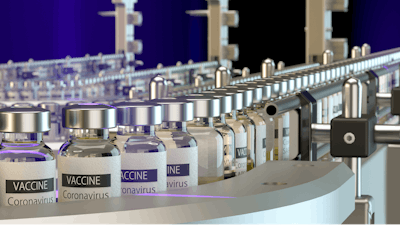
Risk management is key to effective life sciences manufacturing. While it is important in any business, in the life sciences, where patients’ lives are on the line, risk management is critical. Life sciences manufacturing is particularly in the spotlight now as companies race to manufacture the COVID-19 vaccine as quickly as possible. Even without the pandemic, regulations and standards were trending to an increased focus on risk management and risk-based thinking throughout a business.
Risk is a complex topic because the very word doesn’t mean the same thing across the board. The word itself has a negative connotation, but in the most recent standards from the International Organization for Standardization (ISO) it can refer to anything unknown — even something good. Then there’s the question of what risk management entails, who’s responsible for mitigation and how to carry out that mitigation. In life sciences manufacturing, these questions are pivotal for compliance, quality and safety.
Risk in Regulations & Standards
Every company has to manage risk. Companies that refuse to dedicate sufficient time and resources to risk management are ultimately shooting themselves in the foot. While the focus on risk and risk-based thinking might seem like an added burden to manufacturers, it’s actually in the companies’ best interest. All manufacturers have finite resources, but risk management indicates where to focus those efforts. And in some cases, it lightens the regulatory burden.
A good example of this is in the U.S. Food and Drug Administration (FDA) Q9 Quality Risk Management guidance. The guidance mentions that effective quality risk management “might affect the extent and level of direct regulatory oversight.” (1) If the FDA follows its own risk-based approach, it will spend less time monitoring and inspecting manufacturers that demonstrate the importance of patient safety in their risk management.
ISO-certified companies should be aware of and use the suggestions in ISO 31000, the organization’s risk management standard. One of the biggest changes in the most recent version of the standard is “greater emphasis on the iterative nature of risk management.” (2)
Instead of approaching risk management as a linear process, manufacturers need to think of how new factors play into mitigation and how mitigation itself can affect other processes. This emphasis on continual improvement is another area that might look like a burden, especially when you consider the move away from the old principle of reducing residual risk to as low as reasonably practicable (ALARP).
The new approach removes the consideration of how much work and expense risk mitigation presents to the company and focuses solely on patient safety and product quality. It does require more work upfront, but that work pays off in the long run. Taking care of risks before they escalate will always be more cost effective and less time consuming than after the fact.
Good for Manufacturers, Good for Patients
Of all manufacturers, life sciences manufacturers should be familiar with the concept of ensuring the cure isn’t worse than the disease. Anticipating future problems and mitigating them is now a recognized part of the risk management process. One method that’s particularly useful for this is the fault tree analysis (FTA). Manufacturers can use this to see how every product or process touches others. This in turn helps them predict how a failure or mitigation might affect the overall manufacturing process.
In any life sciences manufacturing, failure and risk are literally life-and-death situations. A risk in a pharma manufacturing line can lead to the incorrect amount of an active ingredient being included in the final product. That could result in costly recalls for the company, but more importantly it would negatively affect the health of every patient using the drug. Even a risk that would have a less dramatic impact can still cost a firm millions of dollars in rework and scrap. It makes financial sense to have good risk management in place to avoid these problems.
On the non-financial side, it saves time and anxiety to have a good risk management framework in place. As the FDA states, “Risk ranking and filtering can be used to prioritize manufacturing sites for inspection/audit by regulators or industry.” (3) This also applies to partners and customers. A customer that’s confident in a company’s ability to handle risk may decide they don’t need to conduct audits quite as often. But how can a life sciences manufacturer get their risk management to the point where it inspires this level of confidence?
Continual Monitoring of Continual Improvement
Companies that still build out risk matrices on paper or Excel will find it difficult to really manage risk. This is largely due to how difficult it is to track, trend and analyze data that’s kept on paper or spreadsheets. Companies using an electronic quality management system (QMS) will have an easier time doing this, if their QMS has risk management functionality. However, even this is limited. The typical risk management solution lets you build a risk matrix and use severity, frequency of occurrence, and detectability to calculate how severe the risk is. But that’s where the average solution’s usefulness ends.
MasterControl
Fortunately, there are more options available to manufacturers now. Using more advanced solutions, manufacturers can track and trend their risk data, demonstrating the effectiveness of their risk management to regulators and auditors. By implementing a full electronic QMS, companies will be able to connect their risk data throughout their quality system to gain insights into quality events, audits and inspections, and training.
Businesses can also accelerate their risk management with preset mitigations that can immediately be implemented when an issue arises. Even more important will be advances in artificial intelligence (AI) and machine learning (ML) which will let manufacturers use their data to predict the outcome of a mitigation before implementing it.
Conclusion
Life sciences manufacturers are always under a lot of scrutiny, but they can prepare for this by improving their risk management processes. Regulators want to see companies making risk-based decisions and effectively mitigating risk. This makes sense on a compliance and business level, due to the time and cost savings that follow.
Risk needs to be the concern of every member of an organization and employees need the proper resources to deal with it. The life sciences have reached a point where this is no longer feasible on paper documents. Modern digital tools with advanced technology are essential for managing risk on the manufacturing floor.
Sources
(1), (3) U.S. Food and Drug Administration. “Q9 Quality Risk Management.” June 2006. Retrieved from https://www.fda.gov/media/71543/download
(2) International Organization for Standardization. “ISO 31000:2018 Risk Management Guidelines.”