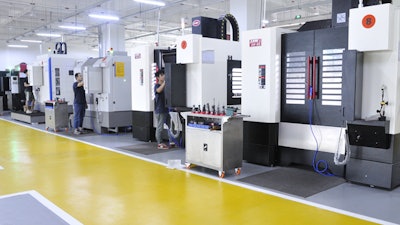
Globally, there is a growing demand for automation in major sectors. Industries such as aerospace, automobile, and healthcare require high precision levels, hence the need for CNC machining.
Manufacturers such as WayKen are utilizing customized CNC machining services to produce high-quality products for their clients. To maintain the quality in product development, manufacturers should have an efficient CNC machine shop.
If you want to maximize your machine shop's efficiency, here are some factors to look out for.
What Is A CNC Machine Shop?
A machine shop is a building or floor where the CNC machining process takes place. As a space for subtractive manufacturing, it holds all the machines and equipment involved in creating CNC parts. It also hosts all the company technical staff and machinists.
Different machines perform different functions in this type of shop. Businesses can use them in cutting, drilling, or shaping materials such as wood, plastic, and metal. The presence of a CNC machine shop in a small business significantly reduces the overall manufacturing costs.
A typical machine shop has several machines needed for subtractive manufacturing. These include drill press, grinding machine, milling machine, lathe, machining center, bandsaw, welding machine, metal cutting, and metal bending machines.
The equipment present in a machine shop may be equipped with Computer Numerical Control (CNC) technology or manual; operated by a machinist.
Factors That Affect Productivity of A CNC Machine Shop
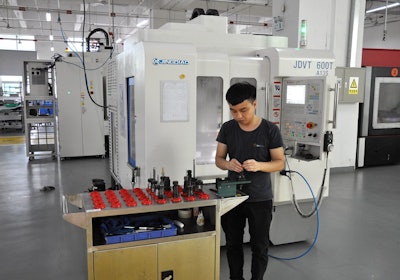
Maintaining high levels of productivity in the machining shop saves on operating costs and boosts operations efficiency. Let's examine some of the factors that could affect the productivity of the CNC machine shop.
Human Resource Efficiency
Machine shops often have a combination of automated and manually-operated equipment. For the manual ones, they require operators to handle them. Productivity in this setting is affected in two ways, the operator skills level and man to machine ratio.
The man-to-machine ratio is the number of machines one personnel runs. There should be an ideal optimum time to dictate which equipment the technical staff operates and at which intervals. Avoid idle times for both machines and operators for maximum productivity.
Inventory Management
A CNC machine shop deals with a lot of raw materials. To minimize time and resource wastage, there should be a proper inventory management system. Cutting tools, raw materials, and replacement parts need to be readily available at the shop, especially if stored in a different location.
Machinery and Tools Capability
The machine shops' most important assets are the machines and tools present. The only way to ensure you meet high productivity levels is by making sure your equipment is performing at the maximum capacity. Manufacturers need to invest in the latest CNC technology to meet the market and client demands.
A state-of-the-art machine shop will boost the overall profitability of the company. The turn-around time for clients will also be faster.
Production Planning
Manufacturers need to have a technical and production plan for the CNC process. A plan dictates the manufacturing flow and boosts productivity. During this phase, there is an allocation of resources for each stage of the fabrication process.
How to Maximize the Efficiency of A CNC Machine Shop
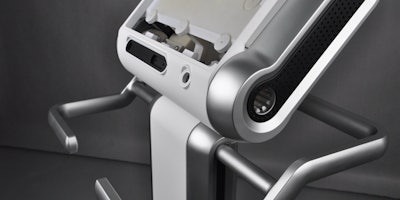
Manufacturing CNC parts requires specific precision. To achieve this, the process should be synchronous to produce high-quality outputs consistently. Here are some tips on how you can continuously maximize the efficiency of your CNC machine shop.
1. Upgrade and Invest In Your Machines
The machines are the lifeline of your shop. With the right tools for the job, you can produce CNC parts with speed and precision. Allocate a more significant portion of your budget to custom machines to achieve maximum efficiency.
2. Optimize the Machines' Capabilities
The modern era CNC machines are high-performance equipment. Avoid having them idle, which is an extra overhead expense. Utilize the machines to their optimum performance for high productivity.
Not pushing the machines to their maximum capacity can result in breakdowns which are an added expense to the company.
3. Train Your Staff
Machinist and technical staff in the CNC machine shop are an essential asset. Investing in them improves the efficiency of the shop. You can develop an apprenticeship program for them to improve their skills.
Furthermore, you can provide simplified documentation with instructions on operating the equipment to reduce errors. It would be best if you also educated them on workplace hazards, emergency response procedures, and the safe operation of the machines in your shop can go a long way in mitigating most of these risks to begin with.
4. Organize Your Floor Management System
To maximize the efficiency of your shop, take some time to organize your shop. Strategically design your layout to keep the shop organized and clean. You can collaborate with your staff in the shop to plan where all the tools need to be for a proper workflow for everyone.
With technology, the shop can utilize the latest software that allows for an integrated floor management system. This process integrates all business processes from the first contact to making payments. The automation reduces hiring costs and makes the shop's operations more efficient.
5. Have Realistic Expectations
Have a production plan for each day at the machine shop. Set up realistic expectations according to the tasks at hand, staff involved in the work, and machine capabilities. With a proper plan, you can meet the daily targets and avoid overworking the staff or the equipment.
The high demand for high-quality CNC parts often results in setting unrealistic goals. In the long run, this results in a backlog or missed deadlines which significantly slows down the company's efficiency. Boost your worker's productivity for higher efficiency.
Summary
Efficiency and productivity go hand in hand with CNC machining. There is demand for a high precision level with the increased demand for CNC parts in different industries.
Manufacturers can only meet these demands by investing in an efficient CNC machine shop. Maintaining an integrated workflow system for your human personnel and equipment is essential for the business.