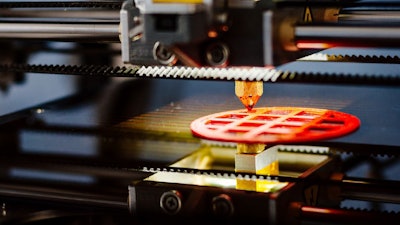
Linear motion components play a critical part in the successful operation of a 3D printer. They must precisely guide the movement of the unit's print head, nozzle, laser, or electron beam — and sometimes also its material bed. That's true for every relevant additive manufacturing technology, including stereolithography and sintering, direct metal laser sintering, direct metal laser melting, and electron beam melting.
Early 3D printers did not demand the utmost in precision and today many desktop models still regulate linear movements using the same mechanisms that 3D printing pioneers employed, such as bushings and belt drives, or steel rods and basic ball bearings. This arrangement is inexpensive, and provides adequate control for many simpler printing tasks.
However, today, designers of even some smaller printers are turning instead to more advanced linear motion solutions, such as profiled linear guideways with ball bearings or rollers.
These cost more than belt and rod systems — averaging 3x more expensive. But their advantages for many printing applications are decisive.
Their much higher degree of stiffness enables printing that virtually eliminates frustrating printer problems such as ringing or backlash. And they help avoid other issues of rod and belt arrangements, which are often too tight (so movement suffers from roughness or binding) or too loose (so movement is affected by excessive play in the mechanism). Instead, a linear guideway's high-precision machined tolerances ensure ultra-smooth motion.
Beyond the desktop level, or beyond printers used simply to create one-of-a-kind prototypes, modern 3D printers are often dedicated to complex industrial uses. They typically turn out parts — often at high production volumes, and always with great consistency — for machine tool, aerospace, automotive, and biomedical uses, and more.
When a printer is dedicated to these applications, make sure it implements a whole new level of linear motion performance. Demand a linear motion solution with much higher degrees of critical characteristics such as rigidity, speed, and precision.
Modern motion components often applied to industrial printers include profiled guideways with balls, profiled miniature guideways, miniature balls screws, and linear motion systems.
Integration is a continuing trend. Why buy a rail or a slide plus a separate encoder, and then encounter difficulties in trying to align them? Specifying the guideway with an integrated encoder/measuring system can save setup time and trouble while reducing total cost of ownership.
Also, buy with an eye on simplifying maintenance. Look for options such as integrated long-term lubrication features, or materials with extended wear resistance.
Ask the linear motion experts
Many 3D printer OEMs have limited resources. Partnering with an experienced linear motion supplier can in effect extend your engineering team. Working closely with the supplier helps to build the best relationship for a successful project:
1. Start early. Call in the supplier near the start of your process, arrange a nondisclosure agreement (NDA), and get your linear motion requirements quantified and understood as quickly as possible. That gives the supplier maximum time and scope to come up with just the right solution, from initial planning to final design freeze.
2. Design to performance. Ask the supplier to quickly pinpoint any motion issues and opportunities that a given printer design may present. They can identify trade-offs and suggest alternatives. The goal: help you avoid any pitfalls now — to prevent performance shortcomings later, when they're harder to correct.
3. Design to cost. Budgets are always a prime concern. Give your supplier your intended market price or target. The right supplier will strive to meet it, without sacrificing quality or long service life. The ultimate goal is to strike the best balance: optimal performance with the lowest total cost of ownership over the lifetime of your printer.
4. Explore custom options. Some standard, off-the-shelf components won't fit, or can't deliver the right performance for your specific design. Keep your options open. Avoid "take-it-or-leave it" ultimatums; find a partner to tailor solutions to your unique specifications. Customized linear motion components and systems can improve the design process, the performance, and the total cost of ownership of your 3D printer.
Besides expertise with customization, find a supplier with a wide array of linear motion offerings to draw on a range of products such as anti-friction guideways, profile linear guideways, bearings and racks, positioning systems, linear ball bearings, and ball screws. Components like these can be intelligently combined in a system with the rigidity, speed, and precision to deliver the performance you demand.
Rigidity
The performance of a 3D printer's linear motion system rests, literally and figuratively, on its base.
Where high performance is called for, sufficient rigidity or stiffness demands close attention to factors such as thickness, frame construction, and materials. All must be consistent with the final performance specifications.
Rigidity affects factors such as flatness and straightness. For example, printer makers may attempt to attach a linear motion rail made of stainless steel, of required thickness and suitably rigid design, to an aluminum plate that's actually thinner than the rail. The inevitable result: deflection.
(Linear motion components are typically designed to resist forces along the x, y, and z axes to prevent this.) Here deflection would mean that the rail could curve, however slightly, in the direction dictated by any force applied. This affects smooth travel and repeatability, which in turn can degrade the uniformity of the printed product.
