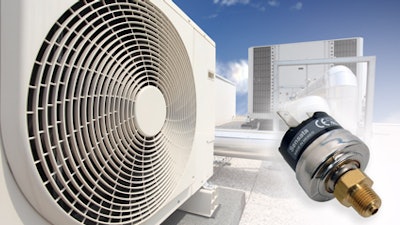
a new set of challenges for cooling system design.
Because of new government environmental mandates, cooling equipment manufacturers are migrating to less damaging, green refrigerants that do not deplete the ozone layer and have low impact on global warming.
They also need to research and pick components that can handle the specific refrigerant’s technical challenges and performance characteristics.
There are two important criteria in measuring whether or not a refrigerant is environmentally acceptable.
Ozone Depletion Potential (ODP)
Ozone depletion potential (ODP) measures the relative amount of damage a substance can cause to the ozone layer. UV radiation from sunlight causes the release of chlorine in chlorofluorocarbons (CFCs) and hydrochlorofluorocarbons (HCFCs) into the atmosphere, which then damages the ozone.
In contrast, natural refrigerants have an ODP of zero, meaning that they will not have any depleting effect on the ozone layer if they escape the system.
Global Warming Potential (GWP)
Global warming potential (GWP) is a relative measure of how much heat a greenhouse gas traps in the atmosphere. The lower the GWP, the better a substance is for the environment. GWP compares the amount of heat trapped by a certain mass of the material in question to the amount of heat trapped by a similar mass of carbon dioxide. A specific GWP is calculated over a time interval, typically 20, 100, or 500 years.
Many of the older refrigerants have a global warming potential ranging from 1,400 to nearly 4,000. One can compare varying GWP values as they relate to types of refrigerants in Figure 1. Current hydrofluorocarbons (HFC) Refrigerants R404a and R134a have extremely high GWP values ‒ 3,922 and 1,430 respectively ‒ that are harmful to the environment. By comparison, Propane R290 Hydrocarbon, which is a newer, natural refrigerant version of R404A, has an extremely low GWP of only three.
Figure 1: Global Warming Potential (GWP) of Refrigerants.Sensata Technologies
Characteristics of Natural Refrigerants
- Hydrocarbons - Hydrocarbon based refrigerants like Propane (R290) offer better thermodynamic properties and heat capacity versus older HFC refrigerants. Hydrocarbons can also provide higher device efficiency, with faster temperature recovery and lower energy consumption. Hydrocarbons have no ozone depleting properties and low GWP. However, this new generation of hydrocarbon refrigerants is highly flammable and therefore require different and safer technologies for refrigeration and cooling systems and components.
- Ammonia - Ammonia is another natural refrigerant now being used, although not as often as hydrocarbons. It measures zero for both ODP and GWP and breaks down rapidly. The challenge with ammonia is that its alkalinity is extremely corrosive, so components used in applications require careful consideration of material compatibility.
- CO2 - Carbon Dioxide - CO2 has a GWP of only one but operates at almost twice the pressure of hydrocarbons making it difficult to manage. This necessitates designing in specialized components such as pressure switches to ensure reliable operation in applications where CO2 is used, which in turn affects product manufacturing.
Pressure switches in CO2 refrigeration systems protect against high pressure burst or over pressure situations that could cause the coils to rupture. When the pressure builds up to a certain point, the switch opens the electrical contact and turns off the compressor.
When the pressure drops back down to normal levels, it automatically switches the compressor back on. But in today’s market, even more safety is needed. Since switches are an electro-mechanical device, they inherently can spark when the contacts make or break.
To prevent a spark from accidently causing ignition, Sensata has built extra safety into their pressure switches with a sealed design that ‘seals the spark’ inside by isolating the specific pressure media from the electrical switch assembly.
Each switch is manufactured with a hermetic seal around the gas path as well as a sealant around the electrical connections. This safety design eliminates the potential for explosion by stopping the gas from entering the electrical switch compartment where the arcs can be generated during contact make or break operations.
Given the changes in refrigerants being used around the world, it is clear that natural refrigerants are important to the future landscape of the industry. In order to optimize safety and efficiency, component manufacturers need to understand what kinds of hardware and systems must be specified for the implementation of these new and more technically challenging materials.