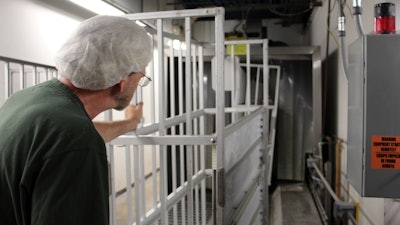
Automation Dynamics of Independence, MO makes automated equipment for the commercial laundry market. It holds numerous patents for equipment designed to efficiently process laundry in facilities that handle an average of 230,000 lbs of laundry per day for hospitals, hotels, restaurants and other venues with large volumes of laundry.
Though its primary products sort, count, weigh and route laundry through the wash process, it also makes automatic washers that clean and sterilize the carts on which laundry is transported to and from wash facilities.
The Healthcare Laundry Accreditation Council (HLAC) inspects and accredits laundries that process reusable textiles for healthcare facilities, a regiment that now includes elevated standards for laundry cart washers.
A recent cart washer installed at Madison United Healthcare Linen, a commercial laundry company that serves hospitals in southern Wisconsin, is among the most unique that Automation Dynamics has ever installed.
The Madison United plant is built into the side of a small hill, with loading docks on both the first and second levels. Laundry arrives and is sorted on the second level, and is then transported to the first floor where it is washed, processed and ultimately loaded on trucks to be taken back to the various hospitals.
When laundry arrives it is taken off the carts, and the carts are lined up to be cleaned and disinfected in the washer. The sterilized carts eventually need to be reloaded with clean laundry for transport back to the hospitals, so a system had to be developed to lower the carts to the first floor.
Unique Challenges
Lowering laundry carts the 14’-8” distance from the second floor to the first floor is a routine application for a PFlow Industries, Inc. vertical lift. Several unique challenges had to be addressed in designing the lift:
- Limited space between the cart wash discharge area and the placement of the lift required that the carts had to be automatically loaded on the lift;
- With only one cart on the lift per trip and no space outside the washer for carts to be staged, the flow of carts into the washer had to be controlled by the flow of carts entering the lift on the top floor;
- The lift had to accommodate multiple sizes and types of carts, some stainless steel varieties weighing 350 lbs, and some made of aluminum or plastic being considerably lighter;
- The lift is for high-cycle use, completing on average 260 trips per day.
Seamless, Controlled Operation
PFlow and Automation Dynamics engineers collaborated to design a system that integrated the controls of the cart washer and the vertical lift. Controlled by a PLC with Automation Dynamics proprietary software, the operation of the washer and lift are directly integrated to sequence the flow of carts through the washer and lift system.
The cycling of the system, which is initiated by the downward movement of the cart-loaded lift, is highly coordinated:
- A chain conveyor, similar to a car wash, hooks on to the wheels of a cart and pulls it through the washer;
- Once washed the cart exits the washer and slides down an incline onto the lift platform through an open gate;
- An electric eye senses that the cart is securely in place, and automatically closes the upper level gate and sends the lift down.
- Parallel bumpers attached to the lift platform hold the cart in place while traveling down. The bumpers are designed to firmly hold the various cart models and sizes;
- When at the lower level, the lift door opens automatically, but the cart sits on the platform until it is manually removed by an operator;
- Once the cart is removed the operator presses a button to close the gate and send the empty lift back up to retrieve another cart;
- When the lift arrives back to the upper level an electric eye senses the VRC is empty, prompting the wash conveyor to release the next cart down the incline and onto the lift platform, starting another cycle;
- The integrated controls hold the chain-driven conveyor from pulling a new cart into the wash until the most recently washed cart is securely on the lift and on its way down.
In addition to the standard safety measures such as interlocked gates and enclosures, the Madison United lift features a carriage operated safety barrier at the upper level to stop carts if the lift is not present. On the lower level a buzzer and light indicate that the lift is down and ready be unloaded. The alerts remain in effect until the operator removes the cart, shuts the gate and hits a clear button.
The other PFlow lift at Madison United is a hydraulic model installed in 1995 to move finished laundry and supplies between the two levels. It remains in peak operating condition.
Madison United Lift Details
- Model: M Series, 2-post mechanical lift with straddle carriage
- Capacity: 1,000 lbs live load
- Vertical Travel: 14’-8”
- Levels: 2 Speed: 25 fpm
- Useable Carriage: 5’-0” W x 7’-0” L x 7’-0” H
- Load Pattern: Z, pass-through