Even the finest linear motion products can't deliver superior speed or precision if they rest on a base that allows any extraneous movement. Traditionally, most 3D printers have been mounted on structures such as sheet metal cabinets or aluminum tables. These won't deliver acceptable rigidity for most of today's industrial additive manufacturing equipment. Instead, research strongly built steel or iron structures or granite bases.
Another innovative choice: a substructure composed of minerals and epoxy resins. These mineral cast bases furnish printer beds with superlative vibration dampening, strong chemical resistance, and excellent thermal stability. They can be formed to accommodate any contours and dimensions a given printer requires, including custom-shaped openings, spaces, and wiring channels. They also offer clear technological, economic, and ecological advantages over steel, gray iron, or cast iron.
Discuss expected loads and printer configuration with the linear motion supplier early so that the system can withstand all the specific operation forces and conditions.
Speed
The travel speed of the linear motion system essentially defines the printer's speed of production.
Of course, for some printers' tasks, relatively slow speeds are necessary to prevent problems such as deformation. On others, excessive travel acceleration can create issues from ringing to ghosting to lack of layer adhesion to filament blobbing. In most cases, additive manufacturers seek to maximize speed wherever possible.
It's essential for some applications that a linear motion element accelerate as rapidly as possible for the highest productivity. But settle time is often another key metric: how long it takes the rail or other component attached to the moving part (print or beam head, material bed, etc.) to come to rest without appreciable vibration after each acceleration step.
Of course, these factors are greatly dependent upon the printer's design; the material, shape, thickness, resolution, and other characteristics of the specific piece the printer is making; and which linear motion components are chosen.
Generally speaking, in an optimum configuration, some of today's high-performance linear motion systems can attain constant velocities with step-and-settle intervals — even at highly precise positions — of as low as 50 milliseconds. That would allow extremely rapid travel to support the fastest industrial printers available today, which operate at up to 1000 millimeters a second.
Precision
When choosing linear motion equipment, consider the degree of positional accuracy and repeatability — the precision — that the 3D printer/additive manufacturing design demands. This will impact several critical areas of final performance, including accuracy, repeatability, and resolution.
If the work process includes after-print finishing steps to attain given tolerances or flatness/smoothness specifications, extreme precision in primary printing may not be necessary. A good linear motion system for this range of printers might deliver positional precision down to plus or minus 50 or 100 microns.
However, internal features of the workpiece may not be easily accessible after completion. Additionally, OEMs at the forefront of the industry are evolving their approaches to minimize extra finishing. Some cases may require extremely accurate linear motion to achieve precise dimensions and shapes at every point.
Many 3D printing applications are moving to the level of linear motion equipment precision traditionally required by high-performance machine tools. Now, if you're used to building a printer to achieve only 100-micron exactness, you may not be sure how to improve that significantly. And as additive manufacturing technologies evolve, some applications demand even higher degrees of precision — like those that leading linear motion suppliers design into ultra-precise nanoscale equipment for semiconductor manufacturing.
Much depends on the specific printer design and on the piece that must be printed. Beyond that, address issues such as linear motion system's stiffness, flatness, load/preload, and materials of construction to its operating temperatures and vibration/resonance potential and considering factors such as constant velocity and stroke length. But under the right conditions, a superior linear motion system today can enable certain 3D printers to attain repeatable accuracy from 0.5 down to 0.1 microns.
Moving into the future of additive manufacturing
Today's advanced linear motion systems can actually deliver more precision than existing 3D printing technologies can use.
As additive manufacturing continues its explosive development, speeds will increase, efficiencies will grow, and materials will proliferate. Certainly, the tipping point is near when more 3D printers will produce metals than plastics.
So there's ample room for printers' linear motion capabilities to grow. For instance, the ability to precisely control the movement of dispensing elements on smaller and smaller scales can empower bioprinters to manufacture ever-finer somatic structures. Vein tissue was first successfully printed in 2016. Fully functional 3D-printed human organs are predicted in the not-so-distant future.
Or on an industrial scale, high-precision linear motion equipment could help enable 3D printers to produce surfaces characterized by extreme smoothness. This would permit the production of pieces flat enough to function in bearings, seals, or other parts that demand closely mating surfaces — without requiring additional finish machining.
Conclusion
An increasing number of 3D printing/additive manufacturing OEMs are exploring the benefits of advanced linear motion solutions for their unique products. The right supplier can overcome concerns and obstacles to help deliver advantages such as expert design, acceptable lead times, reduced cost of ownership, reliable quality, and rewarding partnership. And the right products can provide critical characteristics such as the rigidity, speed, and precision that enable truly high-performance printing.
Ross Blumenthal is vice president for sales and marketing with Schneeberger Corp.