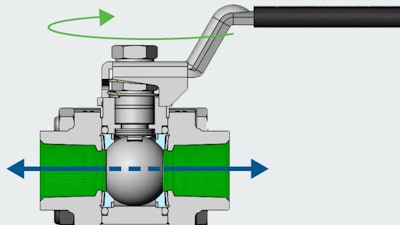
Choosing the proper components for your industrial fluid systems is critical to ensuring they function as intended. One of the most important components to consider are the valves, which give operators the ability to control system fluid flow in ways that are most appropriate for the application’s needs.
It is important to consider the factors that affect complex fluid system design, including:
- Do you need to stop and start flow?
- Do you need to control the direction of the flow?
- Do you need to regulate flow rate?
- Do you need to protect your system from overpressure?
- How often will you cycle the valve?
You should ask all these questions about your fluid system before finalizing your valve selection. In this article, we will provide examples of different industrial valves to help you make the right choice.
Safety First
Fluid systems sometimes operate at high pressures and temperatures, and occasionally they carry hazardous materials that could pose a threat to the operators if leaks occur. To ensure fluid systems do not pose unnecessary hazards, best practices for installation and operation should be followed.
Valves play critical roles in enabling safely functioning fluid systems. For example, a safety shut-off valve or pressure relief valve can prevent your system from reaching overpressure, a potentially dangerous scenario that may lead to a blowout. That is why it is so critical to select the right valve for the function you are trying to achieve, which starts with understanding how flow operates within your system.
Understanding Flow
Ultimately, valves are designed to control flow, which is defined as a substance’s movement in a steady and continuous way through your system from higher pressures to lower pressures. Using a flowmeter, the pace of flow is recorded as a ratio of distance or volume per unit of time. For example, flow might be measured as meters per second, liters per minute, gallons per day, or other similar measurement criteria.
The diameter of a valve’s end connection and its flow path determine how well valves allow flow to occur. Manufacturers often include a flow coefficient, or Cv, with their valves, which gives operators a better understanding of how much flow a valve will control. The higher a Cv, the higher the flow rate – although, higher is not always better. The Cv you choose is highly dependent on the valve type and application. In some situations, that may mean the Cv will be close to zero.
While this may seem complicated, manufacturers can often help you determine the right valve selection for your application. To determine Cv or flow based on pressures, flow rates, temperatures, and media within your system, ask your manufacturer if they have a Cv calculator to offer the guidance you need.
Valve Functions and Types
Choosing the right valve for your application may initially seem overwhelming. After all, valves come in many sizes, configurations, materials of construction, and actuation modes. To make the best choice, it is always good practice to ask the first question in valve selection: What do I want the valve to do? Once you have answered that question, you can more easily decide what specific valves you need, which generally fall into one of five categories.
1. On/Off is the most basic type of valve function. On/off valves start or stop the flow of fluid, and there are many different types of valves to choose from, including:- Ball valves. Ball valves can be used in a wide range of applications, from general-purpose to critical-service applications. They are useful for reliable, leak-tight shut-off and have a low overall cost of ownership. (Figure 1)
Figure 1. Ball valves can be used in a wide range of applications, from general purpose to critical-service applications. They are useful for reliable, leak-tight shut-off and have a low overall cost of ownership.
- Bellows valves. Bellows valves are packless, making them a good choice when the seal to atmosphere is critical and access for maintenance is limited. A welded seal divides the lower half of the valve, where the system media resides, from the upper parts of the valve, where actuation is initiated. The stem, which is entirely encased in a metal bellows, moves up and down without rotating, sealing over the inlet.
- Diaphragm valves. Diaphragm valves have a long cycle life, provide effective shut-off, and can be found in a wide variety of sizes, materials, and configurations. Actuator options include manual, pneumatic, and locking. Consider a diaphragm valve in high-purity and ultrahigh-purity applications. (Figure 2)
Figure 2. Diaphragm valves have a long cycle life, provide effective shut-off, and can be found in a wide variety of sizes, materials, and configurations. Actuator options include manual, pneumatic, and locking. Consider a diaphragm valve in high-purity and ultrahigh-purity applications.
- Gate valves. Gate valves are designed primarily for blocking flow rather than regulating it. They contain a plate-like barrier (gate) that can be inserted into the stream of a fluid to block its flow.
- Rising plug valves. Similar to a gate valve but in instrumentation sizing, a rising plug valve lifts a plug out of the flow path to achieve a full flow. They are often used in applications requiring a straight-through flow path and rough-flow control. (Figure 3)
Figure 3. Similar to a gate valve but in instrumentation sizing, a rising plug valve lifts a plug out of the flow path to achieve a full flow. It is often used in applications requiring a straight-through flow path and rough-flow control.
2. Flow control valves are designed to regulate the flow of a fluid through the system. The amount of regulation depends on what type of valve is selected and can range from simple regulation to fine metering. The most common flow control valves are needle valves (Figure 4), which can provide on/off functionality if necessary. Orifice size, stem type, and stem position, which are controlled by the turning of the valve handle, will determine the pace of flow.
Figure 4. Needle valves are commonly used to control flow in general- and severe-service applications. They provide reliable and consistent flow control and can be found in a variety of materials, sizes, and end connections.
3. Directional flow valves guide the flow in the proper manner and are used to change the direction of the flow, if desired. The most common valves used for directional control are check valves (Figure 5) or multiport ball valves. It is important to note that directional flow valves do not throttle flow; instead, they operate in either the on or off position.
Figure 5. Check valves are designed to allow fluids to flow in one direction only and are typically rated for use in medium- and high-pressure fluid systems. They are useful to control backflow in general-service and high-purity applications.
4. Much like the overpressure valves, excess control valves are designed to prevent problems if the flow levels at the valve rise to unsustainable levels. If excess flow happens downstream, the valve’s poppet is activated to the fully forward position, which prevents an uncontrolled release of system media.
5. In the case of overpressure protection valves, the goal is to prevent pressure buildup beyond a preset limit. For this application, systems typically rely on relief valves (Figure 6) or rupture discs. Relief valves are essential to any system that operates under pressure to avoid blowouts and can be calibrated to open after the pressure reaches predetermined levels. They are generally considered the last line of defense when pressures rise too high and can protect plants by allowing production to continue by relieving overpressure when it occurs.
Figure 6. Relief valves provide simple, reliable overpressure protection for a variety of general industry applications and have an easy external set pressure adjustment.
Consider Cost of Ownership
The true cost of a valve is not its purchase price – it is the purchase price plus the cost of owning and maintaining or replacing that valve over time. To calculate the cost of ownership, you must know how long a valve will operate in your system between maintenance checks.
Maintenance costs must not only be calculated on the cost of replacement parts, but also in labor and downtime. Note that some valves are much easier to service than others. Some can be serviced in place; others must be removed from the process line.
Making the Right Selection
As you design your fluid system to be as optimized as possible, selecting the right valves to meet your application needs is important. The better your understanding of each valve and its proper function, the better able you will be to make the decision that most fully meets your specific needs.
Work with a supplier who offers training on valve selection, identification, and troubleshooting so your team can remain up to speed and knowledgeable about the latest in valve innovations.
An original version of this article appeared on the Swagelok Reference Point blog here: swagelok.com.
---
Joe Bush is a Senior Product Manager for Swagelok Company.