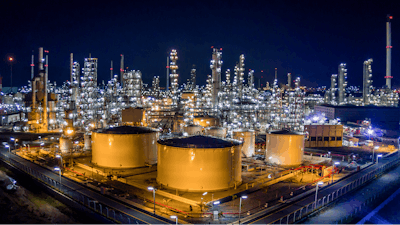
For decades refining and petrochemical organizations have focused on capturing Lessons Learned from STO events. Over the last several years many have improved by not only capturing the Lessons Learned but implementing solution for recurring issues in the preparation and execution processes and procedure for future STO events.
The concept of Risk Management has been around as long as Lessons Learned, but for many organizations effectively utilizing Dynamic Risk Management as a forward-facing process to eliminate completely, or mitigate as much as possible, known threats to the success of the STO event has not been a robust, nor fully implemented, process.
The industry is facing strong challenges to deliver on safety, quality coast and duration targets, implementing a Dynamic Risk Management process will help organization reach those targets.
Lessons Learned stands in stark contracts to Dynamic Risk Management. Lessons Learned is a backward-looking process that asks, “What went right and what can we improve for the next STO event?” While this exercise is legitimate the positive effects of a good LL process won’t be implemented until the next STO.
Typically, a single Lessons Learned workshop takes place 1 to 3 months after an event.
By this time some of the key stakeholders, namely contractors, are no longer available to participate, people have forgotten some of the causes of delays or the organization has lost or switched focus to more immediate concerns. This causes Lessons Learned lose its effect to capture all the issues and effectively develop mitigation measures for the next event.
Lessons Learned remain a valuable exercise and organizations should continue to debrief after each event.
Dynamic Risk Management with its emphasis on now, will have a greater effect on eliminating or mitigating the risks to the upcoming STO event.
Figure 1: Dynamic Risk Management is a structured approach for identifying assessing, prioritizing and mitigating uncertainties that may impact successful project delivery.
Dynamic Risk Management as forward-looking process asking, “What could possible go wrong during the preparation and execution of this STO event and what can we do now to mitigate or eliminate known risks?”
Dynamic Risk Management focuses the entire organization on making the current STO event as successful as possible. Dynamic Risk Management utilizes three to five risk identification/mitigation workshops during the preparation phase of an STO event.
The number of workshops is a function of the size and complexity of the event, with larger more complex events requiring more workshops to capture risks at each stage in the preparation phase.
Figure 2: Example of four Dynamic Risk Management Workshops during preparation phase for a Medium-to-High complexity STO event.
For all STO events the first risk identification/mitigation workshop should be held closely following the events kickoff meeting. The remaining one to four workshops should be held at the start of each phase of the preparation stage.
Your organization will have to adjust the number of workshops according to the size and the complexity of the STO event. Each Dynamic Risk Management workshop should be attended by a cross-functional group representing all departments with a role in making sure the STO event succeeds.
Dynamic Risk Management workshops are most effective when facilitated by a neutral third party who can ensure that the process provides the organization with valuable information as an outcome.
Identification:
Each of the participants is requested to identify two to three risk, non-equipment related, that they believe may occur during the upcoming event. Those contributing possible risk will rely on past Lessoned Learned, there own experience and information that they have relevant to the upcoming STO event.
Assessment & Impact Analysis:
During the DRM workshop the facilitator will enable the group to capture all possible risks in a formal event risk register. The attendees will then risk rank each risk to determine the possibility the risk will occur and the impact to the event if it does.
Mitigation:
Following each workshop, as part of the Dynamic Risk Management process, all or a subset of the workshop participants, will meet regularly to develop mitigation plans and assign action items to resolve each of the identified risks. Mitigations will be developed in order of relative importance, High – most likely to occur with the greatest impact to Low – least likely to occur with the lowest impact.
Monitoring & Reporting:
Each risk is assigned to an owner. The risk owner is responsible to ensure that the mitigation and action plans are implemented and completed so that the risk has as little impact on the success of the event as possible. Implement the defined mitigation measures.
he progress of implementing mitigation measures should be frequently reviewed and updates to the risk register should occur on a regular basis for all risks.
The STO Steering Committee should be made aware of which risk require their influence and guidance to address on-going concerns with High risks and those risks for which mitigations do not reduce the risk to a tolerable level.
Fully implementing a robust, forward looking, Dynamic Risk Management process will increase an organization’s focus on the current STO event.
This increased focus will have a positive effect on the targeted results for the event on safety, quality, cost and duration. By utilizing DRM to reduce or eliminate risks to the event the participants in Lessons Learned, at the end of the event, are less likely to say or hear someone say, “Well I knew that was going to happen”.
Mark Rigdon is manager at T.A. Cook Consultants. With over 18 years of consulting experience and having worked on projects across a range of different industries, Mark is currently dedicated to the asset intensive refining and petrochemical industries. He has provided leadership on client projects focused on turnaround excellence, maintenance work order process improvements and OEE. www.tacook.com/en