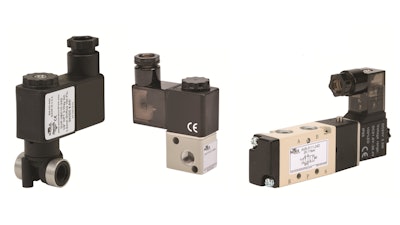
When using fluid power in industrial machine applications, pneumatic cylinders and actuators are key components for providing low cost, fast, reliable and repeatable linear and rotary motion. Air flow must be closely controlled for proper motion, a task for which a solenoid valve is often used. This article reviews pneumatic valve selection criteria, and looks at some common applications.
Picking the Right Valve
For proper control of pneumatic motion, clean and dry air must be supplied to and exhausted from the cylinders and actuators, typically by pneumatic valves, also called directional control valves. Table 1 lists leading pneumatic valve selection criteria.
Table 1: Selection Criteria for Pneumatic Valves
- Valve actuation
- Valve types and configurations
- Number of ports and position
Pneumatic valves can be activated in a variety of ways including manually, solenoid-operated and air-piloted. Manually activated valve switching options include foot pedals, toggle actuators, pushbuttons and handles.
Automated machines typically use solenoid-operated or air-piloted solenoid valves. These valves are usually activated using 12 Vdc, 24 Vac/dc or 120 Vac power. Air-piloted solenoid valves use a small electrically operated valve spool to switch air that operates a larger main valve spool, minimizing the amount of electrical energy needed to control the valve. These valves have a minimum operating pressure needed to shift the spool.
Pneumatic valves switch air using poppet, diaphragm and spool configurations. A poppet configuration is often used with both manual and solenoid-operated valves. For example, a solenoid valve directly operates a 2-way, 2-position gate valve. A diaphragm configuration is similar to a poppet valve, but a diaphragm isolates the valve from the fluid being switched.
Both solenoid-operated (direct operated) and air-piloted solenoid valves use a spool configuration with a piston and seals to switch air. This configuration is commonly used in 4-way valves and 3-position valves.
Some of the common pneumatic valve types are listed in Table 2.
Table 2: Common pneumatic valve types
- 2-port (2-way), 2-position
- 3-port (3-way), 2-position
- 5-port (4-way), 2-position
- 5-port (4-way), 3-postion
The type of work a pneumatic valve can do depends on the number of ports and positions, with several valve types available (Figure 1). The number of different pathways by which air can flow in or out of a valve are called “ways”. The number of states a valve has are referred to as “positions”. Regardless of the valve type, all valves have an air inlet port (P), and one or two air outlet ports (A, or A and B)
Figure 1: These common pneumatic valve types, with related circuit symbols, are identified by the number of ports or ways, and the number of positions..AutomationDirect
A simple 2-port or 2-way, 2-position valve has one inlet and one outlet port. This type of valve is either open or closed. It works well in air blast applications. A 3-way valve adds a port that can supply or exhaust pressure. It could be used to fill or pressurize a vessel, and to drain it.
Adding an extra exhaust port is common, but it can cause confusion with some valve types. For example, a 5-port valve is still a 4-way valve with two exhaust ports, often labeled R and S. These ports are open to atmosphere so they are the same “way”. With a 5-port valve, there is also an inlet port (P) and two outlet ports (A and B).
5-port valves are available in 2- and 3-position models. With 5-port, 2-position valves, the A and B output ports are in complementary mode. When one is supplied inlet air pressure, the other exhausts air, which works well for extending and retracting double-acting cylinders. 2-position valves are often spring return. During design, consider unintended cylinder motion after an emergency stop or during power on.
A 5-port, 3-position valve adds a center or neutral position. With both solenoids de-energized, the center position will either supply pressure to both output ports, block both outlets, or exhaust pressure from both. A closed center valve works well when holding a cylinder position. The center exhaust is used to dump air from a cylinder when not actuated, usually for safety reasons.
Following these guidelines will assist in proper valve selection for your pneumatic machine automation applications.