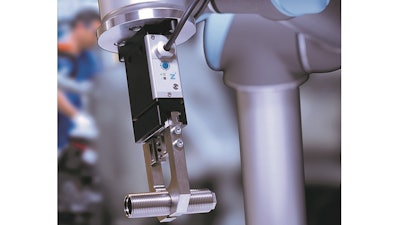
The Zimmer Group (Hickory, NC) is rounding off its line of grippers by launching a new series of electrically driven small parts grippers, which are designed to be very easy to control. With the GEP2000, the Zimmer Group is introducing a new series of electrically driven small parts grippers, which have been designed especially for assembly tasks and the handling of small parts. Grippers in this series, which starts with three models, offer adjustable gripping forces of between 80 N and 400 N and jaw strokes of between 10 mm and 16 mm to deal with these tasks.
The grippers, which have a mechanical self-locking mechanism to prevent the loss of the workpiece in the event of power failure, are equipped with an integrated control and are available in three control versions: With IO-Link, digital I/O and with digital I/O in combination with an analog output for querying the jaw positions.
- GEP2000 with IO-Link: Future-proofed Intelligence. In the IO-Link version, the gripper offers all the system-specific advantages of IO-Link, which means not only simple handling and operation, but also easy integration. By connecting a single cable, the gripper can receive data from or transmit data to the master controller. Parameters such as gripping force and gripping speed are set centrally. The gripper uses IODD (IO Device Description) to send signals to the higher-level control system. This results in a considerable time savings during initial setup or when replacing the gripper. IO-Link, how-ever, opens up new horizons for advanced diagnostic functions and predictive maintenance, which is reflected in improved machine availability. No additional hardware in the form of controllers is required thanks to this highly sophisticated control system.
- Digital I/O: As simple as a pneumatic valve. In the I/O version, the grippers operate as simply as a conventional pneumatic valve. The gripper opens when it receives a control signal, and the jaws are closed when it receives another one. No movement occurs without a signal. In this cost-effective version, a four-pole cable that supplies the gripper with electrical energy and with control data is all that is needed for the connection. A commercially available central distributor can be used to control several grippers at the same time. If you need to query the gripper position, this can be done via magnetic field sensors, for which two grooves are already provided in the gripper. The gripper is able to use these sensors to send a signal as soon as a set query position is reached (just like with a normal pneumatic gripper). We have developed a comfortable solution for how to adjust the maximum gripping force: It can be adjusted directly on the gripper using a potentiometer in four stages. This is not only quick and easy, but it also offers the advantage that the setting can be seen even if the power has failed or the gripper has been removed.
- Digital I/O with Analog Output: Accurately record the jaw position. For applications where you need more precise information about the position of the gripper jaws, the Zimmer Group offers a digital I/O version with analog query. An analog sensor, which outputs a voltage of between 0 and 10 volts depending on the jaw position, is already integrated in the grippers. This voltage can be evaluated using an analog card in the higher-ranking control, thus making it possible to determine the position of the gripper jaws with a measuring accuracy of less than 0.05 mm.
www.zimmer-group.de/us; 828-855-9722