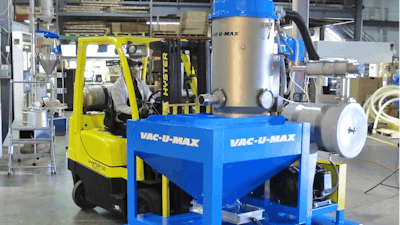
Under intense scrutiny since the U.S. Chemical Safety and Hazard Investigation Board’s (CSB), released its Combustible Dust Hazard Study, OSHA is taking action to amend is General Industry Housekeeping provision, 1910.22. The amendment to the housekeeping requirements comes as a result of employers’ misinterpretation of housekeeping standards already included in the provision.
In a recent hearing before the Senate Subcommittee on Employment and Workplace Safety, Edwin G. Foulke, Jr., Assistant Secretary of OSHA, said the provision will “state more explicitly what has always been true: that the standard applies to accumulations of dust that contribute to an explosion hazard. This clarification of language in the Housekeeping provision will eliminate any doubt that employers are obligated to prevent combustible dust from accumulating in their workplaces.”
Although OSHA’s General Industry Housekeeping provision 1910.22 does not specifically address housekeeping and fugitive dust, other OSHA standards such as Dust Control Handbook For Minerals Processing and OSHA’s Grain Handling Facilities Standard or the Mine Safety and Health Act regulations for coal mines do address fugitive dust and suggest that operations “eliminate the use of compressed air jets to clean accumulated dust from the equipment or clothing and substitute a vacuum cleaning system” and “use a vacuum cleaning system to clean spills and dust accumulations. Avoid brooms and shovels.”
However, there is a noted lack of regulation regarding the handling of fugitive dust for general industry including food products, rubbers, metal, wood, pharmaceuticals, plastics, paint and coatings and synthetic organic chemicals.
Vacuum Cleaning First Defense in Controlling Fugitive Dust
In nearly all industries, with the exception of the metals industry, the NFPA recommends vacuum cleaning as the preferred first defense method of controlling fugitive dust. NFPA 654 states, “vigorous sweeping or blowing down with steam or compressed air produces dust clouds.” Specifics on NFPA standards in relation to particular industries will be covered later.
Despite the recommendations of NFPA and OSHA standards, many companies today still use air compressors and brooms to clean surrounding equipment and areas of dust and debris. This may be due to the misconception about industrial vacuum cleaners and sheer oversight when reviewing production processes. When a process has been in place for decades, it becomes somewhat transparent and the standard, ‘if it ain’t broke, don’t fix it’ often prevails.
The problem with using brooms and air compressors is that they just blow the dust around resulting in small particles that settle onto elevated surfaces.
In an effort to bring a greater awareness to the severity of poor housekeeping methods, OSHA launched a National Awareness Program (NEP) focusing “on workplaces where combustible dust hazards are likely to be found and lists different types of materials that can generate combustible dust,” said Foulke at the Senate hearing.
“Industries covered by the NEP include agriculture, food processing (including sugar), chemicals, textiles, forest products, metal processing, tire and rubber manufacturing, paper products, pharmaceuticals, recycling operations and coal handling and processing facilities. These industries deal with a wide range of combustible dusts with differing properties, including metal dusts such as aluminum and magnesium, wood dust, coal and carbon dust, plastic dusts, biosolids, certain textile materials and organic dusts such as paper, soap, dried blood and sugar.”
Although using vacuums isn’t new to these industries, many companies have tried in the past to use shop type vacuums to clean up dust and debris and have found them inadequate under the rigorous demands in the processing industry.
In stark contrast to the weak shop type vacuums, powerful industrial vacuums can suck up tons of material an hour but most people don’t associate that type of volume with vacuum cleaners. It’s not common sense. People have a concept of what they have at home or in their workshop and they often need some education.
Frank Pendleton, founder of Vac-U-Max, to prevent dust explosions in textile mills, developed the first air operated industrial vacuum. Firsthand experience taught him the fire hazard had to be safely and efficiently removed, and he knew the dust and lint surrounding oiled textile machinery was a time bomb ready to go off. Dissatisfied with traditional compressed air hoses that simply blew unwanted debris around and aware that existing electrical vacuums were not only underpowered but also posed a real ignition risk due to sparking on start up, Pendleton began engineering a working solution. In 1954, he introduced the first air-operated vacuum cleaner, or air vac, which was three times as strong as its electrical counterpart and posed no sparking hazard.
