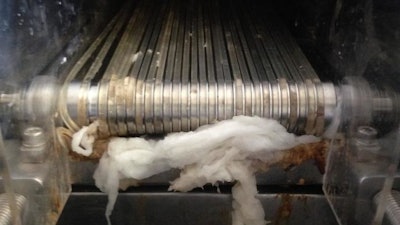
DURHAM, N.C. -- As legend has it, when French workers felt their livelihoods threatened by automation in the early 1900s, they flung their wooden shoes called sabots into the machines to stop them. Hence the word sabotage.
Instead of wasting good footwear, perhaps they should've tried wet toilet paper.
In two new papers published in the journal Science of the Total Environment, engineers from Duke University report on results from the first large-scale, real-world field trials of critical components of their off-grid sanitation system. Since 2011, the Bill & Melinda Gates Foundation's "Reinvent the Toilet" initiative has invested more than $200 million to fund these and other efforts to create small-scale sanitation systems to serve the needs of the 4.2 billion people who lack safely managed sanitation worldwide.
While their nutrient removal processes need improvement, the researchers say they were pleasantly surprised at how long the system's components lasted. They were also reminded of just how important cultural practices can be to the success of a global engineering challenge.
"The first step in our reinvented toilet system separated the solid and liquid waste through a conveyer belt made of rubber bands," said Brian Hawkins, research scientist in the Duke Center for Water, Sanitation, Hygiene and Infectious Disease (WaSH-AID). "It works great in India where they have a washing culture, but in South Africa, where they have a wiping culture, the toilet paper got into the mix and gummed up all of the gears. That resulted in the system needing cleaning every couple of days, which is not sustainable."
For the Gates-funded sanitation systems to be considered successful, they must not only remove pathogens from human waste and recover resources such as energy, clean water and nutrients, they have to do this "off the grid," without access to external electricity or water sources. To top it all off, the systems must cost less than five cents per user, per day--that's 200 users for $10.
The treatment hardware for the prototype sanitation system that underwent field testing at a textile mill in Coimbatore, India.Shamsheer Yousaf
Along with Jeffrey Glass and Brian Stoner, both faculty members in Duke's Department of Electrical & Computer Engineering, Hawkins has worked on his system at RTI International and Duke Engineering for almost a decade. After testing the liquid treatment system at large scales in real-life settings, it appears that the team's dedication is beginning to pay off.
"The big thing we were trying to find out is how long we can run this system before it needs critical maintenance," said Hawkins. "And you want to do that in as close to real-life situations as possible."
Throughout much of 2018, the Duke researchers installed a prototype waste treatment system at two locations -- a women's dormitory at a textile mill in Coimbatore, India and a communal ablution block at the edge of Durban, South Africa. Over the course of eight months, both systems served up to 50 potential users at any given time, processing more than 11,000 liters of waste throughout the field trials.
While the problem of toilet paper was an important discovery, the primary purpose of the trials was to test the longevity of the critical components of the liquid treatment process. After solids are separated from the liquids, they are pushed through a large activated carbon filter.
While this removes almost all of the biosolids, it does not disinfect the water or remove any dissolved salts. But that's okay, because the researchers can make use of one problem to solve the other. Electricity is run through the water to break down the molecular bonds within the remaining salts to produce chlorine-containing oxidants, a powerful disinfectant.
"Electrochemically treating hazardous waste has a lot of benefits," said Glass. "You don't have to ship or handle any chemicals for the disinfection, and the process can be very efficient."
Depending on the specific chemistry of the water, however, the electrical leads needed for this process can corrode quickly. The researchers also weren't sure how much use the activated carbon filters could handle before needing to be replaced. But the field trials helped alleviate those fears.
"Both trials went for eight months and the filters never failed. I had it in my head that it'd be great if they could last a year, and so far it looks like they might be able to," said Hawkins. "So long as we cleaned the electrical system periodically, it lasted for hundreds of hours of service. That's a component that, if you had to replace it every six months, it's not going to work out. But if you can make it last three or four years, that's okay."
In general, the field trial results were promising in regard to the system's potential maintenance needs and performance. Duke's prototype systems met all of the biological parameters and three out of the five chemical standards for liquid effluent according to recently released stand-alone sewage treatment requirements from the International Organization for Standardization (ISO). However they fell short of the standards for remaining amounts of phosphorus and nitrogen.
The textile mill in Coimbatore, India, where one of the prototype sanitation systems was tested in a real-world setting.Shamsheer Yousaf
"These two chemicals are of particular concern when you're discharging water into lakes and streams because too much of either can cause algal blooms," said Hawkins. "There are efficient ways of removing phosphorus and nitrogen at low costs for large volumes, or for small volumes at high costs, but not for low volumes at low cost. That's an ongoing topic of R&D for us."
Duke engineers are now testing solutions to such problems in their next iteration of systems in India. The new systems are more compact and efficient -- and just a little bit closer to being employed as full-scale working solutions.
"If you look at the flow diagram of our original system and what we're testing now, the components are all the same, but the newest prototypes are a lot more lean and mean," Hawkins said. "At this point we're mostly iterating on the same technologies, but not really making big changes."