 0.001mm of surface growth. Other methods, such as anodic processes, are described in terms of a combination of penetration and surface growth, where 0.001mm of a coating may only be equal to 0.0005mm of surface growth because the coating penetrates the metal’s surface.
Threads often have tight tolerances, especially on the pitch diameter where the two parts engage each other. On a 60° thread form every unit of coating thickness applied to the surface will affect the pitch diameter by four times that amount. If threads have to be coated, they should be pre-sized to accommodate the coating thickness requirement to ensure proper engagement.
Surface Finish
Some coating processes will replicate the surface finish, but only down to a certain degree – measured in units of Ra. For instance, plating a surface can replicate as low as 16 to 32 Ra finish. For lower Ra values (i.e. better finish) post grinding or polishing may be required.
With so many considerations, it is critical for the engineer to make sure they communicate with the coating vendor to ensure an efficient design and manufacturing process. Not only can this produce a faster product cycle time, it can also reduce costs and ensure better part performance in the field.