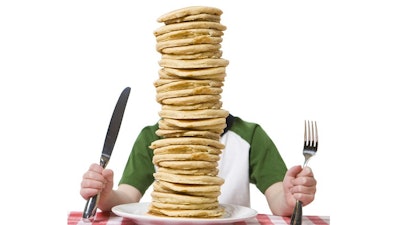
Editor’s Note: This blog is a follow-up to last week’s “A Report Card on Compressed Air Knowledge.” Click here to view Part 1.
The point least understood among the surveyed compressor users is how to size a system for the shop. We presented a scenario with five techs, each using 15 cfm tools, and gave five different compressor size (hp) options. Less than 40% picked the most appropriate option, and most incorrect answers were heavily over-sized. We see this in the field all the time. Operators routinely overestimate the size of compressor needed.
Depending on the type and design efficiency, most commercial/industrial compressors produce between 3 and 4.5 cfm per horsepower. The (simplistic) quiz scenario assumed all air users would need air simultaneously. Using 4 cfm/hp, a 20 hp compressor with 100% duty cycle would supply air to all five users. As mentioned above, 40% chose this option, but another 40% chose either the 30 or 50 hp options.
The downsides to oversizing include:
- spending more up-front for the equipment (compressors, dryers, etc).
- paying more for parts and service.
- increased wear from over-cycling (starts and stops).
- reduced energy efficiency (this applies more to rotary type machines than pistons, which mostly operate on start/stop controls).
Now factor in the reality that it is very rare for all techs to be operating air tools at the same time. So let’s say only three of five people will be using air simultaneously (total of 45 cfm). A 15 hp compressor would easily handle it. If only two out of five were using air at the same time, an efficient 7.5 hp with 100% duty cycle might suffice. Or bump it to 10 hp (40 cfm) and add 100-200 gallons of storage to be safe. Far more cost effective than buying the 20 hp.
For energy efficiency, it would be better to get two smaller machines than one large one. This also give you back-up, but it does drive up the initial cost.
If you anticipate that you will need more air in the future, arrange your compressor room/area to allow for additional machines, but only buy what you need in the short term. The money you save on energy and service will help pay for the upgrade later.
For more information, download Kaeser’s Compressed Air System Installation Guide e-book.
Michael Camber is Kaeser’s Marketing Services Manager. He is a member of Kaeser’s active training team, educating both Kaeser’s distribution network and customers on reliable and energy efficient compressed air system design. He is also KFaCT Master Certified and has completed the US Department of Energy’s Compressed Air Challenge Level