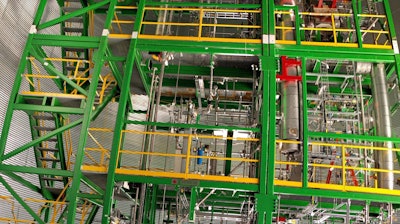
Anellotech is a sustainable technology company focused on producing cost-competitive renewable chemicals and fuels from non-food biomass (view photo in gallery).
Today, the company announced that its engineers, collaborating with petrochemical company Axens, has completed a successful continuous performance test of the TCat-8 pilot plant as part of unit commissioning in Silsbee, Texas.
The test involved continuous injection of MinFree woody biomass feedstock and production of BTX and other valuable chemical by-products.
The primary objectives of the test were met by demonstrating steady control and operation of the reactor, stripper, and regenerator fluid bed systems with continuous catalyst circulation at design pressures and temperatures.
Anellotech also filed a Form D with the US SEC disclosing a $0.8 million equity investment from a new, confidential strategic partner.
The Company has now raised a total of $3.2 million in equity and R&D funds since its last funding update in October 2016.
“Being able to operate the unit continuously this early in our commissioning program is a significant achievement, especially considering the complexity of its various recycle loops at a pilot scale.” said Chuck Sorensen, Anellotech CTO. “This operating milestone is the outcome of three years of collaborative design, project management, construction, and start-up work by Anellotech’s R&D team, IFPEN, Axens, Johnson Matthey, South Hampton Resources, and other key advisers”.
Additional tests are planned to complete the commissioning phase and then commence process development studies to acquire data for commercial scale-up and design of the process.
Anellotech is developing the Bio-TCat process to produce cost-competitive renewable aromatic chemicals (benzene, toluene and xylenes, “BTX”) from non-food biomass for use in making plastics such as polyester, nylon, polycarbonate, polystyrene, or for renewable transportation fuels.
Bio-TCat co-products, C9+ aromatics and carbon monoxide, can be used to make cellulosic jet and ethanol bio-fuels respectively, using third-party technology.
The key differentiators driving Bio-TCat’s cost-competitive advantage are its MinFree biomass pretreatment followed by a one-reactor catalytic process.
The Bio-TCat reactor outlet hydrocarbon product requires only mild hydrotreating to remove trace impurities using existing oil refining technology. By using renewable and readily available non-food materials, such as sustainably harvested wood, corn stover and bagasse, the process is less expensive compared to processes relying on sugar as a feedstock, and avoids competition with the food chain.
As a result, these renewable chemicals are expected to be produced and sold profitably either against identical, petroleum-derived BTX counterparts, or as renewable fuel blend stocks.