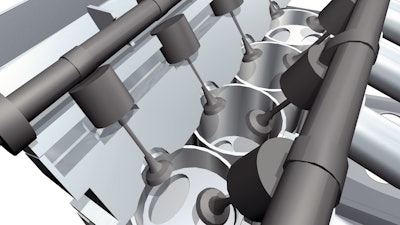
Seeking to go beyond the limits is a defining characteristic of manufacturers of super cars, motor bikes and of professional racing teams in motorsports because of the hyper competitive markets in which they compete worldwide. To achieve their mission on both the road and track requires continually pushing the operating performance limits of all their component parts as well.
One of the most demanding environments in high performance vehicles are the high friction, wear and contact areas of the engine and valve train such as the camshaft, piston pins, valves, lifters and finger followers, where there is high contact pressure and sliding speeds. Coatings play a pivotal role by reducing friction and adding hardness to reduce wear. By doing so, performance is enhanced, and the usable life of key components is increased.
However, utilizing coatings to increase performance and life of key components is complex, as coatings must work within a tribological environment of friction, lubrication and wear. In addition to delivering a hard, smooth surface, coatings must have excellent adhesion to metal substrates.
Limitations of Current Coating Technologies
To date, the performance standard for coatings in this environment has been Diamond-Like Carbon (DLC) coatings which have been the coatings of choice for OEMs and professional motorsports over the past 25 years. These coatings are produced through plasma assisted chemical vapor deposition (PACVD) which produces extremely hard, yet thin, coatings which provide high adhesion to substrates while providing hardness and reducing friction. Within this coating family, the majority of coatings are made of amorphous carbon with hydrogen (a-C:H).
“Although today’s a-C:H coatings can be produced at high volume for low prices, in terms of their design properties they are already reaching their performance limits,” according to Marc Hervé, Segment Manager Motorsports for international coatings manufacturer, Oerlikon Balzers. “When a customer seeks higher performance than an a-C:H coating can deliver, the only option to date has been a more expensive and time-consuming hydrogen-free DLC.”
Hydrogen-free coatings, which represent only a small percentage of the DLC category, are made using a physical vapor deposition (PVD) by arc method which produces tetrahedral amorphous carbon or ta-C. Although this can be used to create a very dense, hard coating with high adhesion, the process produces small droplets that contribute to a rough surface finish.
As a result, coating manufacturers must complete secondary polishing processes to smoothen the surface. Because of its hardness, it is a time-consuming and expensive process.
“Hydrogen-Free DLC coatings are extremely hard and adhere well, but the process can leave a rough surface finish that requires secondary polishing,” explains Hervé. It can be expensive, because the coating is so hard it takes time and specialized equipment.”
Creating a New Performance Standard
Fortunately, recent advancements in the development of harder, yet smoother DLC coatings are being driven by refinements in the application process, says Hervé.
In a proprietary process developed by Oerlikon Balzers, the DLC coating can be applied utilizing Scalable Pulsed Power Plasma (S3p), which combines the advantages of the arc evaporation and sputtering methods. Arc evaporation is known for producing dense coatings with high adhesion. Sputtering, a conventional coating technology where atoms are ejected from a target or source material to be deposited on a substrate, is known for high levels of smoothness.
The result is a hydrogen-free DLC coating that delivers a unique combination of high hardness, low friction and a smooth surface. The S3p technology generates a high level of “diamond” (tetrahedral) bonds with hardness up to 40 GPa (indentation hardness, HIT). In comparison, typical DLC coatings achieve hardness levels in the range of 20-30 GPa and only 10-15 for WC/C coatings.
As such, the coating – called BALIQ CARBOS – provides the hardest surface coating within the category and up to double the hardness of current DLC coatings. The coatings exhibit three times lower abrasive wear than a 20 GPa hard DLC coating as measured by a calo test (ball cratering with abrasive slurry).
Unique to the extra-hard BALIQ CARBOS coating is that it both delivers the low friction of carbon coatings with the smoothness typical for coatings applied in the sputter process with the same low roughness of Ra = 0.03 µm as other sputter- or PACVD coatings. Moreover, the smoothness is achieved without additional polishing treatments saving time and cost. In most cases, the component is ready to use immediately after coating.
The coating process operates at a relatively low temperature, below 200 degrees Celsius as compared to up to 350 degrees for other DLC coatings, which enables its application to a much wider panel of materials, effectively bonding to aluminum and steel substrates. This opens up more options for coating applications and the higher hardness directly translates to longer component service life.
Together the advancements in hardness, smoothness and temperature of even harder DLC coatings promise to provide OEMs and professional motorsports teams with an opportunity to extract more speed and increase the durability of their precision engine components as they pursue their high-performance goals in the fast lane.
For more information on BALIQ CARBOS, visit the Oerlikon Balzers’ website at: www.oerlikon.com/balzers/baliqcarbos.