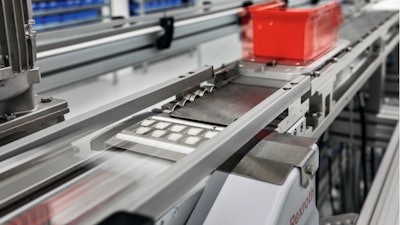
It’s estimated that over the past three years a total of 82% of manufacturing companies have experienced unplanned downtime and that unplanned downtime is costing them as much as $260,000 an hour. Surprisingly, it’s also estimated that more than 70% of respondents weren’t fully aware of when their equipment is due for maintenance, upgrade or replacement. Even with the knowledge that unplanned downtime is so costly, manufacturers’ most frequently used approaches to maintenance — which should ideally help reduce unplanned downtime — are not necessarily effective in reducing it.
Unplanned maintenance on a conveyor system can result in downtime that impacts productivity and throughput — which can be costly downstream. Replacing traditional conveyor systems with a software-driven, intelligent, high-speed conveyor system can play a critical role in minimizing overall downtime by increasing throughput and optimizing processes for maximum productivity.
Implement Predictive Maintenance
A recent GE Study found that only 24% of operators describe their maintenance approach as “predictive,” or based on data and analytics. The rest either took a reactive or time-based approach. In terms of unplanned downtime associated with each approach, reactive approaches averaged 8.43% annually, with 7.96% for planned and 5.42% for data/monitoring approaches.
With the data gathering capabilities of intelligent high-speed conveyors, operators gain visibility into the entire system and can stay on top of downtime-causing events before they impact production. Compared to traditional systems, which tend to only have external sensors, high-speed conveyors have data gathering capabilities within the system. This means that not only can an operator track external data, such as where pallets are positioned and where they’re going, but intelligent conveyors also track internal components, such as volts, currents, position and errors, to ensure the conveyor is running at peak performance.
Implementing modern, high-speed conveyors with advanced predictive maintenance capabilities keep unplanned downtime low and productivity high.
Optimize Changeover Process
Traditionally, conveyors require tools and operator intervention to adjust the equipment for product changeovers. For example, a consumer packaged goods (CPG) manufacturer might be packing 16-ounce bags of product, then have to change over to pack 8-ounce bags to fulfill an order. This means that in a conveyor application, the tooling would be set to hold up the 16-ounce packaging as it flows through the line and would have to be adjusted to accommodate a smaller 8-ounce bag. In some production lines, this process could take multiple hours.
Instead of having to stop production and manually adjust the conveyor for the 8-ounce bags — a process that would require equipment downtime and lower productivity — software-driven high-speed conveyors enable the change in parameters as simply as pushing a few buttons and have it automatically applied to the system.
By leveraging automation and software to streamline changeover processes, production staff can maximize uptime and throughput regardless of product variations. As an added benefit, longer production runs to keep inventory are not necessary. With a flexible conveyor system, manufacturers can start producing on demand and use the storage room for more valuable operations, such as additional production lines.
Reduce Cycle Times
The latest generation of transport systems offer a valuable tool that is relatively easy to implement. These easily reconfigurable transport systems let manufacturers adjust their production processes built around the system with minimal cost and time required. Manufacturers who have installed this type of transport system have been able to dramatically improve productivity and reduce cycle time. The ability to independently program each pallet, varying its speed and direction, gives assemblers and manufacturers the power to target specific process bottlenecks and keep their production lean as they respond to the needs of their markets and customers.
Linear motor-driven, high-speed conveyor systems combine versatile motion with transport speeds up to four meters per second, significantly faster than many standard conveyors. In addition, workpiece pallet changeover time is under one second. And since each pallet is independently programmable, its position can be tracked and documented with total accuracy. Faster throughput, tight position accuracy and pallet-level tracking can increase productivity, thereby helping reduce cycle time and overall manufacturing and maintenance costs.
Conclusion
When determining if intelligent, high-speed conveyors are worth the investment, consider the overall ROI, in particular the long-term maintenance benefits. While traditional conveyors tend to be less expensive up front, the maintenance costs will stack up down the road. Traditional conveyors can be less durable, which means excess maintenance and repairs will also be required to keep operations running smoothly.
Making an investment in intelligent conveyor systems unlocks advanced automation capabilities that will help lower maintenance costs and result in less costly unplanned downtime from inefficient production processes.
Abdullah Al Ramadan is Product Sales Manager, High Speed Conveyance, Bosch Rexroth Corporation.