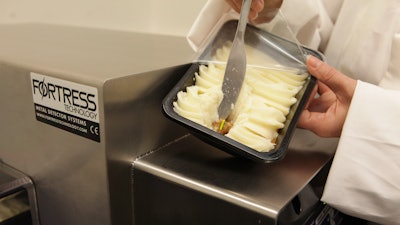
The FDA final rule on Requirements for Additional Traceability Records for Certain Foods becomes applicable in less than 12 months (from January 2026). The foods it will apply to are generally in fresh form, although it does also apply to finfish, crustaceans, and shellfish, in both fresh and frozen forms, as well as designated produce on the FDA’s Food Traceability List (FTL) that are used in fresh form as part of a multi-ingredient food.
This could include, for example, a sandwich that contains salad and tomato slices. All these applicable foods within the supply chain will need to ensure that their communication platforms are robust enough to supply traceability records to the FDA within 24 hours.
Although rolling out in January 2026, the Food & Drug Administration (FDA) assures processors that it is maintaining its ‘educate before regulate’ ethos. This means routine inspections are unlikely to commence until 2027 to ensure traceability information can be cascaded among all applicable entities in the supply chain.
Despite this lead time, Fortress Technology has observed significantly more requests for data integration support in the last 12 months. Indicative that food processors clearly prefer to get ahead of the curve.
Tech-Enabled Event Tracking
There are already various digital record keeping options available. The data extraction technology selected often depends upon the size and the existing capabilities of the food processor. Generally, electronic records rather than paper print outs are advised by the FDA, as these can be held in a secure and traceable way. For example, information cannot be inserted retrospectively, and records cannot be falsified or altered in any way.
Most digital metal detectors today feature on-board data logging and time stamped data that can batch statistics to be collected by a person from each machine. Although this may capture every metal detection event to satisfy the reporting requirements and general food safety standards, this machine-by-machine data collection process can be labor intensive and impact productivity.
Automated data collection removes the risk of human error and makes sure records are instantly accessible. Most solutions, e.g. Contact 4.0, can schedule reports to be sent at regular intervals direct from the machine to appointed internal food safety persons and quality control decision makers. From viewing live event logs and performance verification checks, to quickly accessing records to support a recall event, processors can then stream and share performance data more rapidly.
Real-time system monitoring becomes even more sophisticated when multiple inspection machines are networked. For example, Contact 4.0 provides a high level dashboard that allows users to assess the health of all connected Fortress Technology inspection systems at a glance.
To extract the data, authorized users could simply log into the web interface via a browser on any networked device, including laptops and tablets. This essentially means that reports could be sent electronically and within minutes to the FDA via a web portal in accordance with Section 204(c) of FSMA.
Processors are already using digital reporting tools and data features extensively to support reporting and to ensure food safety is not compromised.Fortress
Unified Reporting Platforms
Utilizing automated data integration technologies like OPC-UA Adapters and Ethernet/IP Adapters provides those with established data reporting processes the opportunity to merge inspection data and stream within the firewall of a business network. With these solutions by Fortress Technology, data tags defined by each food factory are converted in real time to an internal business database. These could be pulled into enterprise resource planning (ERP) or other structured plant monitoring systems, providing valuable oversight to support flexible production.
As more and more of the equipment in food factories become connected, the interoperability of OPC-UA architecture makes it more straightforward to establish centralized data control. For example, it allows the live data from multiple metal detectors to feed in real time into a client’s central server.
Additionally, the OPC-UA architecture is supported by most major automation technology suppliers. Making it easier to synchronize data generated by multiple machines in smart processing environments.
Monitoring Vision
By the time the FDA final rule is applied to routine inspections, vision solutions will likely feature strongly in the traceability process. For example, vision could be integrated more into combination metal detection and/or X-ray and checkweighing systems.
Rather than collecting data individually by machine type, these combination machines may use vision sensors to collect comprehensive data on each inspected pack, including details on weight, size, visual integrity, contaminant detection results and adherence to quality standards. This hub of valuable data could also help to indicate when something isn’t right within the production line, which plays a huge role in increasing hazard traceability.
Takeaways
There are multiple data collection and reporting options in food inspection and many of these tools have been available for some time. This makes them well tried and tested.
Although the mandating elements for processors that manufacture, process, hold or pack certain foods can seem a little extreme, it is worth examining how your existing frameworks could be used or adapted. There will inevitably be communication platforms in place that can be applied relatively quickly to help minimize contaminated foods reaching the marketplace. Collaboration will be essential. Our advice is to start the conversations with your equipment suppliers now to see what is feasible and develop traceability plans early, as 12 months comes around quickly.
Eric Garr is a regional sales manager and food safety specialist at Toronto-based Fortress Technology.