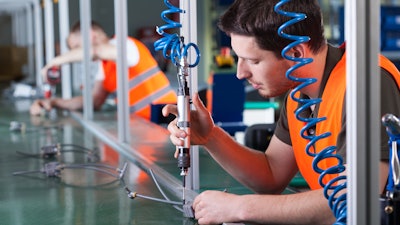
This first of a four-part series on air compressor purchasing tips gets advice from experts on selecting the right size and type of compressor that’s the best fit for your facility.
What do you feel are the most important criteria to consider when selecting the right type and size of air compressor?
Scott Baker, Quincy Compressors: Pressure, flow, duty cycle and ensuring lower energy costs.
Lane Hawkinson, Rogers Machinery Company: The main criteria is that the compressor output closely match the system demand. Doing detailed analysis of the system demand profile, such as with a compressed air system audit will insure that the correct size compressor and clean up equipment is purchased. Without data, it’s just someone’s opinion.
William Milligan, Chicago Pneumatic
William Milligan, Chicago Pneumatic: When selecting a compressor, the most important factor to understand is the current air demands of the system. Properly understanding the maximum operating pressure and the total air requirement (total CFM) will ensure the right type of compressor is selected.
Deciding between a reciprocating or a rotary screw air compressor depends on the continuous air usage needed for your system. Rotary screw compressors have a 100 percent duty cycle that is designed to run continuously, but must be sized appropriately to avoid unnecessary start and stops on the motor.
Something important to consider is having multiple smaller compressors instead of one large compressor. This provides redundancy for your system, allowing maintenance to be performed on one compressor while the others continue to operate, reducing downtime. Energy savings can also be provided by having one compressor shut down during periods of low air demand.
Chad Larabee, Ingersoll Rand
Chad Larrabee, Ingersoll Rand: The type of equipment will likely be driven by the air quality required. Do you need oil free air? What dew point is needed? Consider using ISO 8573 part 1 classifications to quantify what type of air quality you need.
Size is about summing the demand in terms of flow at required pressure. Develop a chart or table with each of the air users. Consider the variability of the flow requirements. A large intermittent user like a bag house is very different from a constant user.
Consider a margin of safety but be careful not to oversize too much or you may pay a price in efficiency. When determining pressure requirements, minimize high pressure users and consider delivering the high pressure needs through smaller a dedicated system. More pressure requires more power and consequently, more cost, so design for lowest possible pressure.
Finally, consider needs for reliability. Downtime is costly in the way of lost production, so consider redundancy. The Compressed Air and Gas Institute offers some resources on sizing at: http://cagi.org/news/Hot-Topics-Sizing-Compressed-Air-System.aspx
Paul Humphreys, Atlas Copco: To choose the appropriate compressor for application needs, plant operators need to first answer the following questions:
- What is the application? It’s important to understand the pressure and flow needed to power the application. Pressure determines the compressor’s ability to perform the application whereas flow is the compressor’s ability to continue performing that task. Having this information available will help you properly size your compressor. Knowing your application requirements will also help you decide on the type of compressor, whether it’s rotary, centrifugal or reciprocating.
- Is oil-free air needed? Certain industries and applications require oil-free air, which means there is no risk of oil contamination infiltrating the production processes and affecting the end-product. Oil-free compressors are used within industries including automotive, food and beverage, chemical, electronics, textiles, pharmaceuticals and more. Understanding your application needs and industry standards will help you decide if oil-free air is right for you.
- Is there a fluctuation in flow demand between shifts? If your application only requires full load or no load compressed air supply then a fixed speed, or idling compressor, is an appropriate solution. However, most applications have a fluctuating air demand throughout the day where a variable speed drive (VSD) compressor can benefit. A VSD compressor adjusts its motor speed to the air demand so the compressor’s output capacity matches demand.
- Are there plans for future expansion? Similar to buying a house or a car, you should consider plans for the future of your compressed air system. If you foresee changes to your manufacturing activity, it may be best to purchase multiple smaller compressors as opposed to a few larger units.
Dan Leiss, Jenny Compressors: In regards to size - it's the compressor's capacity and operating pressure that matters most. First, determine the amount of CFM (cubic feet per minute) required in your facility. Begin by adding the CFM needs for all the tools that may need to be used simultaneously, and then add another 30 percent to allow for unknown or uncommon compressor usage.
It's important to understand that CFM can be figured in three different ways, and to know the difference:
- Displaced CFM (DCFM) is simply the mathematical calculation of the bore, stroke and rpm. But it does not take into account any of the other important variables, such as temperature, atmospheric pressure, humidity, friction or heat dissipation. So, really, DCFM doesn't add much "real world" value.
- Standard CFM (SCFM) is a better measure. SCFM is the flow of free air in a standardized environment, such as 14.5 psi atmospheric pressure (the pressure at sea level), 68 degrees Fahrenheit and 0 percent humidity. Since this is a standardized metric, it allows a way of comparing compressors on an apples-to-apples level. But specific needs will affect that value of this measurement. For instance, someone working in Denver will have different requirements than someone working at sea level in Louisiana.
- Actual CFM (ACFM) is the most valuable metric because it figures in the variables that apply to a specific situation. It provides the output of the pump for the actual working conditions. But ACFM is difficult to determine, as it requires site-specific data and calculations that may be best left to an engineer. Thus, for selection purposes, the best route is to compare compressors based on SCFM ratings.
CFM is also important to know when considering whether to select a single-stage compressor or a two-stage compressor. Again, begin by listing the minimum operating pressure requirements for the tools you're going to use. This will indicate whether a single-stage compressor or two-stage compressor is needed.
Single-stage compressors are fine up to 150 psi. Higher pressures require a two-stage unit. A single-stage compressor will typically have a higher CFM rating because the cylinder draws in air and compresses it with every rotation, whereas a two-stage compresses the air up to an intermediate pressure in one or more cylinders and then passes it on to another cylinder to finish the job.
Because the air is typically passed through an intercooler between stages, a two-stage compressor is more efficient at higher pressures. One final consideration is peak air demand requirements. Many plants tend to use constant air for most applications, such as blow-down guns and air grinders. At some point, the plant may be using more air, but the tank will level that out.
In terms of the features aspect of selection, the key is to look for components that equate to durability. Specifically, look for features such as a cast-iron cylinder, a heat-dissipating head, an efficient cooling system, structural protection for critical components and fittings, a heavy-duty steel frame and powder-coat or electrostatically applied paint. Keep hose diameter in mind too. Don't skimp on a 1/4” hose if 3/8” will be needed to handle the load of more tools or longer runs.