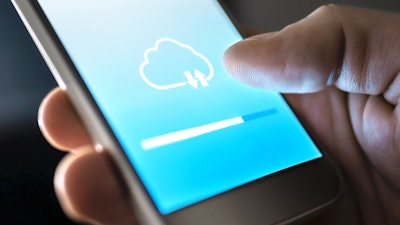
Across manufacturing, evolving and emerging enterprise asset management (EAM) technologies are revolutionizing entire operations. IoT and industry-specific technologies are powering more timely and accurate tracking, analysis, and strategic management of business-critical investments.
And that’s not simply within the walls of the facilities. A natural extension of all of this computing innovation and power is to deploy it to our field—where much of the crucial work takes place. Our mobile devices have redefined how we access information and conduct all aspects of our lives, and workers are ready to employ that connectivity and digital intelligence to work faster and smarter.
As many field employees are providing essential services during this time, the ability to track work done during equipment inspection and assessment has become even more important. Dispatched to the field for pandemic-specific cleaning activities, techs often discover other issues that need attention. With complete asset records in the palms of their hands, they can update the case management, non-conformity, and the condition finding checklist of that equipment.
A Game Changer
This mobile transformation can occur whether focused on the manufacture of pharmaceuticals, computer screens, or industrial chemicals. No matter what is being engineered, it all relies on precise equipment calibration, predictive asset condition assessment, consistent maintenance, and very specific regulatory requirements.
Connectivity and networking optimizes processes and accuracies by working across systems and breaking down information siloes. Everyone has access to the same EAM data, while sophisticated business intelligence enables analysis down to the zettabyte.
What does this mean in the field?
Mobile technologies target and direct the right field personnel, with the right skills, to the point of performance. While there, they have fingertip access to tool requirements and location. Real-time tracking means hands-on maintenance is recorded while the technician works, as their device and online work order captures the work as it’s happening. Mobile apps track warranties and service intervals, while appropriate sign-off signatures are captured digitally. Recordings, including videos and photos, can be stored in the asset maintenance file.
Meanwhile, back at the office, mobile location tracking provides managers with worker location so they can more efficiently dispatch to the next need.
Connecting Through the Cloud
Employing the full power of mobility is made easier by moving to a cloud platform. Manufacturers are catching up to other industries, recognizing the advantages of lower capital costs by eliminating the need to invest in on-premise software, hardware, and the talent to maintain them. Cloud costs can be shared among multiple enterprises, and storage and software can quickly scale for added capacity. A cloud system also easily connects industry-specific, third-party systems.
At the field level, the cloud collects and stores all technicians’ work, disseminating crucial data when and where it’s needed. It also allows unprecedented collaboration, deploying the same data sets and information to anyone who wants and needs it. Leadership can reply on the collected, real-time data as a single source of truth.
The cloud also poises organizations to not only meet today’s user needs and expectations but creates a foundation for what’s next—which is often unknown. Rapid innovation is the new normal, and a cloud platform allows for the growing complexity and sophistication needed to be nimble and ready for what is possible in the fully mobile future.
Mobility and optimized up time
A successful mobile strategy is all about the people who use it, and an intuitive, efficient system is the key to worker engagement. It also mitigates the organizational and worker stress brought by an unexpected malfunction.
A mobile field force is most prepared to address critical infrastructure failures, resulting in faster uptime. Consider mobile enablement at a large, multinational manufacturing enterprise. There is a sudden power outage. The supply chain director arrives at the office, and uses his phone to log into the company’s system. The facility manager receives an automated, urgent alert on the way to work. Pulling her car over to check her phone, she knows to grab a flashlight upon arriving at work.
Meanwhile, the issue is quickly identified as a short circuit, caused by something as simple as a burned-out fuse. The manager alerts her technician, who is at another site, via text. The tech checks his fuse supply on his smartphone. He has the correct fuses and returns to the site, getting the building back online and into full production.
As we know, it’s not just field techs who are increasingly relying on mobile technologies to do their jobs. As the last few months have shown us, the shift to a more remote work culture is affecting workers across industries and functions. With the right technology in hand, this transition can be easier, and maintain connections across the workplace.