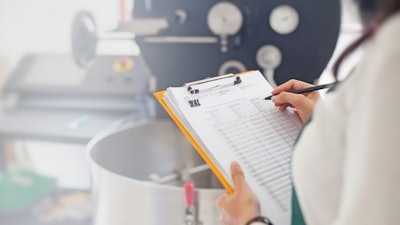
Consumers rely on manufacturers to produce items that are safe, uniform, and do work correctly. While quality assurance takes time and is viewed by some as a bottleneck, without QA, facilities will find themselves with a lot bigger problems.
Quality assurance is about so much more than just monitoring a line and rejecting bad samples. In a way, quality coordinators are an advocate for customers on the manufacturing floor. When quality assurance is done correctly, it helps producers not only make better products, but win the trust of their client base, setting themselves apart from the competition and growing their business over time.
On the flip side, companies who pass over quality assurance, or even take shortcuts, wind up badly damaging their reputation, paying millions of dollars in fines, lawsuits or recalls, and losing future profits. Let’s look at three examples of quality assurance failures in the last couple of years, and see what lessons we can learn about how to take quality control seriously.
Avanos Medical, July 2021
Avanos Medical, Inc. is a global medical supplies company based in the U.S. From 2013-2015, they manufactured medical gowns claiming to meet the highest level of protection from virus penetration.
In reality, Avanos had a quality problem on their line that meant the gowns were failing viral-penetration tests. The company knew about the issue and was working on making internal changes, but continued to sell the gowns branded as meeting those standards.
It is not enough to have internal quality checks if nothing is done with that information. Avanos should have considered the end user - frontline healthcare workers dealing with highly contagious diseases and the vulnerable patients they treat. Sending out an inferior product was unethical and dangerous.
In the end, Avanos wound up paying more than $22 million to resolve the issue. Putting profits over safety resulted in neither. Pulling the gowns from the market or rebranding them to properly reflect their level of protection would have been not only a more responsible solution, but a better business plan.
Johnson & Johnson, July 2021
The summer of 2021 had many consumers panicking when Johnson & Johnson recalled a series of aerosol sunscreen products found to contain benzine, a known carcinogenic.
In this case, the recall was voluntary, giving Johnson & Johnson a leg up in the public relations battle. However, because of the quality slip, the sunscreens in question were immediately branded in the news media as causing leukemia. The products were maligned by social media influencers and Johnson & Johnson settled several lawsuits, but not before one of its major distributors, Costco, was also dragged into the legal fray.
Getting ahead of the problem through the proper recall channels was the right decision, but imagine an alternative outcome where Johnson & Johnson and their manufacturing partners had more rigorous quality assurance procedures in place. The company could have been spared millions of dollars in lost profits, and end users could have been spared so much anxiety, not to mention potential health complications down the line.
Abbott, February 2022
One of the most recent quality assurance debacles affected the youngest of consumers, when baby formula made by Abbott was found to contain cronobacter sakazakii, which can cause a dangerous bacterial infection. The formula was manufactured in Sturgis, Michigan using faulty equipment, and did not meet industry standards of cleanliness.
Two separate whistleblower reports were filed with OSHA in 2021, ultimately causing the plant to shut down earlier this year. The shut down contributed to a nationwide shortage of baby formula, and three infants are known to have died after consuming the contaminated formula.
It is always unacceptable to put innocent lives in danger. The failure in quality will undoubtedly follow the company for a long time to come.
While Abbott did eventually voluntarily recall the formula, there are many questions about the timeline of events. It appears that the first OSHA complaint was filed several months before the FDA completed an inspection, and that inspection was conducted four months before the product was finally recalled from shelves.
Facilities should not rely exclusively on FDA oversight to signal when it is time to make changes. Industry standards and government regulations are important, but quality assurance has to transcend that. Internal standards in manufacturing are just as necessary as external rules. Consumers depend on it.
No manufacturer is immune from quality issues. Compliance training, regular evaluations, confidential reporting channels and other quality assurance measures have to be seen as a protection, not a burden. While safety and profits are good motivating factors for higher standards, our ultimate goal as an industry should be to earn the trust of consumers through rigorous quality assurance.
Gavin Collier is a serial entrepreneur with a background in biology, chemistry, and the law. He currently serves as CEO of Dynamic Blending Specialists.