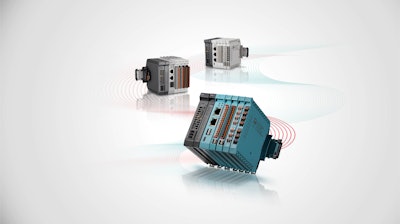
Manufacturing operations everywhere are striving to improve the intelligence of their systems through digital transformation and industrial internet of things (IIoT) implementations. In all industries—and on equipment ranging from individual machines to factories and processing plants, to energy generation and distribution equipment—end users need flexible ways for connecting with growing numbers of field sensors and transmitting that data to higher-level controllers and computing systems.
Due to the wide variety of possible input/output (I/O) signals and controller/computing types, it can be challenging to harmonize on an I/O product line which can accommodate such diversity. Users need modern distributed remote I/O platforms with easy connectivity to all types of field signals, support for a wide range of industrial network communication protocols, and other features making it simple to integrate field I/O signaling solutions.
From OT to CT to IT
Automation and IIoT applications may use individual microcontrollers, programmable logic controllers (PLCs), edge controllers, or even industrial PCs (IPCs) located on equipment or at factory sites. These controllers must collect field data, act on it, and perhaps transmit it to higher-level control room PCs, servers, or even cloud-based computing resources. Some designers identify three layers associated with these tasks:
- Operations technology (OT): This is where field information is collected via I/O, typically using PLCs, or sometimes IPCs.
- Computing technology (CT): This is where local/edge computing and analysis is performed on-site, sometimes in a PLC but more often in an edge controller or IPC.
- Information technology (IT): This is where powerful analytics, browser-based visualization, and much more are performed on-site or in the cloud.
Remote I/O is necessary so designers can install the hardware close to exactly where it is needed in the field, and then link the remote I/O to any type of controller or supervisory system using just one network cable. This minimizes field wiring and provides the most adaptable way for connecting OT signals up to CT and IT systems.
A Distributed I/O Solution
Some controller platforms offer their own “native” I/O solutions, but these may not interoperate well with other platforms. One way to provide to improve I/O signaling compatibility among many platforms is to choose a third-party solution conforming to industry standards, with the following characteristics (Figure 1):
- Convenient DIN-rail, modular form-factors.
- Push-in terminal blocks for easy wiring.
- Auto-addressing and LED diagnostics for best usability.
- Diversified options for high-speed fieldbus.
- Responsive performance.
Figure 1: The Dinkle iO-GRID C family of distributed/remote I/O is easy to install, wire, and commission. It provides useful diagnostics, along with flexible connectivity to higher level systems via a wide range of industrial network communication protocols.Dinkle International
Suitable I/O solutions should provide a variety of UL-approved and CE-certified power supply options, discrete and analog I/O, and communication adapter modules in compact form-factors, with modules clicked together as needed and then installed on a DIN rail. Removable push-in design terminal blocks facilitate easy initial installation, along with any required maintenance.
As the I/O is commissioned, an auto-addressing function delivers significant savings on the integration cost, and once in operation LED displays provide users with a clear and intuitive understanding of operational status. Ideally, I/O solutions include a high-speed on-board communication bus to ensure responsive performance and extensibility.
Although the preceding points are important, compatibility of any I/O solution with a variety of higher-level systems depends on support for high-speed network communication protocols, such as EtherNet/IP, PROFINET, EtherCAT, CC-LINK, and Modbus.
A consolidated remote I/O solution based on the preceding features and standards enables designers to use one product family for all their needs, simplifying design effort and hardware costs, while reducing spare parts inventories. Designers need only learn one platform, and they can avoid proprietary technologies.
Application Flexibility
Using third-party standardized remote I/O solutions gives designers complete architectural flexibility, with many options for scaling to meet project needs. For example, remote I/O can be used directly with local PLCs for equipment monitoring and control. Or, the same family of remote I/O hardware can be used for IIoT projects—sometimes in parallel with a control system so as not to disturb existing operations—with I/O points monitored and analyzed by edge controllers or IPCs.
In one facility, a food manufacturer used remote I/O in conjunction with field instruments, PLCs, and IPCs to monitor their material supply, dough making, freezing, and drying operations, and to present data via a webpage monitor. This allowed them to easily visualize real-time status, empowering them to increase productivity and reduce waste.
For an automated warehouse sorting system, there were many sorting stations requiring automation. The designer chose to distribute remote I/O points exactly where it was needed at each equipment location, and to connect all points to a Siemens PLC via PROFINET (Figure 2). This design reduced the overall cost of the system, while providing a scalable way to upgrade the number of points and features in the future.
Figure 2: For an automated warehouse sorting system application, designers used Dinkle iO-GRID C remote I/O installed as needed at numerous sorting stations to reduce cost and to provide coordination of all operations via one main PLC.Dinkle International
Industrial equipment designers should consider the many advantages of using remote I/O solutions which can integrate with any type of controller or computer as needed using standardized protocols, as these components provide a wide range of smart options.
---
Matt Hou is a sales engineer for Dinkle International and has been an integral part of the development of the Dinkle Corporation, USA subsidiary since 2018. Matt Hou holds a BAS Degree in Electrical Engineering from the University of Waterloo in Canada.