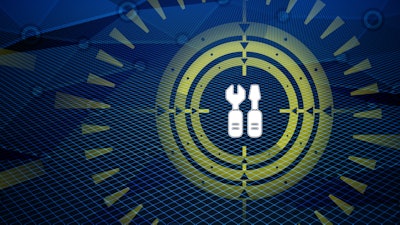
Unpatched vulnerabilities in Operational Technology (OT) and legacy systems are a persistent problem for manufacturers, and the next big breach could be just around the corner.
Why? Because patching remains a challenge for IT teams, especially when it comes to legacy environments, which a majority of manufacturing organizations still rely on. According to research, 51 percent of IT professionals say patching poses a greater challenge than vulnerability detection. While it takes threat actors an average of just five days to exploit unpatched vulnerabilities, 77 percent of organizations take a week or more to deploy patches.
One possible solution to improve the patching process: manufacturers can harness the power of AI and machine learning to apply automation and leverage real-time insights while maintaining full control to pause or rollback patches if necessary.
First, let’s explore a few more examples showcasing how AI-powered tools are helping manufacturers harden their endpoint security posture against the shifting threat landscape.
Strengthening Endpoint Security Across the Factory Floor
In response to the growing volume and sophistication of cyber threats, manufacturers are adapting by evolving their security posture to respond more quickly and efficiently to breaches. Here are a few examples of how manufacturers are leveraging AI-powered tools to strengthen endpoint security.
- Securing Industrial Control Systems (ICS) & IoT Devices: Manufacturers now deploy EDR (Endpoint Detection & Response) agents on HMIs, PLCs, and SCADA systems, which were previously left unprotected behind a firewall. Platforms like CrowdStrike and SentinelOne offer tools used to monitor anomalies in factory floor devices.
- Zero Trust Architecture: Industrial sectors are adopting Zero Trust, which treats every device (even inside the network) as untrusted until verified. A CNC machine running Windows operating system gets endpoint security policies applied to it, just like a laptop.
- Remote Work and Maintenance: As remote access to maintenance and operations increases, endpoint security protects engineers’ laptops and mobile devices through continuous monitoring and protection tools.
- Real-Time Threat Detection: AI-driven endpoint tools are helping manufacturers get ahead of vulnerabilities before they impact OT (Operational Technology) environments. For example, when it comes to robotic controllers, endpoint tools can flag when unauthorized software is installed to mitigate risk in real-time.
- Patch Management and Device Visibility: Endpoint management platforms provide real-time visibility and automate patching across all connected devices. Instead of relying on IT to manually patch a workstation, endpoint software alerts and updates the system automatically.
While all of these best practices help fortify security postures, without accelerating Mean Time To Remediate (MTTR), organizations are left vulnerable to attacks.
Where Manual Patching Misses the Mark
The manufacturing industry’s reliance on legacy systems and use of OT environments presents unique challenges that cannot be addressed through manual patching processes. A mix of cloud-based and on-premise systems with legacy components leads to fragmentation, which adds complexity and risk. In turn, patching is delayed and critical systems are left exposed for extended periods.
Patching is also necessary to avoid any system downtime, which disrupts manufacturing supply chains. Even short disruptions in system availability can cause a significant financial impact and result in losses or delayed customer deliveries. Automated patching supports higher system availability by minimizing downtime, unlike manual patching, which often involves time-consuming reboots and hands-on intervention.
Manufacturers often operate many different production facilities distributed across the globe. Manually patching these complex systems in a timely manner is unattainable. By automating approvals and deployments through automated patching, manufacturers can avoid disrupting operations, improve security posture, reduce risk and increase IT efficiency at scale.
As IT and OT systems converge, attack surfaces are expanding, giving attackers more opportunity to move laterally across networks. Automated patching helps close these gaps by significantly reducing the potential for lateral movement. Automated patch management minimizes vulnerabilities across connected systems and ensures timely remediation of known exploits, closing gaps that attackers commonly use to exploit once inside a network.
By maintaining consistent software and firmware updates across all endpoints – from engineering workstations to industrial controllers – automated patching neutralizes the attack chain and strengthens overall cyber resilience in manufacturing operations.
Nearly a decade after the NotPetya cyberattack, the manufacturing industry has made notable strides in cybersecurity, such as segmenting networks, deploying OT-aware monitoring tools, and scrutinizing third-party risk.
Despite all the progress, many organizations still leave known vulnerabilities unaddressed. Automated patching tools can help manufacturers close known security gaps swiftly, minimize downtime, and maintain compliance with regulations.