Since then, Vac-U-Max, located in Belleville, NJ, has been the pioneer in solving vacuum-related challenges in a wide range of manufacturing and industrial settings from powder coating and metalworking to chemical and pharmaceutical applications.
Vital Housekeeping Standards from OSHA and NFPA
Although there has been many technological advances over the last 50 years to prevent dust explosions, good “housekeeping is vital because without the accumulation of significant amounts of combustible dust, catastrophic secondary explosions will not occur,” says Foulke.
Of the 17 existing standards actively targeted by OSHA (which includes 6 industry specific standards), housekeeping dominates the list. However, even with OSHA’s increased enforcement, NFPA standards, and the CSB’s push for tougher adherence, John Bresland
Chairman and CEO of the CSB reported at the Senate hearing that “in the two years since the CSB compiled the data for the combustible dust study, media reports indicated the occurrence of approximately 82 additional dust fires and explosions. “ He added that the “CSB estimates that a percentage of those explosions could have been prevented if there were standard housekeeping practices in place.”
After the Imperial Sugar refinery exploded due to a dust explosion OSHA launched and intense campaign targeted at preventing additional mishaps including distributing a fact sheet, HazardAlert: Combustible Dust Explosions that addresses secondary explosions and states, “due to poor housekeeping practices, an initial explosion may dislodge into the air the dust that is accumulated on the floors, beams, and other areas of a workplace. This dispersed dust, if ignited, may cause one or more secondary explosions. These secondary dust explosions can be far more destructive than a primary explosion due to the increased quantity and concentration of dispersed combustible dust. Many deaths in past accidents, as well as other damage, have been caused by secondary explosions.”
The Hazard Alert also references several NFPA standards that address the need for companies to employ vacuum cleaners in housekeeping practices to prevent catastrophic explosions.
Foulke again addressed the need for complying with housekeeping requirements. “The fatalities and injuries at the Port Wentworth sugar refinery probably could have been prevented, had Imperial Sugar complied with existing OSHA standards on housekeeping and other OSHA requirements.”
After Imperial Sugar’s Port Wentworth sugar refinery exploded the company willfully refused to remedy similar conditions at their Grammercy plant resulting in more than $8.7 million of proposed penalties for both plants, the third highest proposed penalty in OSHA’s history.
The relative cost of even the most elaborate central vacuum system is minute compared to the loss of life that occurs from secondary explosions or the fines levied against a company that fails to proactively protect their workers.
Although the majority of companies aren’t in willful violation of the standards, a lack of understanding of housekeeping standards and misconception of the relatively low cost of vacuum systems prevail in the industry. Often times, the addition of industrial vacuum cleaners to the housekeeping routine produces additional cost benefits in terms of increased production, reclamation or wage savings.
Applying Housekeeping Standards According to Application
The proper selection of an industrial vacuum cleaning system is based primarily on the application. In some cases small air and electric powered drum- style units will suffice, while others require a central large electric and diesel powered units for multiple users and filtration systems capable of capturing particles that are invisible to the naked eye.
Some applications require sophisticated customized vacuum cleaner installations. For other applications, compact, off-the-shelf vacuum systems are perfectly adequate when replacing crude or unnecessarily hazardous cleaning methods, such as the use of compressed air hoses for blowing debris.
Often, users of industrial vacuum cleaning systems may assume they need a custom, one-of-a-kind solution when their application actually calls for a pre-engineered product. In other words, most applications require standard equipment that offers the option capabilities to best fit an application.
Because proponents of H.R 5522 are urging the Senate to ensure OSHA mandates combustible dust safety through the use of NFPA codes, it is suggested that companies proactively follow these guidelines when setting up a good housekeeping program.
The NFPA standards that the OSHA Hazard Alert refers to being applicable to dust explosion hazards are NFPA 654, 61,484,664 and 655. Except for NFPA 61 and 664 that deal with combustible metals and food/agriculture products respectively, the fugitive dust control and housekeeping standards are generally the same for manufacturing, processing and handling of combustible particulate solids, wood processing and woodworking facilities, and also for sulfur.
