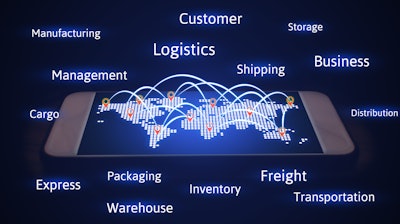
As little fanfare as a consortium called the Catena-X Automotive Network has gotten outside of its origins in the European automotive industry, this nascent but fast-growing cross-industry collaboration could well provide the blueprint for overcoming supply chain issues that have plagued the manufacturing sector for the better part of two years.
Founded in 2021, Catena-X’s expanding membership includes some of the biggest names in the European automotive value chain, from software providers Microsoft, SAP and Siemens to automakers BMW, Daimler and Ford, to Tier 1 suppliers, system providers, research organizations and recyclers.
Its goal: collaboratively implement uniform standards for the secure, transparent exchange of data and information among these entities to further enable material traceability, carbon footprint management, demand and capacity management, and the circular economy in the automotive industry.
This network-based, business ecosystem approach could be exactly the kind of construct that can help many kinds of manufacturers to overcome the disruptions, uncertainty and lack of resilience that have plagued their supply chains — and in the process, meet mounting sustainability-related regulatory requirements. Let’s take a closer look at four of the most glaring supply chain shortcomings across the manufacturing sector, and how a network-based approach could help address them.
Supply Chain Transparency
The flaw: Relying on a traditional, contract-based, linear supply chain approach with manual communication across companies hampers manufacturers’ ability to flag disruptions early and shift to Plan B (or Plan C). Too often during the past couple of years, we’ve heard stories about manufacturers being ambushed by a disruption they didn’t see coming - a lack of timely visibility caused by one-stage supply chain contracting practices.
The fix: A network that extends beyond the one-stage contractual chain and automated information flow, in which manufacturers have full, real-time supply visibility into the availability and whereabouts of critical goods and materials because they are connected to and sharing data with multiple tiers of suppliers. A manufacturer gains a clear business advantage when they can anticipate disruptions sooner, then identify alternative sources that are part of the network (even though they may not be part of the manufacturer’s direct contractual chain).
Regulatory Sustainability Requirements
The flaw: Manufacturers are challenged to track and trace carbon footprint and other ESG (environment/social/governance)-related information up and down the supply chain in order to meet reporting requirements, carbon-reduction targets and company ESG goals. Like most businesses today, manufacturers are being held increasingly accountable for greenhouse gas emissions, resource stewardship and ethical sourcing, meaning they must have a clear line of sight into carbon footprint, etc., not only from their own operations but beyond company walls and across the value chain. However, getting trusted, reportable and auditable data on emissions, resource consumption and the like from certain suppliers can be difficult.
The fix: A network where tracking and tracing carbon footprint, material origin and other ESG-related information is a straightforward proposition because participants are sharing trusted data. Shareholders, customers, partners, investors, regulators — nowadays they all expect manufacturers to be transparent with their sustainability data. The network enables them to track data and trace the origin of raw materials, components and parts across organizations, from cradle to grave.
Leveraging Equipment Data to Optimize Production
The flaw: A lack of cooperation among the suppliers of factory equipment is causing inefficiencies in the production process. Factory operators typically use equipment from many suppliers on the shop floor. But optimizing manufacturing processes and maximizing factory efficiency can be challenging when those equipment suppliers aren’t contractually connected and collaborating to deliver the optimal outcomes for the manufacturer.
The fix: Network-based collaboration among equipment suppliers optimizes operations on the manufacturer’s shop floor. As manufacturers in Europe discuss formation of a new data-sharing consortium, this issue is among their highest priorities. When the various suppliers of a manufacturer’s factory equipment are networked, they can share data and insight in real time to collaboratively maximize production efficiency, avoid operational disruption and help their manufacturer customer maintain the quality of the end product.
Establish Trust to Break Up Data Silos
The flaw: The various segments in a supply chain are reluctant to share data with one another because they lack full confidence their data will be protected once it flows into the network. The simple fact is that companies are hesitant to share proprietary supply, logistics and operational data with a network in which their counterparts may also be their competitors. Trust and data sovereignty are genuine concerns that impede development of business networks.
The fix: Having a network governed by its members or a neutral central body, in which standards, rules and security/sovereignty measures are clearly stated and universally accepted and followed, and where the benefits of participating are clear to stakeholders. Trust among participants that their data will be protected and that they won’t lose a competitive edge by sharing it is perhaps the most important ingredient in the success of a supply network. To create that trust, it’s critical that the network’s governing body maintain the network’s integrity by establishing and upholding standards. It’s also critical that stakeholders realize clear value from participating in the network. Besides gaining supply chain resiliency and reliability, is the network providing access to new customers and markets, for example?
The growth of Catena-X, as well as other manufacturing-focused multi-industry networks like Exostar and SupplyOn, suggests that companies do indeed see value in being part of a broader business ecosystem, and that the approach they’re embracing could soon become the definitive template for modernizing supply chains around the world.
Georg Kube is the global head of SAP’s industry business units for the industrial machinery industry.