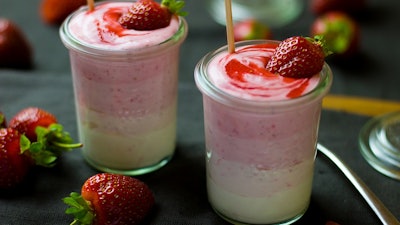
Who doesn’t love a sandwich from Subway? Apparently, there are 37 million possible sandwich variations, made possible through different filling, salad, bread and condiment combinations. The Industrial Internet of Things (IIoT) has added a new dimension to the capabilities of food and beverage manufacturing. Mobile devices, improved connectivity, and the ability of sensors, parts and machines to record, transmit and interpret information are leading new approaches to how food manufacturing is done.
This new automation network allows for devices to connect and communicate with each other, and with workers in the industry. Massive databases can collect, store, and report on data from myriad sources and systems, allowing software to report on performance, detect issues, and schedule or perform maintenance in ways that were not possible just a few years ago.
Automation has long been a part of food manufacturing, but there is one area that hasn’t felt the benefit just yet — customization. Even the likes of automation aficionados such as Ocado, a UK retailer that has thousands of robots automating its warehouses, continue to use humans for customization. For example, selecting the right cuts of meat for packaged products.
From a consumer perspective, Coca-Cola set the scene with its 2014 marketing campaign, that allowed customers to put their own name onto drinks bottles. While this was label-focused project, rather than changing the actual beverage, it demonstrated an ability to output customized products on a large scale.
It makes sense that customization is becoming more prevalent in the food industry, and there is a growing need to have highly flexible, automated machinery that can output customized products at high volumes.
So, how can this be put into practice? An illustrative example could be the production of fruit yogurt. This yogurt may have variant volumes in fruit compote ratio, sugar or sweetener content, lactose content, dairy content and so on. Heck, you could even choose to put the customer’s name on the label for good measure. But, how is this achievable on a standard production line?
To achieve a high level of flexibility and allow customers to choose exactly how they like their yogurt, it requires expert networking of production lines. Manufacturers cannot afford to program a new production project for each variant. However, by using IIoT devices and machinery, there are ways to command machinery to respond to customer orders automatically.
With intelligent SCADA software, and HMI displays from EU Automation, custom orders can automatically trigger the relevant dispensers in a manufacturing plant. Consider this as an example: A customer requested strawberry compote in their yogurt. Intelligent control software could then trigger the output of the strawberry compote vat into the yogurt pot. The ratio of compote to yogurt could be precisely altered as per the customer’s request, using 3D vision systems to sense fill level.
Adding yogurt on top of the fruit compote could also be customized. Vats of standard yoghurt, low fat yogurt, dairy free yogurt or lactose free yogurt could all be triggered to output at certain commands, through this integration with customer order data and intelligent control of the manufacturing plant.
Of course, this yogurt example is just that, an example. The scope for automated customization in food manufacturing can provide more than a build-your-own, yogurt extraordinaire.
The coordination and visualization of order preferences, processes and outputs turns customization from a strictly-human process, into an automated one. This means the market for customized food is capable of scaling, unrestricted by the previous limitations in production. Using this technology, manufacturers can expand their product ranges and introduce new variations of products, without the costs associated with planning, programming and building a brand-new production project.
For this to be a reality, food businesses need to assess their automation flexibility, and begin to use this increased capacity to introduce new product lines and variants, this will allow them to get ahead of the consumer food trends that are just around the corner