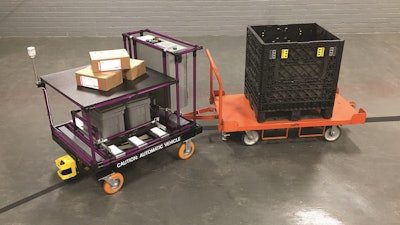
An automotive powertrain component manufacturer sought the expertise of Creform (Greer, SC) in once again developing a “hands free” system to move production parts and supplies from its warehouse to the assembly area, and to transport finished goods back from the assembly area to the warehouse.
Engineers developed a single-direction, one-ton drive Creform Tugger AGV to operate in a multi-shift mode with heavy-duty usage in mind, but with the need to be lightweight, flexible and affordable. The Tugger AGV was constructed with a heavy-duty steel base and a top structure built with rigid 28mm Creform pipe and metal components for its lightweight and flexibility benefit.
The AGV can tow two carts. The hitch is affixed directly to the base and is designed to handle the rigors of industrial towing. With this application, the starting and stopping forces are quite high, hence the need for a robust steel base. The hitch is mounted to a plate that bolts to the frame and is easily height-adjustable with basic tools to match the height of trailer tongue. In addition to towing, the AGV also features a utility load deck for miscellaneous boxes and supplies that can ride along with the tugger. Although heavy-duty in nature, the frame is designed so that the unit can be easily and safely lifted for maintenance with a forklift.
The Creform AGV Tugger follows a peel and stick magnetic tape guidepath that is easily and quickly installed and changed depending on the need. It follows a 1000 ft. path with a long single run and a loop at either end to reverse direction. In this application, the guidepath is covered with heavy- duty protective cover tape to give the surface mounted tape some visibility and durability. An embedded guidepath is available for high traffic areas. There are RFID tags embedded in the floor that can provide unique routing decisions and initiate other functions such as speed and obstacle sensor view changes.
The AGV tugger also features a convenient handle for manual movement. By raising the spring-loaded drive wheels off the floor with the electrically powered drive wheel release, the AGV can be pushed around as a manual Creform cart.
A unique feature to the system is an application specific countdown alarm. If the AGV is stopped or otherwise delayed for more than 30 seconds, an alarm sounds to get the attention of nearby associates. Other features of the unit include PLC with HMI interface on-board controls, 50 course and 128 commands control. The AGV Tugger boasts a 2200 lb. (1000 kg) load capacity, 121 lb. (55 kg) draw bar, can travel up to 131 ft./min. (40 M/min) and brakes for stopping and parking.
It is equipped with a 24-volt system powered by two 12-volt AGM batteries. In regular operation, the batteries are maintained by an opportunity charging system. The connection between AGV and the charging station is made via mechanical contacts and the charge station features a smart charger and 8-bit optical transmitter/receiver so the AGV and charge station can automatically communicate. Batteries are carried in boxes on a tray that is supported by Creform Placon rollers on the AGV as well as the battery transfer cart and back-up charging station. With matching roller heights, no lifting of the heavy batteries is required. The AGV unit features a Category 3 safety system with safety equipment that includes an audible warning device, flashing light, no- contact obstacle sensor (Laser Scanner) and E-stops.
The Creform System is used to create an array of material handling and efficiency enhancing devices and is a proven component in continuous improvement and lean manufacturing programs. The company partners with customers in developing and implementing these programs.
www.creform.com; 800-839-8823