In brief, the housekeeping the standards call for establishing regular cleaning frequencies to minimize dust accumulation on walls, floors, and horizontal surfaces such as equipment ledges, above suspended ceilings and other concealed surfaces. The standards further state that vigorous sweeping or blowing down with steam or compressed air should only take place after the area or equipment has been vacuumed due to the creation of dust clouds by the other methods.
Standards also call for vacuum cleaners to be specified for use in Class II hazardous locations or shall be a fixed pipe suction system with a remotely located exhauster and dust collector. When flammable gasses are present, vacuum cleaners need to be listed for Class I and Class II hazardous locations.
NFPA 61 for food and agricultural processing plants have somewhat reduced precautions than the previously listed standards and NFPA 484 for combustible metals requires that dust and particles be cleaned with non conductive scoops or soft natural brushes or brooms before the dust is vacuumed. In addition, vacuums are suggested to pick up dust that is too small to be picked up with brushes. Blowing combustible metal dust with air compressors is not permitted.
For cleanup of truly explosive materials such as gunpowder, rocket propellant, sodium azide, aluminum powder, and others which can explode if collected in dry form, a Submerged Recovery Vacuum Cleaner is available and designed specifically to pick up explosive powders safely. The explosive or hazardous material is submerged under fluid to render it inert. The unique design includes not only a high liquid level safety shut-off, but also a low liquid safety shutoff to prevent vacuum operation if insufficient liquid is in the drum.
Housekeeping for Fine Powders and Chemicals
Industrial vacuum cleaner experts, such as Vac-U-Max are skilled at designing systems around a company’s particular needs. For instance, when a custom job shop fabricator faced potential flammability issues because they couldn't adequately sweep the fine powder coating residue from the floor, lights, booth walls, and components of their shop; and, the shop type vacuums they had been using posed a static electric shock to the workers, productivity suffered. Not only did they have to vacuum but also clean by hand using wet rags to prepare booths for the next powder coating job.
The fabricator sought out VAC-U-MAX, which offers the industry's only written static control guarantee. To eliminate any shock, fire, or explosion hazard associated with electric or engine driven units, a Venturi compressed air-powered vacuum was installed with antisparking vacuum inlets and grounding lugs, static conductivity from end to end, including a static conductive hose with internal ground wire and grounded end cuffs, that prevent static build up.
To further reduce sparking danger, static-conductive filters were used, rated 99.9% efficient at one micron, which virtually eliminated any fine particle discharge from the vacuum's exhaust back into the work area. This helps to create healthful, productive breathing conditions in the workplace.
Furthermore, a unique pulse jet filter cleaning system on all the company's air vacs not only increased color changes in the powder coating industry but also ensured high vacuum efficiency while virtually eliminating clogged or "blinded" filters. By simply pushing a button on the air vac, the operator can backwash the filter with compressed air instead of taking the vacuum apart to clean the filter by hand.
Housekeeping for the Food Industry
When a major food company was looking for a simple way to get away from blowing compressed air to clean devices and components in their pasta plant, they too hired the experts to design a system that gave them more control over the dust and debris. However, unlike the two smaller applications above, this system called for a central vacuum cleaning system.
The application for sanitation and cleaning in its pasta processing area and packaging department required a vacuum cleaning system rigorous enough for continuous cleaning in a 24/7 operation; and, the technical services manager wanted to use 20 pickup points from each central vacuum producer.
For this application, five VAC-U-MAX systems, designed from standard pre-engineered models, were customized to provide the use of up to 20 pickup points from one central vacuum producer. The systems were easy to operate and the units allowed the pasta producer to clean very specific areas.
For many manufacturers and processors, industrial vacuum cleaners are now being completely integrated into production and process systems, and are quickly becoming a key component of critical strategic issues that range from productivity to environmental safety and worker health.
Regardless of the political aspects of this bill, companies need to be proactive in implementing standard housekeeping practices. Since 2006, there have been 82 dust fires and explosions, nearly one a week, and no company executive wants to be responsible for allowing the makeup of a catastrophic explosion.
VAC-U-MAX is a premier manufacturer of industrial vacuum cleaning systems for production lines and other dust-intensive areas. With a VAC-U-MAX heavy-duty industrial vacuum cleaning system on site, both capital equipment and employees are safer and cleaner.
To read more about VAC-U-MAX solutions in the cement industry visit www.vac-u-max.com and click on case histories on the vacuum cleaning page or contact us at 1-800-VAC-U-MAX (800-822-8629); email [email protected].