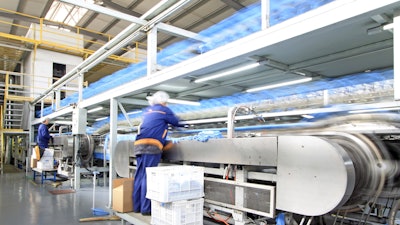
Changing consumer demands, regulatory challenges, quality concerns and decisions related to Industry 4.0 investments are impacting all areas of the industrial sector. At the forefront of many of these critical issues is the food and beverage industry. To discuss some of these unique market dynamics, we recently sat down with Jeff Seabury, industrial product manager at Legrand, a leading supplier of industrial connectivity and safety solutions.
Jeff Reinke, editorial director, IEN: How have the needs of your customers in the food processing industry changed over the past 5 years?
Jeff Seabury, Legrand: Legrand has seen our customer’s needs evolve as a result of more stringent guidelines for safety and cleanliness. The new Food Safety Modernization Act (FSMA) and HARPC guidelines have caused food and beverage facilities to increase focus on cleanliness and safety. Food-processing plant managers are looking for products that can stand up to the rigors of high-pressure wash downs and deliver safe electrical connections that minimize arcing. It is critical that facility workers can ensure a machine cannot be turned on until a safe electrical connection is made.
JR: When speaking with customers about upgrading their facilities, what are the most common obstacles and how do you work through them?
JS: The most common obstacles food and beverage facilities face are operational challenges and cost pressures. Food-processing plant managers are demanding machines that improve operational efficiency, reduce costs, and increase uptimes. This has led to increased requirements for automation, energy efficiency, and integrated solutions. The ability to obtain funding for these types of capital expenditures can be easier for a larger company than for a smaller company.
However, smaller companies can still upgrade their plants to comply with FSMA requirements without capital expenditures for new machines. Legrand’s wiring devices and cords with embedded antimicrobial additives, stainless steel safety switches, cable management systems and wire mesh grips are among a wide range of cost-effective, incremental options to improve a plant’s safety plan. These options are also beneficial for larger facilities who are looking to trim costs.
JR: Looking specifically at food and beverage processing, how has Industry 4.0 impacted their approaches to safety and avoiding recalls?
JS: The increased focus on food safety and regulation has led companies to put more effort into tracing food throughout the value chain. FSMA requirements also mandate traceability of product and of certification and documentation. Our customers within the food and beverage industry are exploring how they can invest in and implement traceability tools. Like any major equipment or technology upgrade, this is not a quick and easy process and will take time for facilities to implement.
JR: In your opinion, if those who have experienced recalls could go back and do one thing differently, what would be most commonly addressed?
JS: The most common theme we hear is the need for enhanced preventive measures for the food and beverage facility. Over the past five years, many food and beverage facilities placed the majority of their focus on post-production inspection. While this is an important piece of preventing a recall, building different preventive measures from the very beginning of food production is critical. This is a major focus of FSMA, which will force food and beverage facilities of all sizes to address this.
JR: What market dynamics or technological advancements do you feel could have the most impact on food processors over the next five years?
JS: I think IoT and the rise of Smart Manufacturing will have a big impact on the food processing industry. IoT enables so many possibilities for food processors to become smarter and more efficient. For example, the use of embedded sensors and connected devices provides remote access to facilities and allows food processors to transmit, collect and analyze data in real time. Being able to access and analyze data will allow companies to increase efficiency, monitor and analyze equipment and assets, and enable them to provide new products and services.
FSMA is one of the most sweeping reforms of food safety and regulation in decades and will continue to impact food processors in the coming years. Facilities must commit to tighter safety controls, greater documentation and continuous safety improvements across their entire enterprise. This requires facilities to implement entirely new systems for not just meeting the standards, but in hopes of exceeding them. This is a process that will take time and investment by everyone in the industry as plants and facility managers make ongoing improvements to food safety in their facilities.