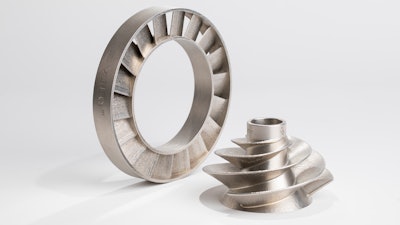
Velo3D recently unveiled their 3D Metal Printing platform, which they feel could take the application of 3D printing from prototyping to full manufacturing. Their goals include enabling manufacturers to design and print more complex geometries that allow engineers to create and manufacture a wider range of new products. The company has raised over $90 million in venture funding, and recently sat down to discuss its offerings and thoughts on the future of 3D printing.
Jeff Reinke, IEN Editorial Director: It’s unique for a 3D printing company to describe their product as “designed for high-volume production.” Could you qualify that a bit in terms of comparison to other high-volume parts production methods?
Stefan Zschiegner, Velo3D’s Chief Product Officer: Designed for high -volume production means that we optimized the system design on spending every minute on manufacturing good parts. There are many innovations that went into the Velo3D Sapphire system to enable that, including automated changeover without human intervention in 15 minutes. We have hermetically sealed build modules that can be automatically staged, docked, setup and started for printing without any human intervention.
After completion of the build, this build module is automatically moved to the ready-to-unpack position and another module can be moved from the ready-to-print position and the print can start automatically in 15 minutes. Other innovations include the ability to extend calibration cycles, the ability to automatically validate that the system is in spec, to hot swapping of filters, and much more.
JR: The Intelligent Fusion platform seems to be what really makes the system unique. How is it different from other additive manufacturing technologies
SZ: Intelligent Fusion technology takes conventional powder bed fusion to another level. It includes the methodology of simulating the thermal meltpool, to predicting and correcting stress and deformation during the print preparation, and then during the execution stage, leveraging in-situ metrology for controlling the melt-pool in real-time to ensure the part is built the correct way every time.
JR: With recent developments in 3D printing carbon fiber and extremely durable polymers, what led Velo down the path of 3D printing with metal?
SZ: The Velo3D vision is to take additive manufacturing mainstream for use in volume production, enabling customers to not only prototype, but to develop and produce in volume with AM technology overcoming the inherent constraints of current solutions (i.e., the ability to print complex geometries without supports) and opening up metal AM for any design.
JR: Are there any industries you’re specifically targeting with this latest release?
SZ: Currently, we are working with customers in aerospace, energy and industrial, and medical implants and tools. However, we also see opportunities in automotive over time.
JR: What do you feel are the leading factors taking 3D printing from prototyping applications to wider-spread adoption of production applications?
SZ: There are multiple factors that are holding the industry back. One of them is capability: there are too many design constraints that are holding AM back. Customers need to change the design for AM and make a commitment for AM in production very early.
The second barrier is the workflow necessary to prepare for 3D printing; it is complex and convoluted and results in mistakes and protracted iterations.
The third issue is cost. While the printing step has become more effective, there is a lot of wasted costs in developing the supports, post processing and the removal of supports.
And finally, there is quality as a key barrier of adoption. Current AM systems are unable to guarantee control quality, which results in too much variation of the produced part. The Velo3D Sapphire system and Flow software solution are specifically designed to overcome these challenges so customers can have confidence and use AM for volume production applications.
JR: How does the ROI compare with a metal 3D printer to one more focused on plastics and polymers?
SZ: In many cases the ROI considerations for metal are very different. The reason is that metal 3D printing shifts away from prototyping to development and production utilizing the same additive manufacturing process. This is different than plastics and polymers, where the majority of applications are limited to prototyping, meaning the production still relies on conventional methods. Since for metal the goal is to use additive manufacturing also in production, the ROI depends on the customer development cycle for a given part, and will be realized over many years to come.
JR: What do you think will be the most important developments in 3D printing in the next 18 months? 5 years?
SZ: There are many exciting developments ahead for additive manufacturing that will push it towards the mainstream. As we are overcoming the barriers mentioned above, customers will have the freedom to print any design with a predictable and controllable quality in manufacturing. It will become the new normal and it will accelerate not only for new designs to be optimized and take advantage of broader design capabilities, but will also be applied to tooling, spare parts for legacy products as well as many other new applications and novel use cases that we have not even yet considered.