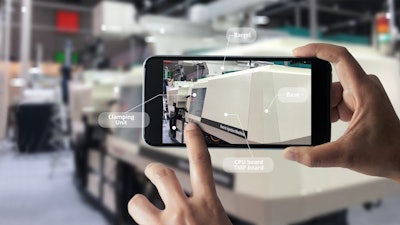
Manufacturers have a lot of confusion over what the Industrial Internet of Things (IIot) can mean for them. I’ll try to make it simple.
Generically, IIoT means the use of sensors to gather actionable data. It doesn’t have to involve the internet; it can reside simply within a building. As an example, temperature and vibration sensors might measure the performance of a machine bearing and when both trend up, you know the bearing is failing and it’s time to change it. The data allows you to change the bearing at a convenient time rather than waiting for it to blow in the middle of a production run. Good use of IIoT allows for more production, better quality, easier training, and less waste, maintenance, and process variation.
IIoT is also used to turn “products into a service.” For example, a washing machine could have sensors installed to give data back to the manufacturer on product performance, tell the owner when to clean the filter, or suggest the best time to schedule a wash for lowest electricity cost. If the consumer pays for this service, the OEM now has a recurring stream of revenue.
Manufacturers can also do the same thing in products they sell to other businesses. GE is doing it now with locomotives and there are dozens of other examples.
The basic structure starts with simple sensors which measure temperature, vibration, sound, pressure, etc., and transmit that information to a database in the cloud. People can then query that database to learn more about their business. For example, how does this machine’s performance compare to another one? Or, why is compressor #2 only putting out 75 psi?
You can then add machine learning (AI), which will perform its own queries and find interesting relationships between the data that you might not have thought of – Compressor #2 underperforms when machines #2, #10, and #25 are all on at the same time, for example, or machine #8 produces worse quality when using material supplied by Company X.
In addition, you can employ “digital twins”, which are numerical representations of an individual machine, to help predict performance or maintenance. Almost half of preventive maintenance is a waste, but everyone does it because it’s more convenient to shut a machine down and make sure it’s working properly than to be surprised in the middle of a run.
AI and digital twins can help predict exactly when (and what) maintenance is required, so you can still schedule it, but do only what is really needed. Why grease a fitting that already has plenty of grease?
IIoT can also be used to gather data for augmented reality, where, for example, trainees can use Hololens glasses which overlay directions on how to operate a machine, or how to wire an airplane.
The major companies which provide these services—Microsoft Azure, AWS (Amazon), PTC, etc.—have made these “stacks” of services interoperable. Which means you don’t have to worry about connecting them all – it’s already done. And you don’t need a 5G connection—4G is plenty.
The most important component of putting this together is to start with the end in mind.
- What do you want to accomplish?
- What do you need to learn about your business?
- What functions are you trying to automate?
- What parts of the business are underperforming?
Start small and cheap—just one machine, one cell of machines, or one department. Then expand.
Before you get started, you need to know:
- Sensors are often the weak link in cybersecurity, make sure they’re behind the firewall.
- Know who owns the data. If it’s all happening within your factory, then you own the data, but if you’re using or providing data to/with suppliers or customers, then you’ll need to discuss this issue up front.
- If you’re in the design stage of a new product, make sure IIoT, particularly the sensors, is designed in from the beginning — it’s harder to add it later.
As you start implementing IIoT, remember that much of this data is actionable on the part of frontline supervisors and machine operators. Make sure these employees have access to it, and training — this will allow you to delegate further and concentrate on even more important parts of your business.
---
Josh Chernin is a partner with Business Improvement Group, LLC, and has more than 30 years of manufacturing and operations leadership experience in the United States and Europe.
Chernin has had P&L responsibilities in printing, metals, converting, contract manufacturing, and textiles, built three plants, consulted to many manufacturers, performed several turnarounds, and visited more than 300 manufacturing plants.
He also has deep experience in medical devices and aerospace and is an expert project manager. He can be reached at www.bizimprovementgroup.com.