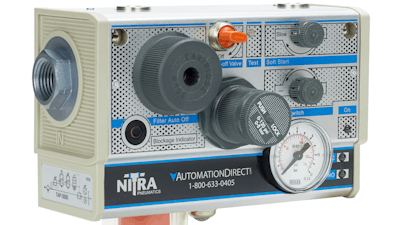
Compressed air and pneumatics are commonly used in automated machines due to simplicity, power and reliability. However, plantwide compressor and distribution systems often add unwanted water, oil and particulates that can adversely impact the pneumatics in downstream machines and processes.
Clean, dry air may enter the plant distribution system, but it still needs to be safely controlled and purified at the point of use. Total air prep units are often the best choice to provide these functions, as opposed to purchasing and assembling separate components.
Although air quality requirements vary for each application, some basic design practices apply to most pneumatic installations.
Pneumatic Contaminants & Safety
Two of the main functions of a machine air preparation unit are removal of contaminants and safe control of air. Air compressors often add airborne contaminants found in the large volume of intake air.
The design and operation of the compressor can also add contaminants such as lubricants and wear particles. Additional contaminants, such as rust and scale from storage tanks and distribution piping, also find their way into compressed air systems.
Adding to that, the distribution system may cool moist compressed air, which can cause condensate to form, causing problems that can stop production. Condensate can cause wear in pneumatic cylinders, leading to air leaks. It can also plug valve ports and orifices, resulting in malfunctions and pipe corrosion.
For these and other reasons, it is good design practice to treat compressed air both at the outfeed of the plant compressor, before it enters the distribution system, and at the point-of-use, where it is connected to a machine.
Good pneumatic system design also includes pneumatic safety. This includes the ability to dump air both manually and under emergency stop conditions. As an assembly, machine air preparation units can provide both contaminant removal and required safety functions.
Machine Air Preparation Components
The devices needed to provide proper point of use air preparation are listed below. These pneumatic components are often purchased individually and assembled as needed to address air purity and safety requirements. Partially and fully assembled options are also available to simplify design, purchase and installation.
Components in Air Preparation
- Manual Shutoff Relief Valve
- Filter
- Regulator
- Pressure indicator and switch
- Lubricator (if used)
- Air distribution block
- Soft-start/dump valve
Safe isolation of motion-causing compressed air is required on a machine, so the connection of plant air to the machine must be through a manual and lockable shutoff relief valve. A filter, with automatic drain, should be next in line to remove contaminants.
While a 20- or 40-micron filter works well in most machines, a second coalescing filter may be needed for applications where higher purity is required. The first filter removes large particles and aerosols, protecting the second and finer filter from quickly clogging.
A regulator should be used to reduce the plant air to a suitable pressure at the machine, typically 60-90 psi. To simplify maintenance, this pressure should be indicated locally, and a Digital Pressure Okay signal should be sent to the machine controller.
A lubricator can be added at this point if using pneumatic motors and air tools. However, oil is not normally needed, as most modern pneumatic components are lubricated for life at the factory.
The air is then distributed to the machine, and an electric soft-start/dump valve is used to supply air to motion-causing devices such as cylinders and actuators. This valve will exhaust air during an emergency stop, and slowly resupply air when the machine is turned back on. This prevents fast cylinder motion that can damage the machine at startup.
Assembly and Total Air Prep Units
The air preparation system can be assembled by combining the individual components in the Table. Combination filter-regulators units can simplify this assembly. However, combining multiple air-preparation functions into a single unit can be more convenient.
A total air prep unit typically includes a lockable shutoff valve, automatic drain air filter with clogged filter indicator, relieving regulator, pressure gauge and air dump. The air dump should include an electrically operated, adjustable, soft start shutoff valve and an adjustable pressure switch.
Combining all these pneumatic components in an all-in-one air preparation unit simplifies design, saves money and reduces installation space, while safely providing clean air supply to a machine.