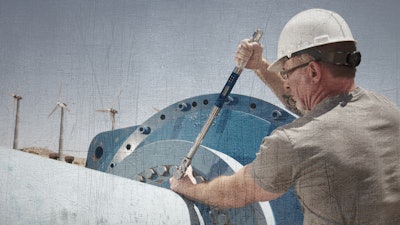
When purchasing a torque wrench from a distributor, many customers already know what type of tool they are looking for. In general, they’re well versed in what they need; they know their application well and the capabilities of the tool to get the job done correctly. Those types of transactions are relatively straightforward and easy to convert into sales.
But where distributors have a greater opportunity to demonstrate their value are to those price-conscious customers who walk in thinking they’re not going to invest a lot of money in a new torque wrench. That may very well be the case, leaving with a tool largely based on price. However, there’s a good opportunity to educate that customer by pointing out some basic distinguishing features of torque wrenches. Instead, they may walk out with a tool that’s not only a better fit for their job, but they’re leaving a little wiser, too.
People who are in the market for a torque wrench are looking for an accurate instrument. That’s the reason they’re buying a torque wrench after all because they have jobs that call for applying a certain amount of torque to fasteners. And for those customers who are basing their decision almost solely on price, do they think that any torque wrench will do? The short answer to that is yes … and no…
Applying Accurate Torque
What they may not realize is a higher-quality torque wrench tends to be more accurate and repeatable. These are two aspects people should consider when purchasing any torque product. Here’s why those are important.
If the technician is assembling shelves in a warehouse that require torque, accuracy may not be as vital compared to building an engine or repairing a wind turbine where under- or over-torquing fasteners can lead to dire results. If it’s a critical bolting job, a higher degree of accuracy is a must.
The two main styles of torque wrenches are mechanical and electronic. Mechanical torque wrenches are popular within many industries because they are relatively inexpensive, and it is the style that many technicians grew up with. While mechanical wrenches represent an older technology, they still perform well if the technician uses the tool correctly, stores it properly and keeps it accurately calibrated.
Electronic torque wrenches tend to offer greater accuracy than mechanical models. The chance of under- or over-torquing is reduced with electronic wrenches. Illuminating LEDs provide operational guidance, signaling the user that he or she is approaching the targeted torque.
Most mechanical torque wrenches come with about a +/- 3% accuracy rate; others may drifter higher to +/- 4%. Electronic torque wrenches are more accurate with a range of about +/- 2%.
Why Repeatability is Needed
The second aspect people need to consider when selecting a torque wrench is repeatability. Technicians using a torque wrench want to achieve a certain level of repeatability of out the tool, as well as a similar level of consistency to their processes on specific jobs. Often, companies have standardized maintenance procedures as a way to not only provide consistent, predictable results in their technician’s work, but also have documented data to back up their performance. Using torque wrenches that are repeatable and consistent day after day is one way to attain that.
Part of achieving consistency in torque wrenches is through calibration. Some wrenches come with a calibration certificate that certifies the tool’s accuracy. Having that certification at time of purchase provides valuable peace of mind in knowing the torque wrench is ready for use. Other wrenches offer calibration certification, but for an added cost. Again, if the job calls for applying torque to non-critical applications, certification may not be all that important to the customer. But many torque applications are significant to the overall operation and safety of a job; calibration certification is a central document to have.
Made in the U.S.A.
Another aspect to point out to customers are if torque tools and their components are made in the United States. Most people would agree that made in the U.S.A. comes with a connotation of higher quality and workmanship in comparison to offshore produced tools.
The ratchet head, for example, is an essential component of a torque wrench as its responsible for transmitting torque to the fastener. Ratchet heads that are made in the United States is a good selling point toward the overall quality of a torque wrench. Additionally, customers using torque wrenches with domestically manufactured components can likely get replacement parts quicker if the need arises.
The value of a distributor is to recommend a torque wrench that best meets their customer’s needs. If their job doesn’t require a high degree of accuracy, no reason to steer them that way, especially if they’re selling to a budget-minded customer. On the other hand, some torque wrenches offer high accuracy with many extra features and benefits that more complex applications call for. It boils down to advocating for the right tool, and brand with experience, that will get the job done efficiency and safely. That is a great way to earn repeat business.
Ryne Montemurro is the Product Manager for Williams (https://www.williams-industrial.com/us_en/). He can be reached at [email protected].