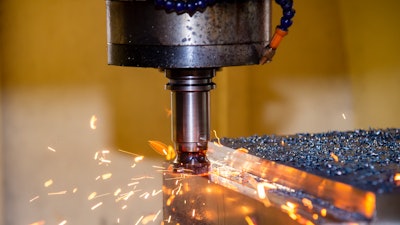
DarkAero, an aerospace company based in Madison, Wisconsin, aims to make aviation more accessible and efficient by providing aircraft kits that enthusiasts and builders can assemble themselves. Central to its manufacturing process is the Tormach 1500MX CNC Mill.
DarkAero’s Ambitious Vision
The company is developing an experimental aircraft designed for speed, long-range travel and efficiency, with an emphasis on components that are lightweight and ready for assembly and without complex requirements.
Leveraging multiple Tormach machines, DarkAero not only prototypes but also manufactures these critical parts.
“We’re now transitioning from the prototyping stage into flight testing and production activities," DarkAero Vice President and Co-Founder Keegan Karl said. "Throughout the whole process, we have been using Tormach equipment, including the 1100 PCNC and now our newest model, the 1500MX.”
Impact of Tormach 1500MX
DarkAero uses Tormach machines to craft authentic, production-ready aerospace parts. This strategy ensures a smooth, efficient manufacturing process that aligns with its innovative business model.
The Tormach 1500MX has been a game-changer for DarkAero as the new machine’s capabilities have drastically improved workflow, especially in terms of production readiness and precision.
“We were really excited to have the very first 1500MX unit in our shop to test out and see what it’s capable of,” Karl said. “We learned quickly that this machine is extremely capable. The spindle can go up to 10,000 RPM. It also has rapid movements of 1,200 inches per minute for X and Y and 600 inches per minute for Z, which means it has a greater rate of material removal than the previous model.”
One of the standout features of the new Tormach 1500MX is its large machining envelope, which allows for the creation of bigger parts. The machine also includes through-spindle coolant and a washdown feature, significantly reducing the manual cleanup and setup time.
“On the 1500MX, the coolant comes out of the spindle head and can go through the tools, which helps in reducing tool wear, improving cutting efficiency and maintaining tighter tolerances on the machined parts,” Karl said. “It also has a washdown feature that takes all the chips generated during the machining process and funnels them into a collection unit at the back. This is a huge upgrade from what we had before.”
Impact on Production
When it comes to production, the new Tormach 1500MX has allowed DarkAero to streamline its manufacturing process, making it more efficient and less error prone. The machine’s automatic tool changer and built-in camera for monitoring crashes are just a few of the features that enhance its usability and reliability.
“The automatic tool changer is a significant time-saver,” Karl explained. “You can upload your program, hit go, and then walk away to get other things done without worrying about chip evacuation or changing out tools. The built-in camera records any emergency stop events, helping us diagnose problems quickly.”