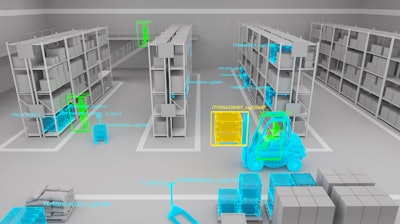
In this exclusive interview with Joey Mulqueen and Eric Halvorson, industrial automation experts at Digi-Key Electronics, a distributor of industrial automation and controls, we discuss how machine vision is making manufacturers more productive; features that should be top priority; and emerging technologies that will be commonplace in the next five years.
IEN: How is machine vision being used to make manufacturers more productive?
Digi-Key Electronics: Manufacturers rely upon vision systems to monitor quality within their plant. They can check quality on each unit as it passes through the manufacturing process. Through pattern recognition, the system can track multiple defects and alert operators to issues within the manufacturing process, such as faulty tooling. They can also allow the system to adjust ordering systems to account for bad/defective product. Machine vision is also a valuable input in machine learning as pattern recognition will enable on-the-fly programming adjustments to the manufacturing process.
IEN: How has machine vision improved to help prevent false positives in quality inspection?
Digi-Key: Quality inspections have historically been conducted by humans. In most cases, this works well, however, there are obvious shortcomings. Human fatigue and insufficient training can lead to errors. The machine can run non-stop without breaks.
Another downside is precision. Machine vision can eliminate much of that. Today’s vision systems are far more precise than the human eye. It can detect exact dimensions, colors, markings and labels. It also possesses the ability to track each single part it inspects. Should there be an issue with a specific product, manufacturers can recall data from the system using date/lot or serial numbers to determine if there was error in the manufacturing process. This is extremely useful in the performance of a failure analysis. It can help determine if the product failure was due to it being out of specification, or if it was customer error.
IEN: When it comes to designing (or retrofitting) equipment, what features should be at the top of the list when it comes to machine vision?
Digi-Key: Designs and retrofits of equipment for machine vision will depend entirely upon the application. Quality control specifically measuring dimensions and color will require high resolution cameras. Label verification would require appropriate lighting as reflections could be an issue. Processing power comes into play when applications run at higher speeds. If your application is outputting high volumes of product, you will want the extra processing power and speed. Adjusting on-the-fly requires communication. The camera will need to interface with the robot and machine to make the adjustments quickly and accurately.
IEN: Have you noticed an uptick in interest for machine vision and other automation technologies since the onset of the COVID-19 pandemic?
Digi-Key: The first wave of COVID-19 has created a slowdown in much of manufacturing. We see this as only temporary. As manufacturing returns, we believe there will be a boom in production. As we begin to return to work while maintaining social distancing as the new norm, there will be an increased need for vision systems and automation systems to help fill the void with more workers unable to occupy the same workspace or unable to come in.
IEN: What emerging technologies should we expect to become commonplace in machine vision applications in the next five years?
Digi-Key: Artificial intelligence (AI) and machine learning are already making huge advancements in the field of machine vision. The machine’s ability to quickly and accurately make decisions through visual inputs is paramount. 3D imaging allows a more complete visual of a product, enabling better quality tracking for manufacturers. The technology itself won’t, most likely, change in the next 5 years, however access to the information produced by the cameras on the manufacturing line will become more readily available to consumers. A future option may be an x-ray inspection system of integrated circuits on the line at the time of manufacture for recall reference during potential failure analysis investigation.