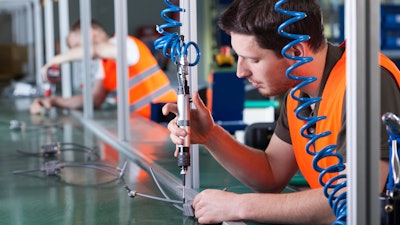
This final article in a four-part series on air compressor purchasing tips provides advice from experts on commonly overlooked maintenance considerations.
What aspects of air compressor maintenance do you feel are most commonly overlooked? Why? Are there simple ways to address these oversights?
Michael Camber, Kaeser Compressors
Michael Camber, Kaeser Compressors: Not maintaining the proper operating temperature can reduce coolant/lubricant and ultimately compressor life. The first step is to have a well-ventilated compressor room. With regard to maintenance, keep the compressor room clean and remove dirt/dust that accumulates on the coolers. Also, reduce heat in the compressor room. The cooler the compressor runs, the more moisture will condense out of the air at the aftercooler and receiver tank.
Maintain air inlet and oil filters regularly. Monitor internal differential pressure and change out the air/oil separator as needed. Many units don’t run enough and water builds up in the oil system. Drain water from the separator as needed.
Also, consider adding automatic condensate drains on moisture separators, tanks, dryers and filters. Properly size dryers for worst case (usually summertime), install and maintain coalescing filters to remove oils/hydrocarbons, and install and maintain appropriate FRLs at points of use.
Keep the electrical cabinet clean. The cabinets on some machines are better protected than others. Periodically wipe or vacuum it out (be sure to disconnect the power first!). This is most needed in high dust environments.
Some units also vibrate more than others, which can lead to loose wires, piping and hoses. Oil leaks inside the machine are a sign. Checking these points for loose connections should be made routine.
Dan Leiss, Jenny Compressors: One of the most common oversights we see are people installing the wrong air filter for the job at hand, and that can cause problems. For instance, a standard filter will trap dust particles based on micron size, while a coalescing filter will remove water and oil from the air. For some applications, such as spraying paint, an air dryer should be used with the coalescing filter so all moisture is removed from the lines.
On the other hand, some tools function better with moisture. I think the reason for this oversight is just thinking all filters are the same. But it can mean a lot in ensuring compressor performance and longevity.
Another commonly overlooked maintenance task is draining the tank at the end of each day, or more frequently in higher humidity environments. It's a simple thing, but given the frequency needed, it's often overlooked. Staying on top of the task can help prevent moisture from getting into the pump, which can spell reliability issues. We see a lot of people simply putting a sign on the compressor - or stenciling a reminder - about draining the tank at the end of each day as a way to keep this top of mind.
William Milligan, Chicago Pneumatic
William Milligan, Chicago Pneumatic: One commonly overlooked maintenance tip is draining the water that accumulates in the air receiver. However, air compressor maintenance is often overlooked entirely. It is extremely important to go by the air compressor manufacturer’s established maintenance schedule with replacing the oil and wearable parts at the recommended hour intervals. This will keep the machine at its best working ability.
The air receiver can often be the forgotten aspect of a compressed air system. As the air is compressed, cooled, and stored in the receiver, the moisture in the air condenses and collects in the bottom of the receiver. This water can damage the integrity of the receiver by rusting the walls and creating weak points. This can be solved simply by installing any kind of automatic drain, such as an electric timer drain or automatic float drain.